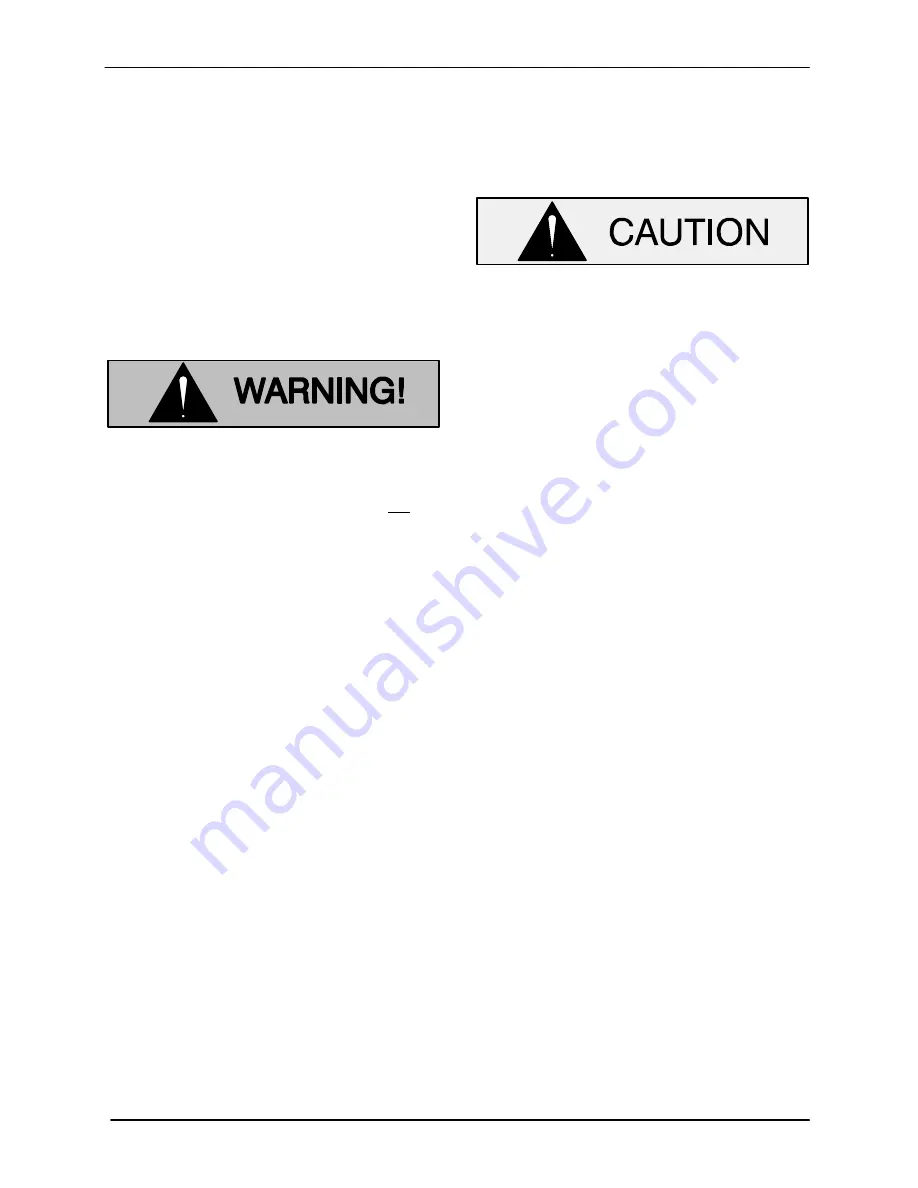
OM-06258
S SERIES PUMPS
PAGE E - 7
MAINTENANCE AND REPAIR
ture, such as worn pump parts, seal replacement,
lubrication, etc., refer to
PUMP END DISASSEM
BLY
for instructions.
If the problem is electrical, complete disassembly
may not be required. Refer to
Electrical Testing
in
TROUBLESHOOTING
, Section D, and have a
qualified electrician check the control box, cable
and terminal housing. If the problem is determined
to be in the motor, proceed with
PUMP END DIS
ASSEMBLY,
followed by
MOTOR DISASSEMBLY
.
Otherwise, see
Terminal Housing And Power Ca
ble Disassembly
.
The electrical power used to operate
this pump is high enough to cause inju
ry or death. Make certain that the control
handle
on the control box is in the off po
sition and locked out, or that the power
supply to the control box has been
otherwise cut off and locked out, before
attempting to open or service the pump
assembly. Tag electrical circuits to pre
vent accidental start‐up.
Carefully inspect any O‐rings or gaskets before re
moval and cleaning to determine if a proper seal
and compression existed prior to disassembly. If
sealing was faulty or questionable, the cause must
be determined and corrected before reassembly.
All gaskets and most O‐rings
must
be replaced if
disturbed. Repair gaskets and O‐rings are listed in
the Parts List.
PUMP END DISASSEMBLY
Strainer Removal
(Figure E-1)
To remove the strainer screen and base plate (48
and 53), raise the pump slightly, or lay it on its side
and disengage the hardware (50, 51 and 52) se
curing the strainer and base plate to the diffuser
(1). If the impeller (2) is clogged, the debris can
usually be removed without further disassembly.
Draining Oil From Seal Cavity
(
Figure E-1)
If any further disassembly is to be performed on the
pump, the seal oil cavity must be drained.
Let the pump cool before removing the
seal cavity drain plug. Pressure built up
within a hot pump could cause the oil to
spray out when the plug is removed. Re
move the plug slowly and permit pressure
to vent to atmosphere.
Lay the pump on its side with the pipe plugs (13
and 16) facing up. Clean any dirt from around the
plugs. Remove the seal cavity drain plug (13), and
install a short 3/8‐inch NPT nipple in the hole. Tip
the pump and drain the seal oil into a
clean
con
tainer. Inspect the oil for water, dirt, or cloudy condi
tion which could indicate lower seal failure or poor
gasket seal.
Draining Oil From Motor Cavity
(
Figure E-1)
If motor problems are suspected, remove the mo
tor cavity drain plug (16), and install a short nipple
in the hole. Tip the pump and drain the motor oil
into a
clean
container. Inspect the oil for dark color
which could indicate motor overheating, water or
dirt contamination. The presence of dirt or water
could indicate a breakdown in the waterproof in
tegrity of the motor cavity, probably due to poor
gaskets or seals.
Positioning Pump For Disassembly
(Figure E-1)
It is recommended that the pump be positioned
upside‐down during disassembly. To hold the
pump in the inverted position, rest the pump se
curely on blocks. Be careful not to damage the
pressure relief valve (29) and the terminal housing
and cable assembly (34) while in this position. Use
adequate equipment and personnel to safely han
dle the pump until it is secured. If inverting the
pump is not practical, lay the pump on its side and
secure it to prevent rolling.