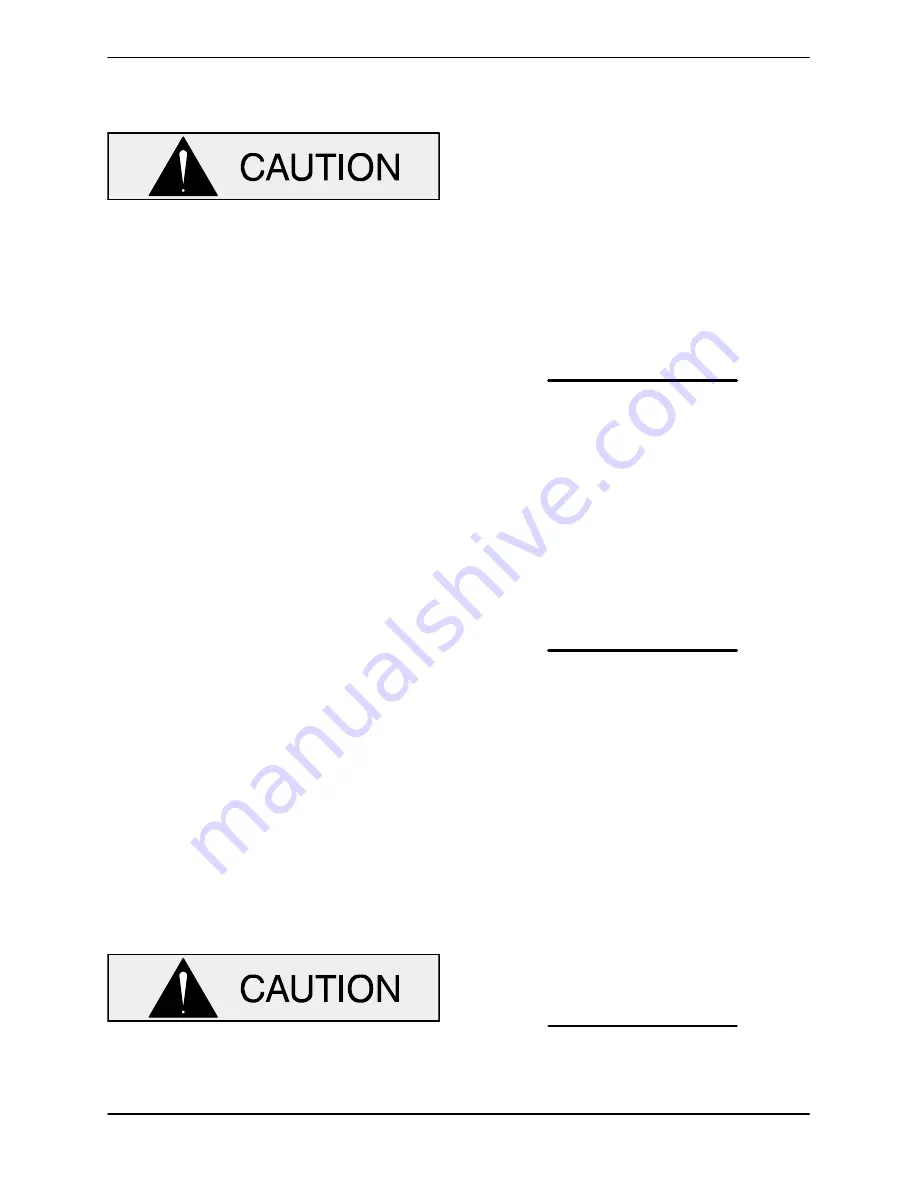
OM--01930--03
T SERIES
MAINTENANCE & REPAIR
PAGE E -- 13
Carefully
wash all metallic parts in fresh cleaning
solvent and allow to dry thoroughly.
Do not
attempt to separate the rotating
portion of the seal from the shaft sleeve
when reusing an old seal. The rubber bel-
lows will adhere to the sleeve during use,
and attempting to separate them could
damage the bellows.
Inspect the seal components for wear, scoring,
grooves, and other damage that might cause leak-
age. Inspect the integral shaft sleeve for nicks or
cuts on either end. If any components are worn, or
the sleeve is damaged, replace the complete seal;
never mix old and new seal parts
.
Install the stationary seal element in the stationary
seat. Press this stationary subassembly into the
seal plate bore until it seats squarely against the
bore shoulder. A push tube made from a piece of
plastic pipe would aid this installation. The I.D. of
the tube should be slightly larger than the O.D. of
the shaft sleeve.
Slide the rotating portion of the seal (consisting of
the integral shaft sleeve, spring centering washer,
spring, bellows and retainer, and rotating element)
onto the shaft until the seal faces contact.
Proceed with
Impeller Installation and Adjust-
ment
.
Impeller Installation and Adjustment
(Figure 2)
Inspect the impeller, and replace it if cracked or
badly worn. Inspect the impeller and shaft threads
for dirt or damage, and clean or dress the threads
as required.
The shaft and impeller threads
must
be
completely clean before reinstalling the im-
peller. Even the slightest amount of dirt on
the threads can cause the impeller to seize
to the shaft, making future removal difficult
or impossible without damage to the im-
peller or shaft.
Install the same thickness of impeller adjusting
shims (10) as previously removed. Apply ‘Never-
Seez’ or equivalent to the shaft threads and screw
the impeller onto the shaft until tight. Be sure the
spring centering washer seats squarely over the
shoulder on the back side of the impeller.
NOTE
At the slightest sign of binding, immediately back
the impeller off, and check the threads for dirt.
Do
not
try to force the impeller onto the shaft
.
A clearance of .025 to .040 inch (0,64 to 1,02 mm)
between the impeller and the seal plate is recom-
mended for maximum pump efficiency.
Pre-load
the shaft in the direction of the impeller
, and
measure this clearance; add or remove impeller
adjusting shims as required.
NOTE
If the rotating assembly has been installed in the
pump casing, this clearance may be measured by
reaching through the priming port with a feeler
gauge.
After the rotating assembly is installed in the pump
casing, coat the threads of the impeller capscrew
(28) with ‘Never-Seez’ or equivalent compound,
and install the impeller washer (28) and capscrew;
torque the capscrew to 90 ft. lbs. (1080 in. lbs. or
12,4 m. kg.).
Rotating Assembly Installation
(Figure 1)
NOTE
If the pump has been completely disassembled, it
is recommended that the suction check valve and
back cover assembly be reinstalled at this point.
The back cover assembly must be in place to adjust
the impeller face clearance.
Install the bearing housing and seal plate O-rings
(20 and 21), and lubricate them with light grease.
Ease the rotating assembly into the pump casing