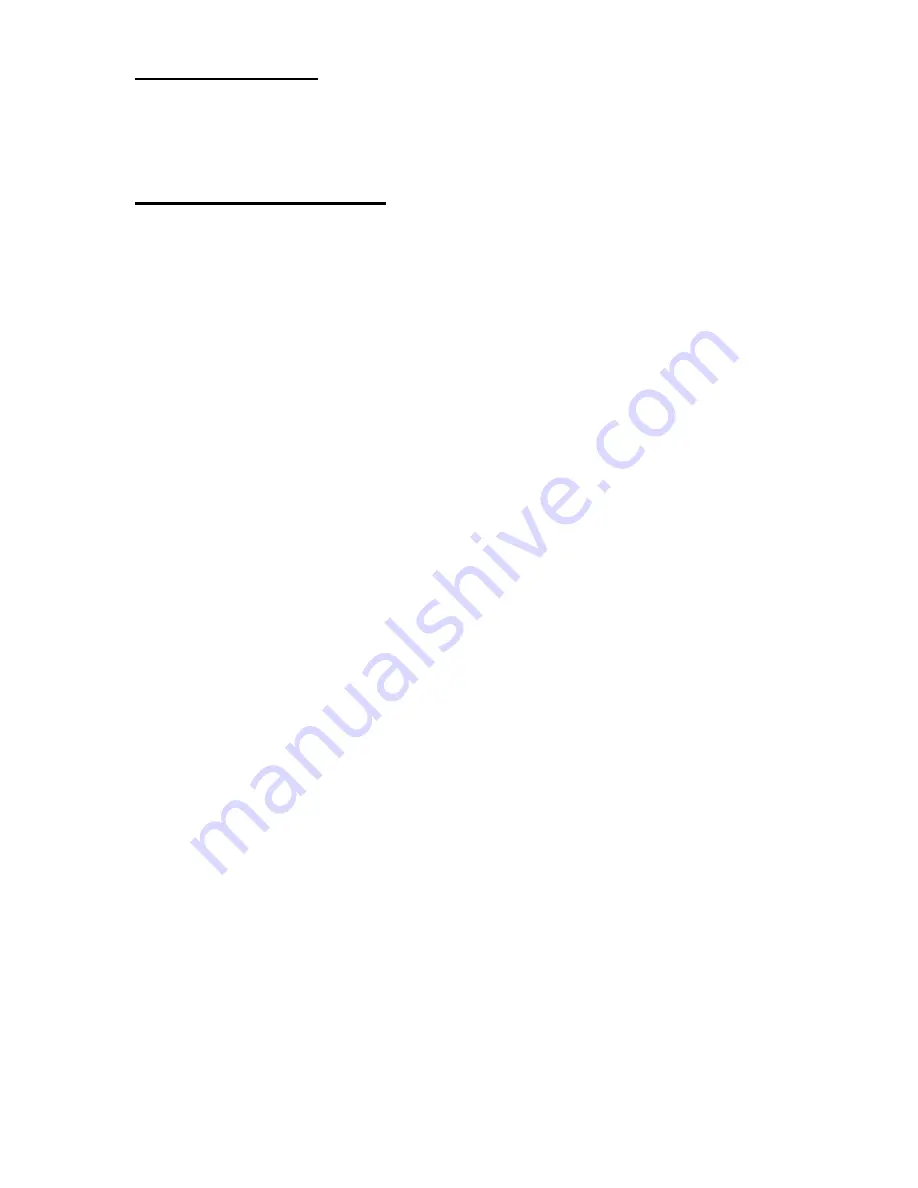
COMPACT-MULTI – INSTALLATION/OPERATION MANUAL
5IM-OF-K4C0-01
Jun/12
5
2.4 MULTI - POSITION
The Compact-multi is designed to operate in either upflow, downflow or horizontal mode. The
breech is convertible from front to rear by switching the breech pipe and cover plates. The
burner is always installed in an upright position by four nuts.
2.5 PLACEMENT & VENTING
Furnace installation should conform to the required installation code for oil-fired equipment
(USA: NFPA 31, Canada: CSA B139).
UPFLOW
Install the furnace close to chimney or vent and central to ductwork. The
furnace may be placed on a combustible floor or, if required, on a Granby
Appliance Stand or four (4) rigid blocks. The floor must be strong enough
to carry the weight of the furnace. The furnace is shipped in upflow
configuration.
DOWNFLOW
Install the plenum and sub-base as shown in Figure - 5 or the illustration
included with sub-base kit (K4C-KA-0500-00). A sub-base is required to
support the furnace. This sub-base maintains the clearances to
combustible materials through the floor and provides a convenient
attachment to the plenum. For furnaces installed on a combustible floor,
ensure that the requirements of the authorities having jurisdiction are
satisfied.
HORIZONTAL
In suspended horizontal positions four 3/8”-16 x 4” eyebolts and 3/8” nuts
are use to suspend the furnace. Determine the appropriate side and
remove the knockouts. Four weld nuts (3/8 - 16 UNC) are concealed
behind knockouts on either side of the furnace. For installations where the
furnace will be supported from below, use 4” long 3/8” UNC bolts as
adjustable legs. Eyebolts complete with locking nuts are available. The
locking nuts should be threaded on the eyebolt 3/4” to 1”. This provides a
stop for the eyebolt.
CHIMNEY/VENT
Connect the furnace to a chimney/vent system of size and condition
required by the NFPA 31 (USA) or CSA B139 (Canada) code. Furnace is
approved for factory built chimney type “L” vent. Breech is certified for 5”
vent pipe. Keep vent/flue pipe as short as possible with min. 1/4” per foot
upward slope. Use approved fitting through a wall. Vent/flue pipes MUST
NOT pass through a ceiling. Maximum flue gas temperature is 575°F.
THROUGH-THE-
Furnace is approved for Granby Direct Vent with Riello burner.
WALL VENTING
COMBUSTION &
Install openings and ductwork to the furnace room to provide fresh outside
VENTILATION AIR
combustion and circulation air for cooling the furnace casing, as
installation codes require (USA: NFPA 31, Canada: B139). If installed in
a closed room, provide two free air ventilation openings of at least 8” x 12”
(96 sq. in.) free flow area near ceiling and floor. Oil burners must have
sufficient air to allow vent systems to operate properly. See furnace
operating label. Not applicable to Direct Vent.