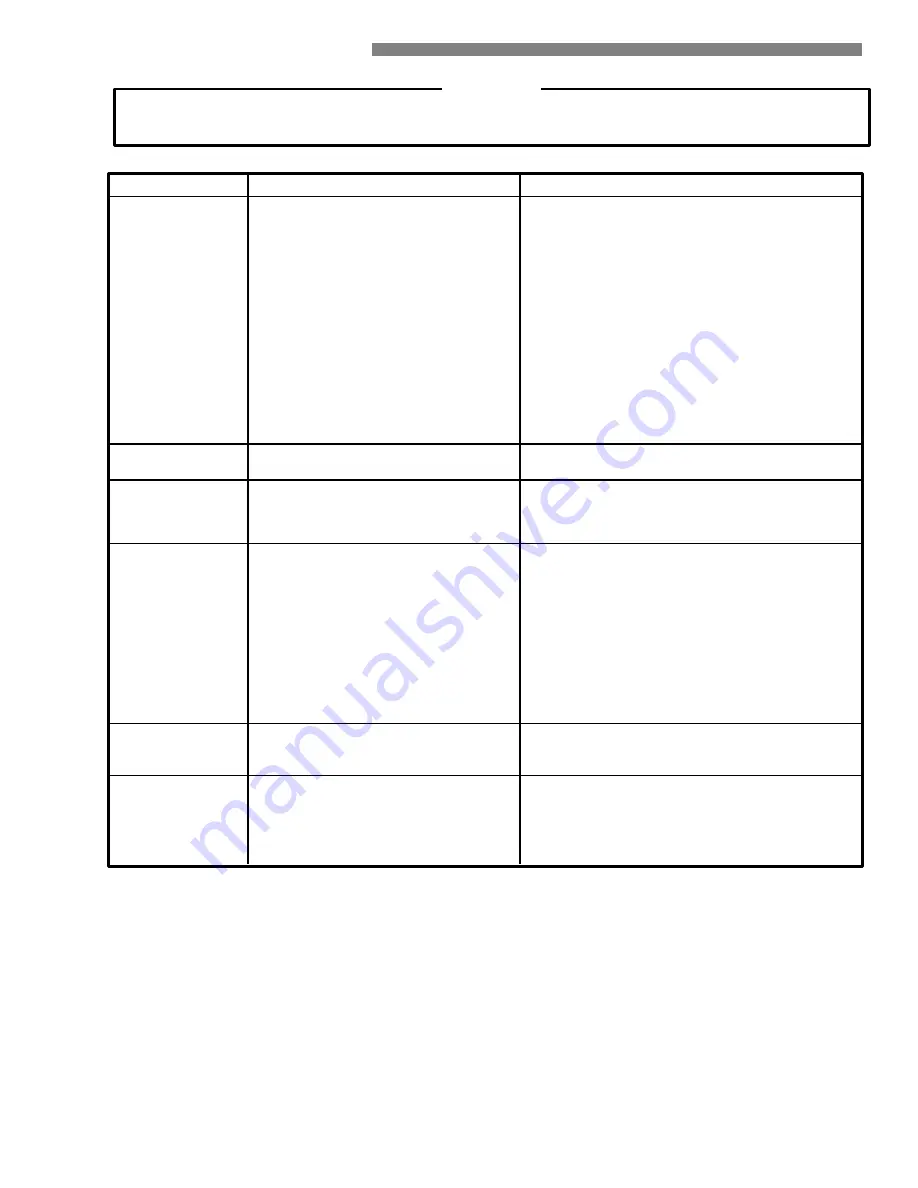
9
308-534ą9
TROUBLESHOOTING CHART
WARNING
To reduce the risk of serious bodily injury, including fluid injection, splashing in the eyes or on the skin, or
injury from moving parts, always follow the
Pressure Relief Procedure Warning
before proceeding.
PROBLEM
CAUSE
SOLUTION
Low pressure and/or
pump runs rough
Replace with tip of proper size.
Clean. Check more frequently.
Check filter. Replace packings. See PUMP SERVICE.
Check water flow rate to pump. Unit must have a
minimum 55 gallon float valve controlled water holding
tank.
Tighten or replace.
Clean inlet and discharge valve assemblies. Check
filter.
Check garden hose, may be collapsed or kinked.
Replace worn valves.
Replace high pressure hose.
Worn or wrong size tip.
Inlet filter clogged.
Worn packings, abrasives in water or
natural wear.
Inadequate water supply.
Belt slippage.
Fouled or dirty inlet or discharge valves.
Even a small particle can cause the valve
to stick.
Restricted inlet.
Worn inlet or discharge valves.
Leaking high pressure hose.
Water leakage from
under pump manifold
Install new packings. See PUMP SERVICE.
Worn packings.
Water in pump
Humid air condensing inside crankcase.
Worn packings.
Oil seals leaking.
Change oil as specified in MAINTENANCE.
Install new packings. See PUMP SERVICE.
Install new oil seals. See PUMP SERVICE.
Frequent or
premature failure of
the packings
Scored, damaged or worn plungers.
Abrasive material in the fluid being pumped.
Inlet water temperature too high.
Overpressurizing pump.
Excessive pressure due to partially plugged
or damaged tip.
Pump running too long without spraying.
Running pump dry.
Install new plungers. See PUMP SERVICE.
Install proper filtration on pump inlet plumbing.
Check water temperature; may not exceed 160
F.
Do not modify any factory–set adjustments. See
EQUIPMENT MISUSE HAZARD.
Clean or replace tip. See Installing and Changing Spray
Tips.
Never run pump more than 10 minutes without
spraying.
Do not run pump without water.
Strong surging at the
inlet and low pressure
on the discharge side
Foreign particles in the inlet or discharge
valve or worn inlet and/or discharge
valves.
Clean or replace valves. See PUMP SERVICE.
Unit will not start
Unit not plugged in.
Electrical service off/GFCI activated.
Thermal overload has tripped.
Check power cord.
Check fuse/circuit breaker. Check for proper grounding.
Press reset button on motor for 1 phase units. Press
stop button on the motor starter for 3 phase units.