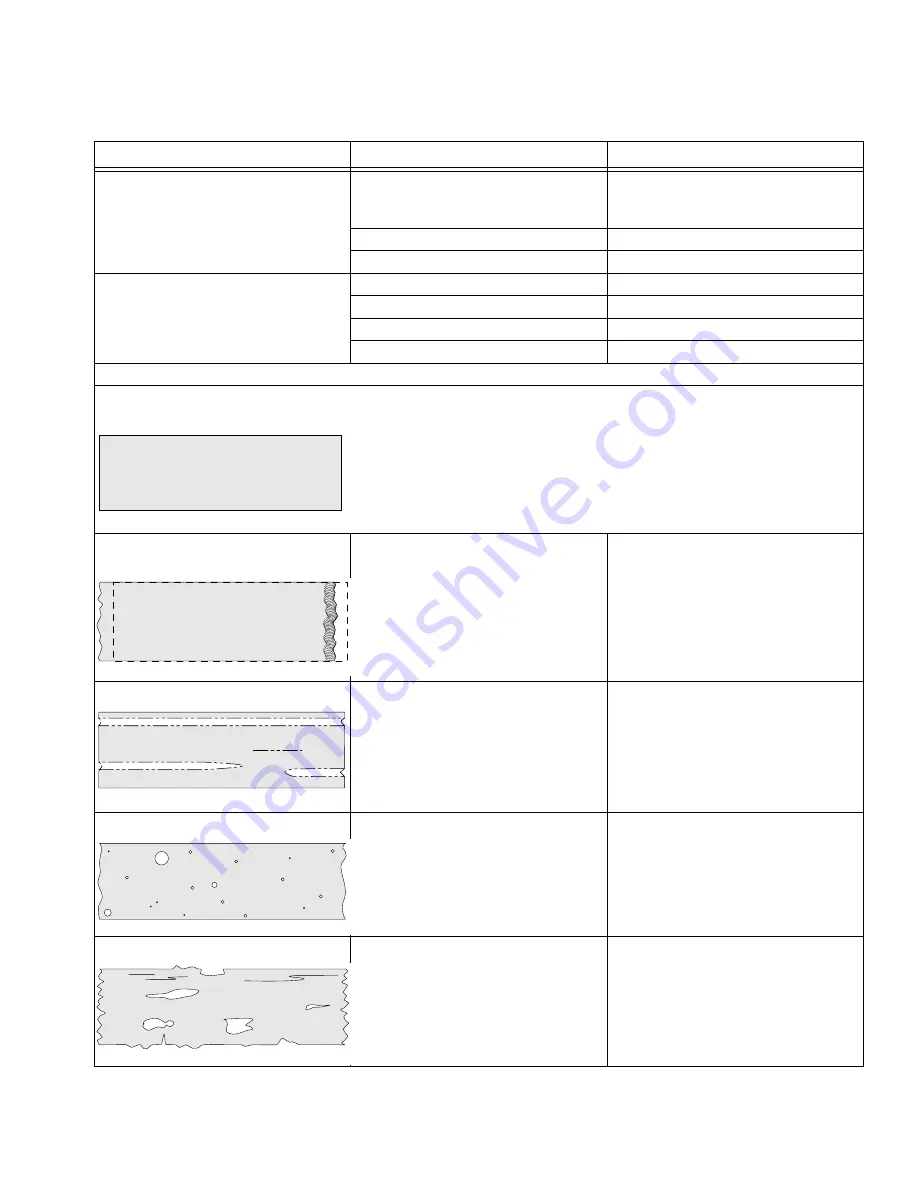
Troubleshooting
3A1320L
39
Applying Material
Problem
Cause
Solution
Ragged line edges when extruding
Dirty screed box
CAREFULLY
clean box. Discharge
opening and screed box plate run-
ners need to be free of debris.
Cold material temperatures
Heat material as required.
Marking speed too fast
Slow ThermoLazer speed.
Rough material surface when extrud-
ing
Overheated material
Reduce heat.
Moisture on road surface
Allow road surface moisture to dry.
Rough road surface
Smooth road surface.
Screed box low on material
Add material to screed box.
EXAMPLES:
Correct line application
will produce a full straight line with sharp edges; correct color,
thickness and width; a firm bond to the surface; and have uniform reflectivity.
Insufficient adhesion (material bulges
at beginning of line)
•
Material temperature too low
•
ThermoLazer speed too fast
•
Debris on road
•
Surface temperature too cold
•
Raise material temperature.
•
Decrease speed of
ThermoLazer.
•
Clear debris from road.
•
Wait for temperature of surface
to raise.
Rough and bumpy line
•
Debris on surface
•
Crust from overheated material
•
Debris caught in screed box
•
Material not covering road high
spot
•
Clear debris from surface.
•
Lower material temperature.
•
Clean debris from screed box.
•
Adjust screed box line thickness.
Gas bubbles in line
•
Moisture or solvent on surface
•
Material is overheated
•
Remove solvent from surface.
•
Lower temperature of material.
Ragged edges and gaps in line
• Material temperature is too low
• ThermoLazer speed is too fast
• Raise material temperature.
• Wait for change in ambient condi-
tions to remove moisture.
• Reduce ThermoLazer speed.
ti14507a
ti14508a
ti14509a
ti14510a
ti14511a