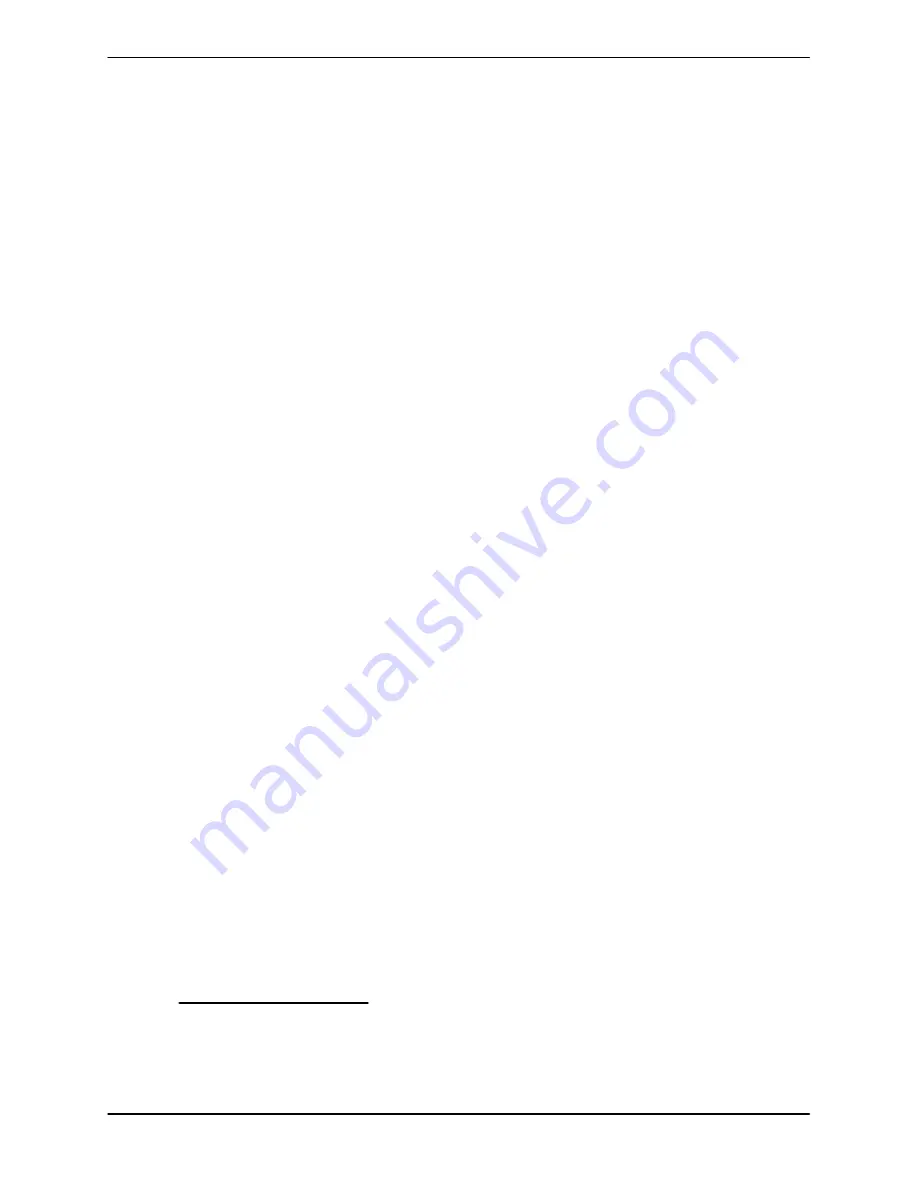
OM-06789
10 SERIES
MAINTENANCE & REPAIR
PAGE E - 9
Pump Casing Installation
(Figure 2)
Install the same thickness of pump casing gaskets
(14) as previously removed and secure the pump
casing (1) to the intermediate (9) with the nuts (7).
Do not
fully tighten the nuts at this time.
A clearance of .010 to .020 inch (0,25 to 0,51 mm)
between the impeller and the wear plate is also rec
ommended for maximum pump efficiency. This
clearance must be set after installing the back cov
er by adding or removing pump casing gaskets un
til the impeller scrapes against the wear plate when
the shaft is turned. After the impeller scrapes, add
approximately .010 inch (0,25 mm) of gaskets.
After the face clearance has been set, tighten the
nuts (7) securing the pump casing to the intermedi
ate.
See Figure 1 and secure the pump casing to the
base (9) with the hardware (11, 12, 14 and 15). Be
sure to reinstall any leveling shims used under the
mounting feet of the pump casing.
Back Cover Installation
(Figure 2)
Inspect the wear plate (15) and replace it if badly
worn or grooved. Carefully center the wear plate on
the back cover (25) and secure it with the hardware
(21 and 22). The wear plate must be concentric to
prevent binding when the back cover is installed.
Clean any scale or debris from the back cover
shoulder and pump casing which might prevent a
good seal.
NOTE
Apply a film of `Never‐Seez' or equivalent com
pound on the back cover shoulder or any surface
which contacts the pump casing to ease future dis
assembly and to reduce rust and scale build up.
Replace the back cover gasket (20) and slide the
back cover assembly into the pump casing. Be
sure the wear plate does not bind against the
pump casing.
Secure the back cover assembly using the hard
ware (23 and 24).
Do not
over tighten the wing
nuts; they should be just tight enough to ensure a
good seal at the back cover shoulder.
Suction Check Valve Installation
(Figure 2)
Inspect the check valve components and replace
as required. Assemble the check valve weights to
each side of the check valve and secure with the
peviously removed hardware.
Position the check valve assembly (27) in the suc
tion port with the large weight toward the impeller
and the small weight toward the suction flange. In
stall the suction flange (26) and secure it with the
nuts (7). Check the operation of the check valve to
ensure proper seating and free movement.
Final Pump Assembly
(Figure 1)
Be sure
the pump and engine are securely
mounted to the base.
Install the suction and discharge lines and open all
valves. Make certain that all piping connections are
tight, properly supported and secure.
Be sure
the pump and engine have been properly
lubricated, see
LUBRICATION
.
Remove the fill plug (2) and fill the pump casing
with clean liquid. Reinstall the fill plug and tighten.
Refer to
OPERATION
, Section C, before putting
the pump back into service.
LUBRICATION
Seal Assembly
The seal assembly is lubricated by the medium be
ing pumped, and no additional lubrication is re
quired.
Engine
Consult the literature supplied with the engine, or
contact your local engine representative.