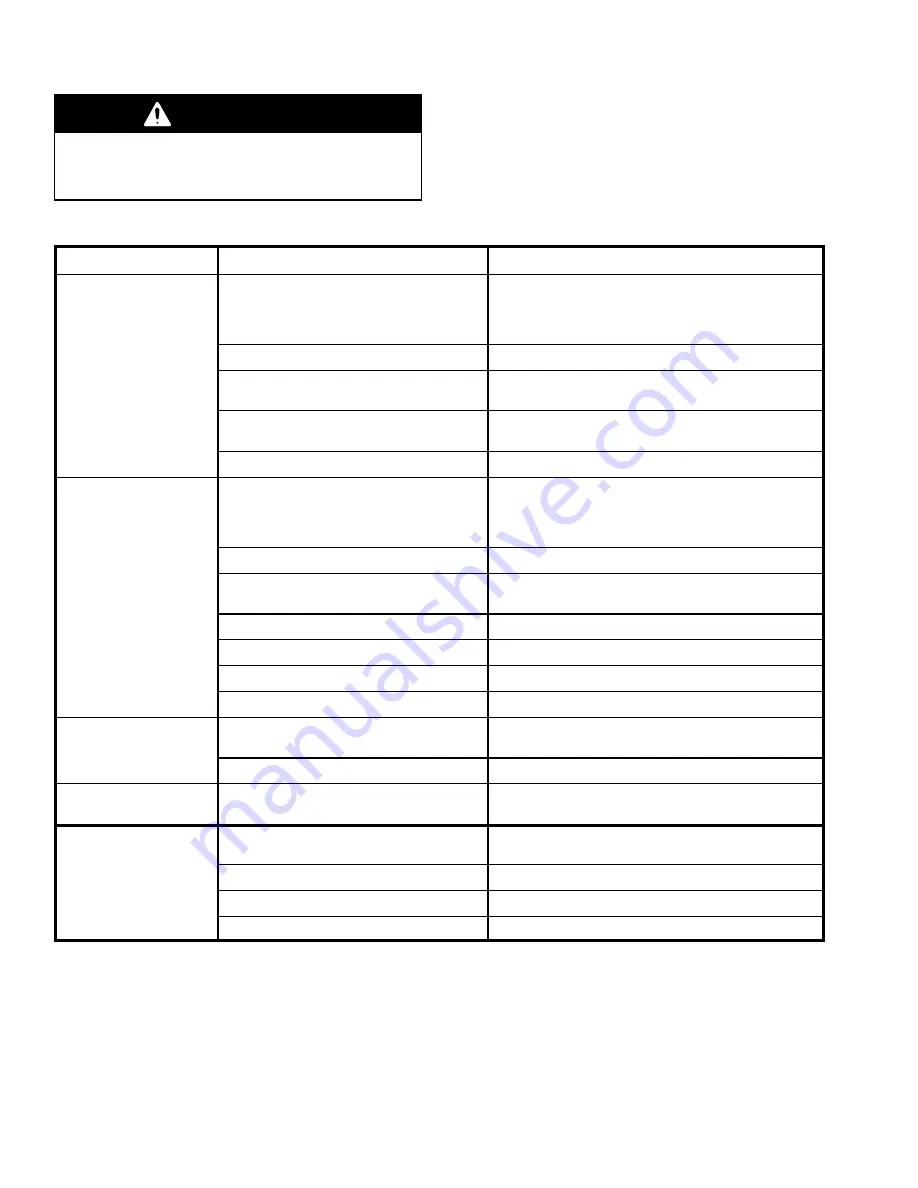
12
309224
Troubleshooting
WARNING
To reduce the risk of serious injury whenever you
are instructed to relieve pressure, always follow the
Pressure Relief Procedure
on page 10.
Before servicing this equipment, always make sure to
relieve the pressure.
NOTE:
Check all possible problems and solutions
before disassembling the pump.
PROBLEM
CAUSE
SOLUTION
Pump fails to operate.
Inadequate air supply pressure or restricted
air line.
Increase air supply (see Technical Data on page
NO TAG).
See Maximum Working Pressure warning on page 8.
Clear line.
Closed or clogged air valves.
Open valves; clean.
Obstructed fluid hose or gun/valve;
fluid hose ID is too small.
Open, clear.* Use hose with larger ID, or use shorter
hose.
Dirty, worn, or damaged air motor parts.
Clean or repair; see pages 20 to 25. Lubricate with
grease.
Obstructed priming tube.
Open, clear.
Pump operates, but out-
put low on both strokes.
Inadequate air supply pressure or restricted
air line.
Increase air supply (see Technical Data on page
NO TAG).
See Maximum Working Pressure Warning on page 8.
Clear line.
Closed or clogged air valves.
Open valves; clean.
Obstructed fluid hose or gun/valve;
fluid hose ID is too small.
Open, clear.* Use hose with larger ID, or use shorter
hose.
Exhausted fluid supply.
Refill and reprime or flush.
Air leaking into supply container.
Check follow plate or inductor plate seal.
Fluid too heavy for pump priming.
Use inductor or follow plate.
Worn seals in displacement pump.
Replace seals. See page 18.
Pump operates, but out-
put low on downstroke.
Fluid too heavy for pump priming.
Use inductor or follow plate.
Held open or worn intake valve or seal (105).
Clear valve; replace seal. See page 18.
Pump operates, but out-
put low on upstroke.
Held open or worn piston valve or seal (103).
Clear valve; replace seal. See page 18.
Erratic or accelerated
pump speed.
Exhausted fluid supply.
Refill and reprime or flush.
Fluid too heavy for pump priming.
Use inductor or follow plate.
Held open or worn piston valve or seal (103).
Clear valve; replace seal. See page 18.
Held open or worn intake valve or seal (105).
Clear valve; replace seal. See page 18.
*
Relieve the pressure,
and disconnect the fluid hose. Turn on the air. If the pump starts when the air is turned on, the clog is in
the fluid hose or dispense valve.