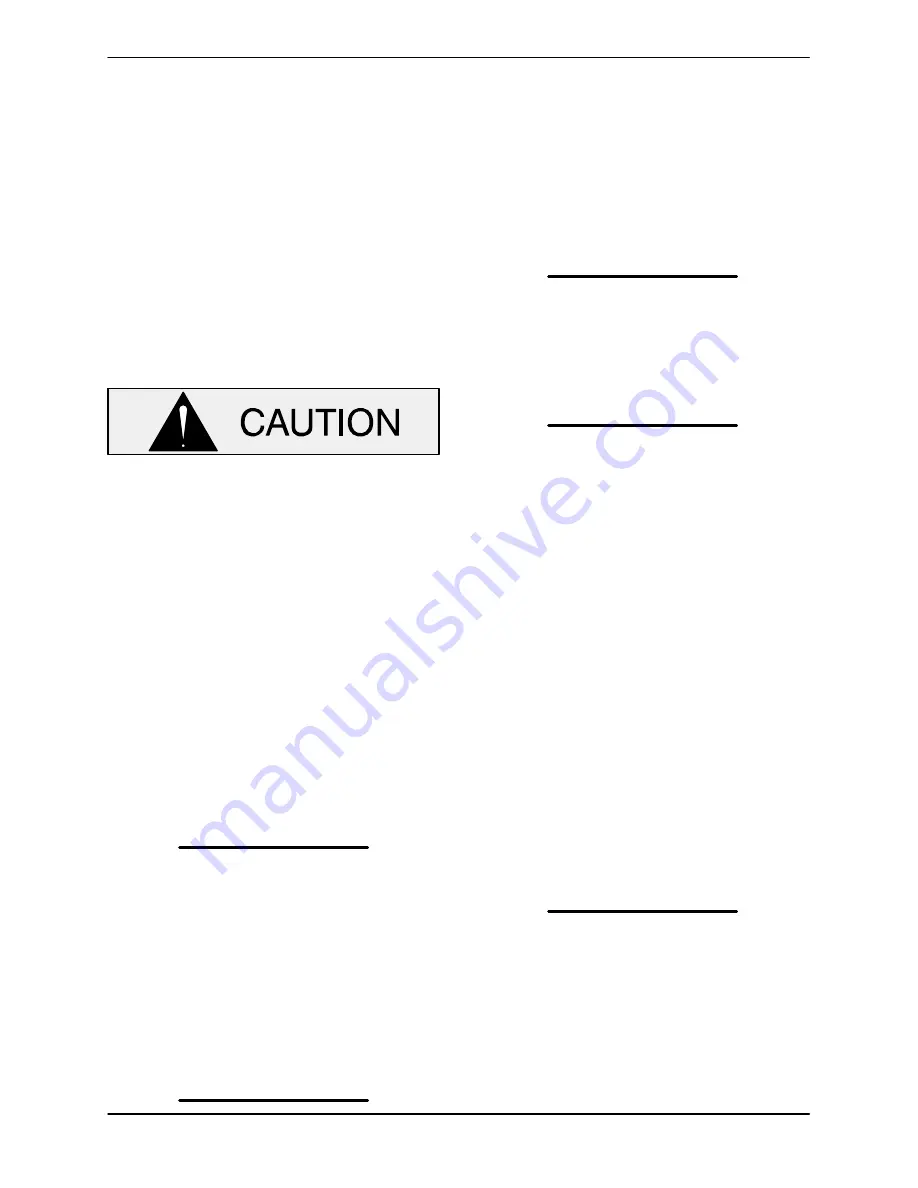
OM-06845
SUPER T SERIES
MAINTENANCE & REPAIR
PAGE E - 19
Slide the rotating portion of the seal (consisting of
the integral shaft sleeve, spring centering washer,
spring, bellows and retainer, and rotating element)
onto the shaft until the seal faces contact.
Proceed with
Impeller Installation and Adjust
ment.
Impeller Installation
(Figure 4)
Inspect the impeller, and replace it if cracked or
badly worn. Inspect the impeller and shaft threads
for dirt or damage, and clean or dress the threads
as required.
The shaft and impeller threads
must
be
completely clean before reinstalling the im
peller. Even the slightest amount of dirt on
the threads can cause the impeller to seize
to the shaft, making future removal difficult
or impossible without damage to the im
peller or shaft.
Install the same thickness of impeller adjusting
shims (26) as previously removed. Apply `Never‐
Seez' or equivalent to the shaft threads and screw
the impeller onto the shaft until tight. Be sure the
seal spring seats squarely on the back side of the
impeller.
NOTE
At the slightest sign of binding, immediately back
the impeller off, and check the threads for dirt.
Do
not
try to force the impeller onto the shaft
.
A clearance of .025 to .040 inch (0,64 to 1,02 mm)
between the impeller and the seal plate is recom
mended for maximum pump efficiency. Measure
this clearance, and add or remove impeller adjust
ing shims as required.
NOTE
If the rotating assembly has been installed in the
pump casing, this clearance may be measured by
reaching through the priming port with a feeler
gauge.
Rotating Assembly Installation
(Figure 3)
NOTE
If the pump has been completely disassembled, it
is recommended that the suction check valve and
back cover assembly be reinstalled at this point.
The back cover assembly must be in place to adjust
the impeller face clearance.
NOTE
There is a 1‐1/2 inch diameter socket head pipe
plug located in the side of the bearing housing. This
hole is required for manufacturing purposes only;
therefore the pipe plug should never require re
moval.
Install the bearing housing O‐ring (18) and lubri
cate it with light grease. Ease the rotating assem
bly into the pump casing using the installation tool.
Be careful
not to damage the O‐ring.
Install the rotating assembly adjusting shims (13)
using the same thickness as previously removed.
Secure the rotating assembly to the pump casing
with the hardware (11 and 12).
To set the impeller and wear plate clearance refer
to the
Back Cover Installation And Adjustment
.
Suction Check Valve Installation
(Figure 3)
Inspect the check valve assembly (30) and replace
it if badly worn.
NOTE
The check valve assembly must be replaced as a
complete unit. Individual parts are not sold sepa
rately.
Reach through the back cover opening with the
check valve and position the check valve adaptor
in the mounting slot in the suction flange (31). Align
the adaptor with the flange hole and secure the as
sembly with the check valve pin (32).
NOTE
If the suction or discharge flanges were removed,
replace the respective gaskets, apply `Permatex