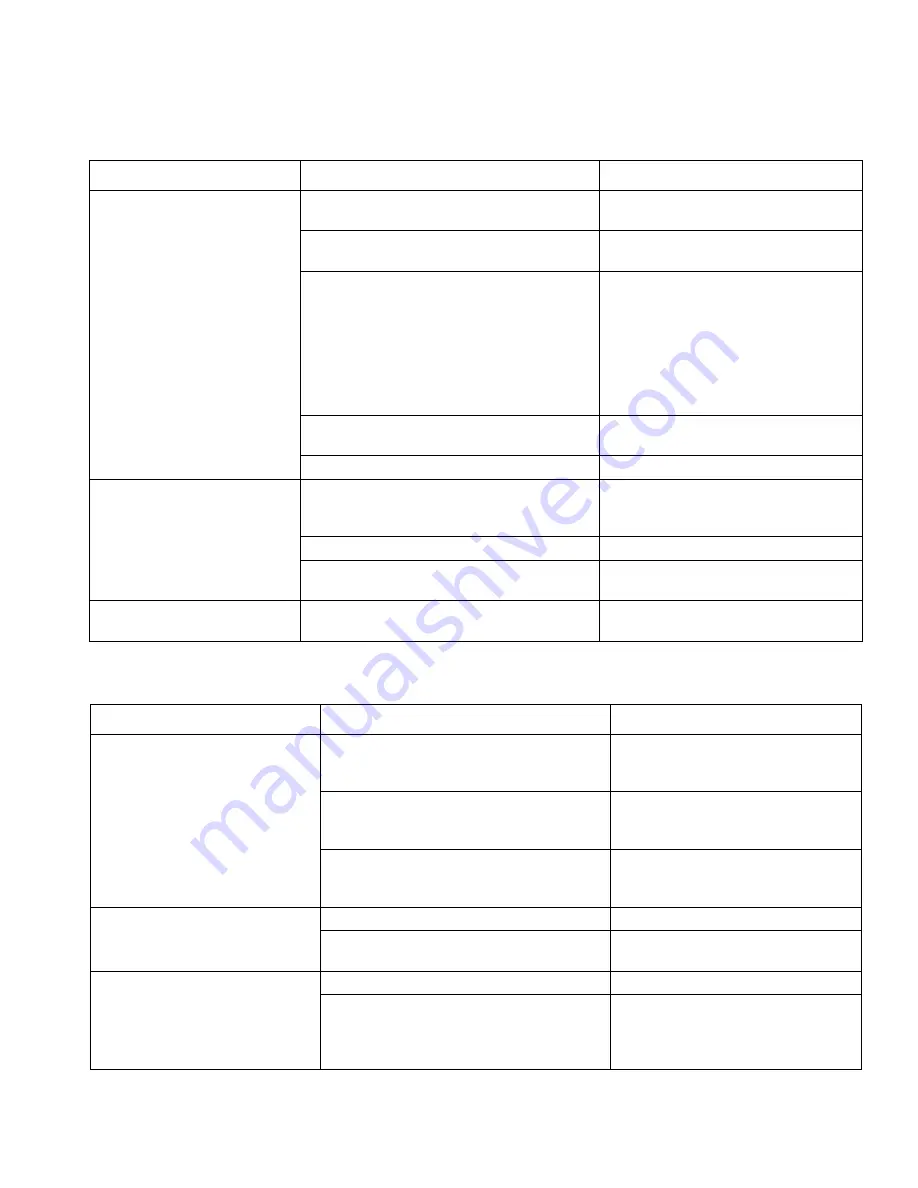
Troubleshooting
3A0245A
17
Low or Fluctuating Output (continued)
Electrical Short
PROBLEM
CAUSE
SOLUTION
Motor runs and pump strokes
No material supply.
Refill hopper and re-prime pump.
Clean hopper strainer.
Loose fittings.
Tighten; use thread sealant or sealing
tape on threads if necessary.
Intake valve ball and piston ball are not seat-
ing properly.
Remove intake and piston valves and
clean. Check balls and seats for nicks or
obstructions; replace if necessary, page
18. Also check piston valve seat for
hardened material or nicks and replace
if necessary. Clean hopper before using
to remove particles that could clog
pump.
Leaking around throat packing nut which may
indicate worn or damaged packings.
Replace packing, page 18.
Pump rod damage.
Repair pump.
Motor runs but pump does not
stroke
Displacement pump pin (damaged or miss-
ing).
Replace pump pin if missing. Be sure
retainer spring (76) is fully in groove all
around connecting rod.
Connecting rod assembly is damaged.
Replace connecting rod assembly.
Gears or drive housing.
Inspect drive housing assembly and
gears for damage. Replace if needed.
Motor intermittently stops while
applying material
See RF Problems, page 18.
PROBLEM
CAUSE
SOLUTION
Building circuit breaker opens as
soon as power switch is turned on.
CAUTION
Any short in any part of the motor
power circuit will cause the control
circuit to inhibit drywall feed pump
operation. Correctly diagnose and
repair all shorts before checking
and replacing control board.
Electrical wiring insulation damaged, termi-
nals fit loose or are damaged. Also wires
between motor control and motor.
Repair or replace damaged wiring or
terminals. Securely reconnect all
wires.
Motor armature is shorted.
Replace motor. Inspect windings for
burns. Perform motor control board
diagnosis.
Motor control board.
Replace with a new control board if
necessary. Perform motor control
board diagnosis.
Building circuit breaker opens as
soon as unit is plugged into outlet
and unit is NOT turned on.
Basic Electrical Problems, see page 15.
Perform necessary procedures.
For damaged or pinched wires in pressure
control.
Replace damaged parts.
Drywall feed pump quits after unit
operates for 5 to 10 minutes.
Basic Electrical Problems.
Perform necessary procedures.
Check electrical supply with volt meter.
Meter must read:
210-255 Vac for 220-240 Vac models;
85-130 Vac for 100-120 Vac models.
If voltage is too high, do not operate
drywall feed pump until corrected.
Содержание 257100
Страница 30: ...Notes 30 3A0245A Notes...