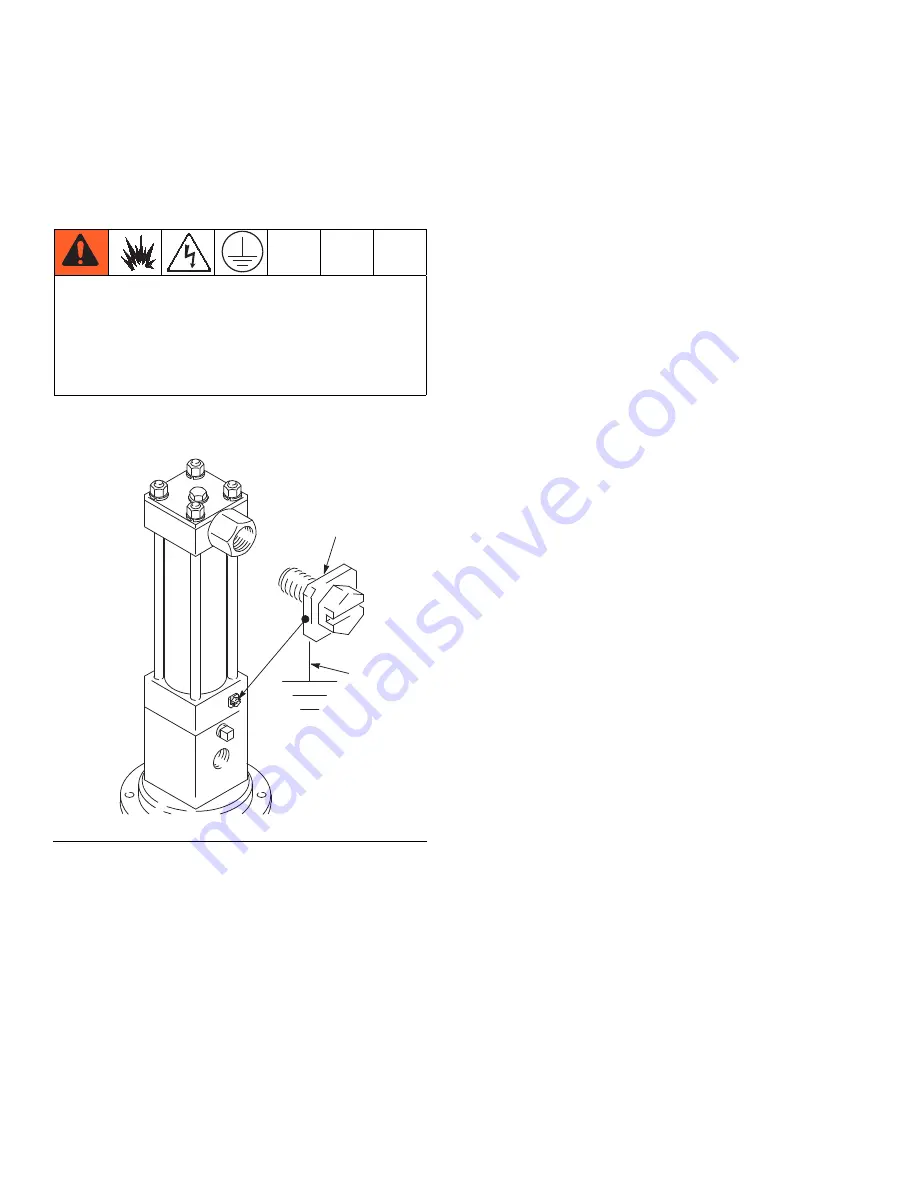
Installation
4
308155U
Installation
Grounding
Pump:
Use ground wire and clamp as shown in F
IG
. 1.
Hydraulic hose and fluid outlet hoses:
use only elec-
trically conductive hoses
Hydraulic power supply:
Follow manufacturer’s rec-
ommendations.
Any pails used when flushing:
Use only metal,
grounded pails when flushing. Make firm metal-to-metal
contact between the metal part of the dispense valve
and the pail. Use the lowest possible pressure.
To ground the pump:
Remove the ground screw (Z)
and insert through the eye of the ring terminal at end of
ground wire (Y). Fasten the ground screw back onto the
pump and tighten securely. Connect the other end of the
ground wire to a true earth ground. (F
IG
. 1)
The equipment must be grounded to reduce the risk
of static sparking and electric shock. Electric or static
sparking can cause fumes to ignite or explode.
Improper grounding can cause electric shock.
Grounding provides an escape wire for the electric
current.
F
IG
. 1
Y
Z
Содержание Dyna-Star 224741
Страница 27: ...Notes 308155U 27 Notes ...