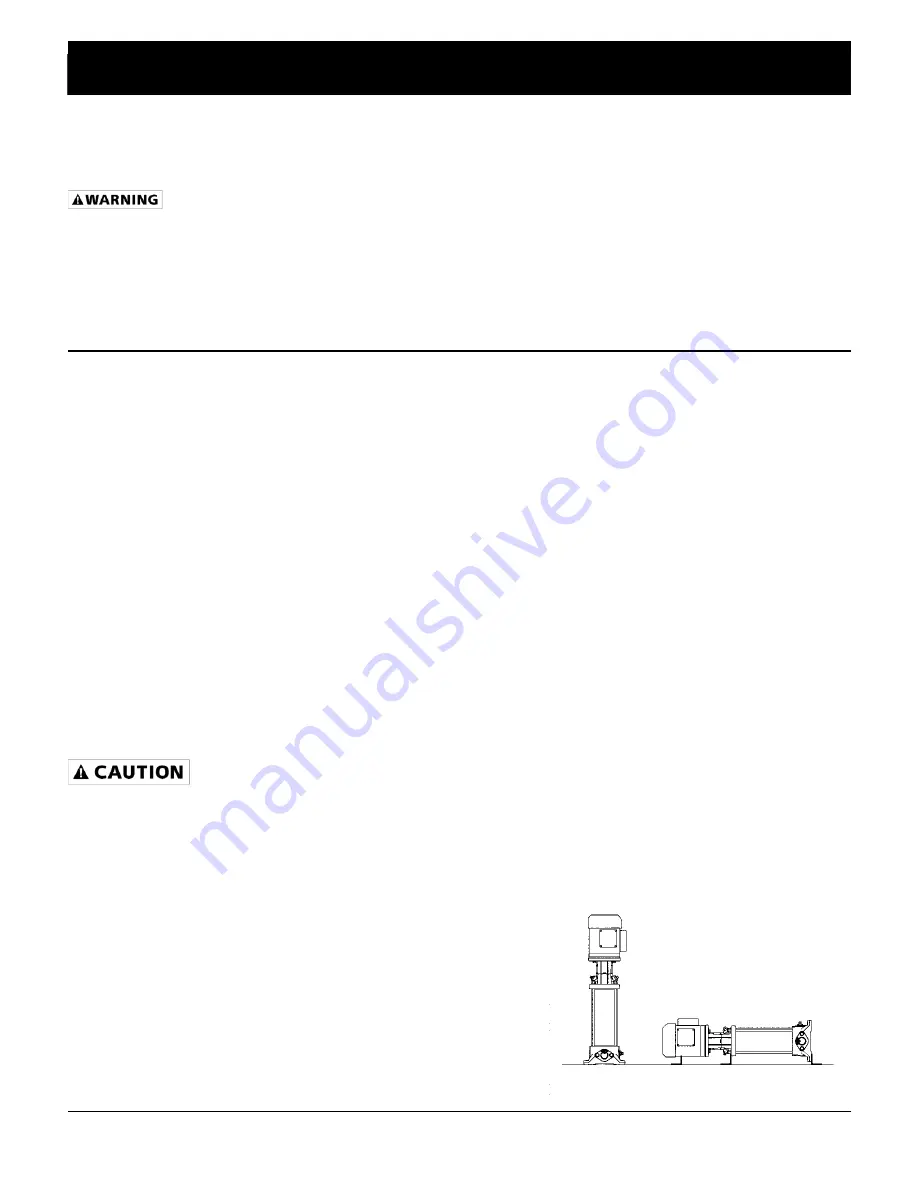
Installation
MOUNTING
Preferred mounting position is with
motor shaft aligned vertically (See
Figure 1).
1. Choose a solid, level surface with
adequate support such as a concrete
slab floor.
2. Use a level against pump to
check for plumb. For uneven
surfaces, shim beneath feet
of Casing (Ref. No. 38) to
attain proper alignment.
3. Securely fasten Casing to
mount surface at all four
mount holes to avoid tip-over
of pump. If space limitations dictate,
pump may also be mounted
horizontally if adequate support is
provided. Do NOT mount motor end
down or with shaft centerline below
horizontal plane.
PIPING
Pump may have a protective cover over
inlet and outlet for shipping purposes. If
present, be sure to remove these covers
prior to attaching piping. If flange
Screws (Ref. No. 41) are loosened, be
sure to re-tighten evenly and torque to
33 ft-lbs [45 N-m] to avoid Gasket (Ref.
No. 39) failure.
Starving the pump of liquid could cause
low performance and damage to pump
and seal. To avoid this, use suction
piping that is short and either matches
pump port diameter or is larger, do not
reduce. Also, immediately preceding
pump inlet, provide a section of straight
pipe equal in length to a minimum 4
diameters of pipe size and avoid using
valves.
5910-250-00
03/2012
Description
APPLICATIONS
These commercial/industrial centrifugal pumps are non-self-priming (gravity feed)
units designed to handle high-pressure/low-flow liquid transfer applications where no
suction lift is required. Typical installations include hot and chilled water, boiler feed,
condensate return, irrigation, high pressure wash-down, booster service, and
sprinkler systems. These pumps have NOT been investigated for use in potable
(drinking) water systems.
FEATURES
The in-line port design and compact footprint of these pumps allows for a clean
installation. All models feature a shaft seal that can be replaced easily without the
need to disassemble the entire pump. An optional ANSI/ASME flange kit is available.
Pumps are equipped with high efficiency closed impellers, and have a casing working
pressure to 536 ft./232 psi [1600 kPa]. Handle liquid temperatures from 40° F to
180° F [4° to 82° C]. For use with clear, nonabrasive, nonflammable liquids
compatible with pump component materials.
MOTOR
All models have 3450 RPM (2850 RPM for 50 Hz) continuous duty TEFC motors.
Single phase units are capacitor start and have automatic reset thermal protection. All
models are manual mode and require field wiring, no controls are supplied.
Motors have multi-voltage options. To avoid damage to motor,
be sure to arrange internal motor wiring to match electric supply voltage before
applying power (see motor nameplate for specific wiring diagram).
PUMP CONSTRUCTION
Pump construction is cast iron casing and adapter; 304 stainless steel impellers,
chambers and column; Teflon
®
wear rings; 304L stainless steel pump shaft with
tungsten carbide sleeve bearings; EPDM o-rings and gaskets; a mechanical shaft seal
of stainless steel, carbon graphite, and tungsten carbide wear faces.
Please read and save this Repair Parts Manual. Read this manual and the General Operating Instructions carefully before attempting to assemble,
install, operate or maintain the product described. Protect yourself and others by observing all safety information. The Safety Instructions are
contained in the General Operating Instructions. Failure to comply with the safety instructions accompanying this product could result in personal
injury and/or property damage! Retain instructions for future reference. AMT reserves the right to discontinue any model or change specifications
at any time without incurring any obligation.
®2009 American Machine & Tool Co., Inc. of PA, A Subsidiary of The Gorman-Rupp Company, All Rights Reserved.
Periodic maintenance and inspection are required on all pumps to insure proper operation. Units must be free of debris and
sediment. Inspect for leaks and loose bolts. Failure to do so voids warranty.
Multistage Centrifugal Pumps
Vertical Inline Models
Refer to form 1808-634-00 for General Operating and Safety Instructions
Specifications Information and Repair Parts Manual
PM1, PM3 and PM5 Series
Preferred Mounting Alternative Mounting
Figure 1 - Mounting