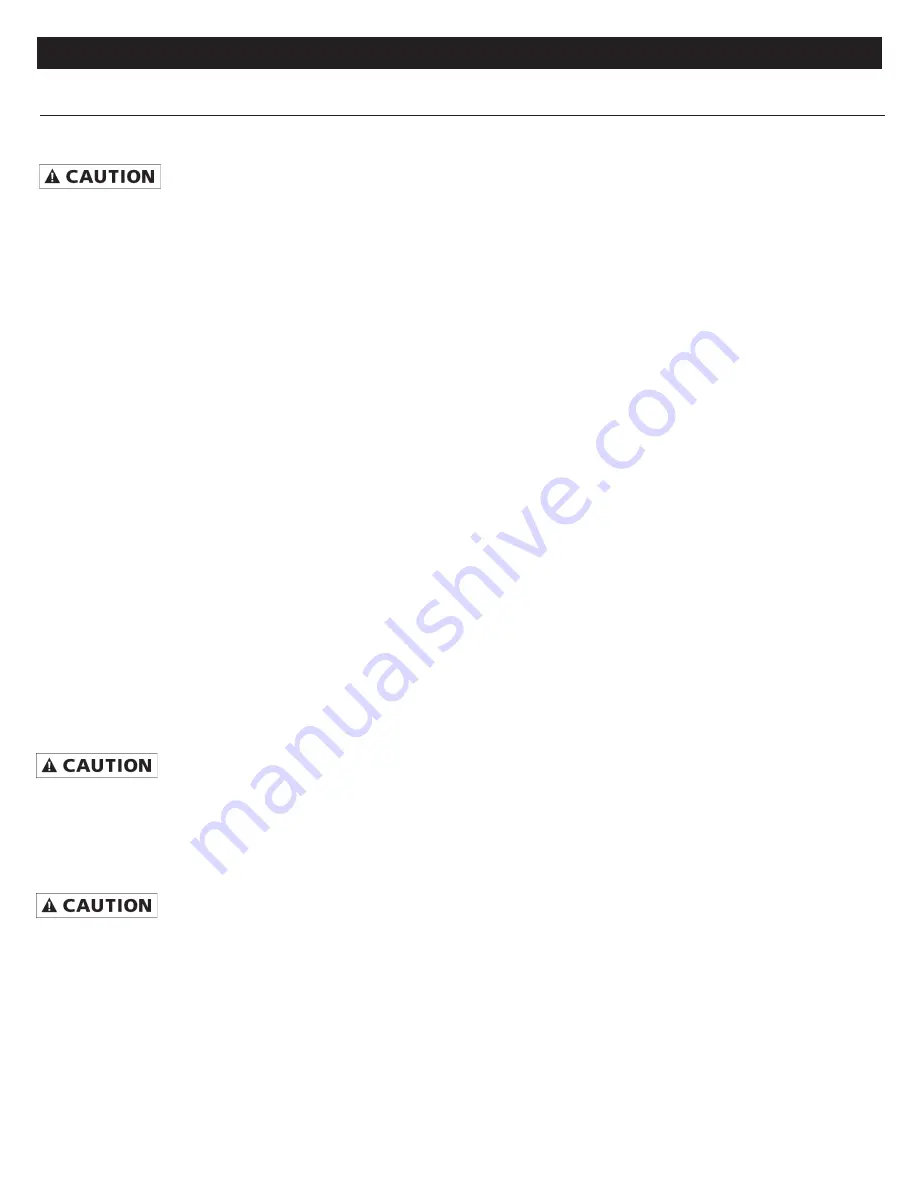
Specifications Information and Repair Parts Manual
573X Series
5730-250-00
3
1/2020
Patterson/AMT Inline Circulator Pumps
INSTALLATION OF NEW SEAL
The precision lapped faces of mechanical seal are easily damaged. To
prevent leaks, handle replacement seal carefully. Do not touch seal
mating faces.
IMPORTANT:
Be sure that shaft does not damage polished seal faces.
1. Thoroughly clean all surfaces of seal cavity in seal plate.
2. Using clean cloth, wipe shaft and make certain that it is perfectly clean.
3. Wet rubber portion of new seal with a light coating of soapy water. While
wearing clean gloves or using a clean rag, press seal seat squarely into
seal place seal cavity. Use cardboard washer (usually supplied with new
seal), place over polished seal surface and use a piece of pipe or dol rod
to press seat in firmly but gently. Avoid scratching polished face.
4. Dispose of cardboard washer. Check again to see that polished face is
free of dirt and all other foreign particles and that it has not been scratched
or damaged.
5. Install seal plate onto shaft and seat against adapter. Align 1/8” NPPT seal
wash port if port is being used.
6. Wet inside rubber portion of new seal head with a light coating of soapy
water. Slide head onto motor shaft with sealing surface facing seal seat.
NOTE:
A short “run-in” period may be necessary to provide completely leak-
free operation.
7. Screw impeller onto shaft. Hold stub shaft with hex key when tightening
impeller and impeller fastener.
8. Check if shaft turns freely by spinning impeller.
9. Slide impeller seal onto exposed shaft, screw impeller fastener onto shaft
with thread sealant applied (Vibra-Tite (12150) Threadlocker Medium
Strength Removable) and tighten.
10. Place casing seal on seal plate raised boss. Slide casing onto seal plate
and adapter.
11. Attach casing using fasteners with thread sealant applied (Vibra-Tite
(12150) Threadlocker Medium Strength Removable). Spin motor shaft to
check for interference with casing.
Seal will produce minor drag when spinning motor shaft, but rubbing
anywhere else must be eliminated! Otherwise, damage to pump and/or
motor may occur.
MOTOR REPLACEMENT
Entire pump end must be disassembled before removing motor from
adapter and stub shaft.
1. Remove pump casing, impeller, shaft seal, and seal plate as described in
SHAFT SEAL REPLACEMENT section.
2. Remove fasteners (Ref. No. 5) connecting adapter (Ref. No. 7) to motor
(Ref. No. 1).
3. Remove adapter from motor.
4. Loosen fasteners of shaft clamp (Ref. No. 2). Remove shaft clamp, stub
shaft (Ref. No. 4), and drive key (Ref. No. 3) from motor shaft.
5. Reverse procedure, reassemble pump on replacement motor.
6. Set distance from motor end bell mounting face to stub shaft shoulder (at
base of impeller threads) to 2.75”.
7. Securely tighten shaft clamp fasteners locking stub shaft in position.
PUMP PIPING
1.
Proper system design and installation by a qualified engineer is
recommended.
2. Always start piping from pump.
3. Use as few bends as possible and preferably long radius elbows.
4.
Do not use flexible connectors on the suction or discharge of a vertical in-
line pump unless the pump is rigidly mounted to a foundation.
5. Ensure piping exerts no strain on pump as this could distort the casing
causing breakage or early failure due to pump misalignment.
6.
All connecting pipe flanges must be square to the pipe work and parallel
to the pump flanges.
7. Eliminate all air pockets that may prevent the pump from operating
effectively.
8.
In open systems, test suction line for air leaks before starting; this
becomes essential with long suction line or static lift.
9. Install valves in both suction and discharge lines to assist with pump
inspection or repair. Suction line valve may be opened completely during
operation.
10. Install a non-slam non-return check valve in discharge line between pump
and isolation valve to protect pump from excessive back pressure and to
prevent water running back through the pump on open systems.
11.
Before starting pump, the system must be thoroughly cleaned, flushed
and drained and replenished with clean liquid.
12. Welding slag and other foreign materials, improper or excessive
water treatment are all detrimental to the pump internals and sealing
arrangement and void warranty.
13. Proper operation cannot be guaranteed if the above conditions are not
adhered to.
NOTE:
INSPECT THE FOLLOWING BEFORE PUTTING PUMP INTO
OPERATION:
1.
Pump primed; liquid in pump.
2. Rotation.
3. System piping and pump properly supported.
4. System clean of all debris.
5.
Proper electrical connections. Consult qualified electrician with any
questions.
6. Proper motor support is required to avoid damage to motor or pump
see page 1, Installation & orienting sections
IMPORTANT: SYSTEM MUST BE FREE OF ALL PETROLEUM BASED
LIQUID OR SUBSTANCE TO AVOID SEAL FAILURE, WHICH CAN ALSO
LEAD TO PREMATURE MOTOR BEARING FAILURE. FAILURE TO
COMPLY VOIDS WARRANTY.
Содержание Patterson/AMT 573 Series
Страница 6: ...Specifications Information and Repair Parts Manual 573X Series 5730 250 00 6 1 2020 NOTES...
Страница 7: ...Specifications Information and Repair Parts Manual 573X Series 5730 250 00 7 1 2020...
Страница 8: ...Specifications Information and Repair Parts Manual 573X Series 5730 250 00 8 1 2020 www amtpump com...