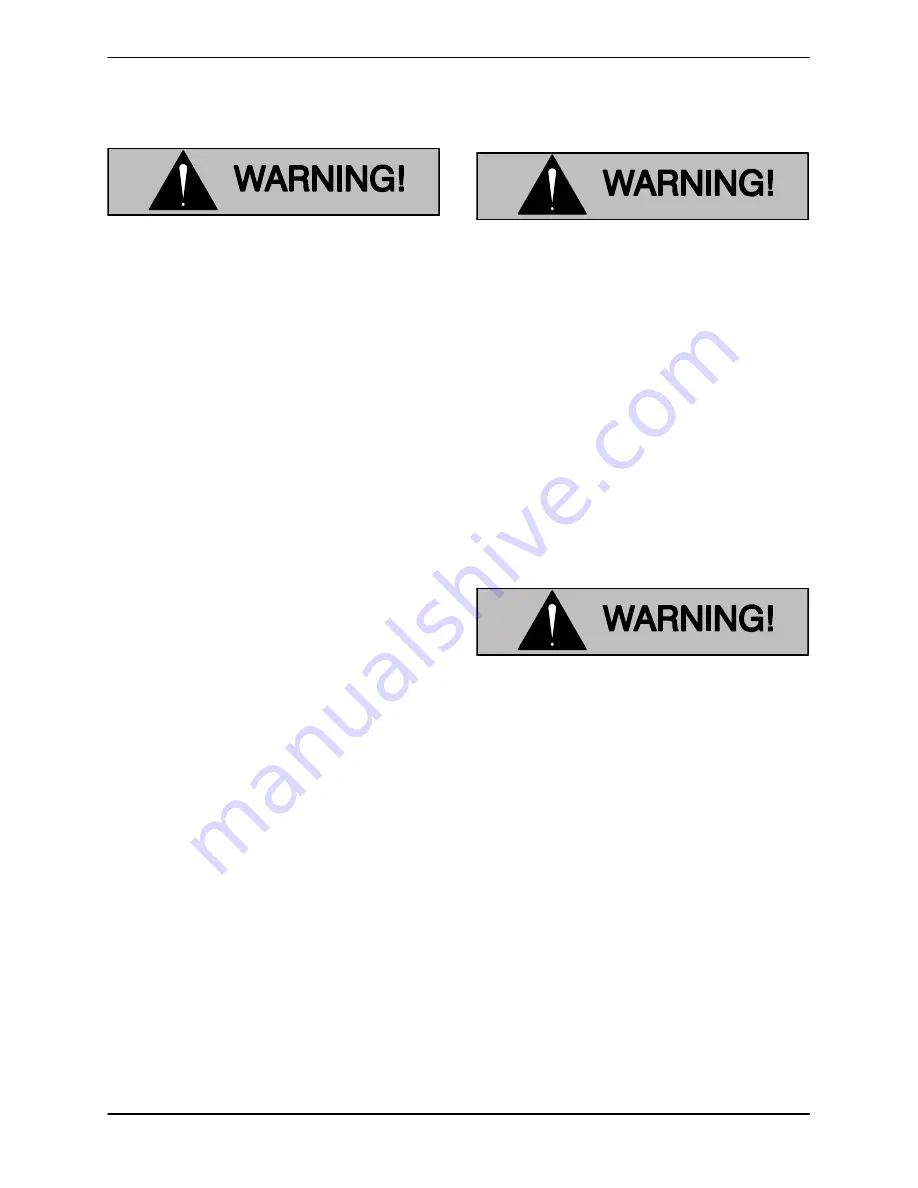
OM--01930--03
T SERIES
MAINTENANCE & REPAIR
PAGE E -- 6
PUMP AND SEAL DISASSEMBLY
AND REASSEMBLY
Most cleaning solvents are toxic and
flammable. Use them only in a well ven-
tilated area free from excessive heat,
sparks, and flame. Read and follow all
precautions printed on solvent contain-
ers.
Review all SAFETY information in Section A.
Follow the instructions on all tags, label and decals
attached to the pump.
This pump requires little service due to its rugged,
minimum-maintenance design. However, if it be-
comes necessary to inspect or replace the wearing
parts, follow these instructions which are keyed to
the sectional views (see Figures 1 and 2) and the
accompanying parts lists.
As described on the following page, this manual
will alert personnel to known procedures which re-
quire special attention, to those which could dam-
age equipment, and to those which could be dan-
gerous to personnel. However, this manual cannot
possibly anticipate and provide detailed precau-
tions for every situation that might occur during
maintenance of the unit. Therefore, it is the respon-
sibility of the owner/maintenance personnel to en-
sure that
only
safe, established maintenance pro-
cedures are used, and that any procedures not ad-
dressed in this manual are performed
only
after es-
tablishing that neither personal safety nor pump in-
tegrity are compromised by such practices.
Many service functions may be performed by
draining the pump and removing the back cover
assembly. If major repair is required, the piping
and/or power source must be disconnected. The
following instructions assume complete disassem-
bly is required.
Before attempting to service the pump, disconnect
or lock out the power source and take precautions
to ensure that it will remain inoperative. Close all
valves in the suction and discharge lines.
For power source disassembly and repair, consult
the literature supplied with the power source, or
contact your local power source representative.
Before attempting to open or service the
pump:
1. Familiarize yourself with this man-
ual.
2. Disconnect or lock out the power
source to ensure that the pump will
remain inoperative.
3. Allow the pump to cool if over-
heated.
4. Check the temperature before
opening any covers, plates, or
plugs.
5. Close the suction and discharge
valves.
6. Vent the pump slowly and cau-
tiously.
7. Drain the pump.
Use lifting and moving equipment in
good repair and with adequate capacity
to prevent injuries to personnel or dam-
age to equipment.
Back Cover And Wear Plate Removal
(Figure 1)
The wear plate (22) is easily accessible and may be
serviced by removing the back cover assembly
(23). Before attempting to service the pump, re-
move the pump casing drain plug (29) and drain
the pump. Clean and reinstall the drain plug.
Remove the hand nuts (35) and pull the back cover
and assembled wear plate from the pump casing
(1). Inspect the wear plate, and replace it if badly
scored and worn. To remove the wear plate, disen-
gage the hardware (37 and 38).
Inspect the back cover O-ring (30) and replace it if
damaged or worn.