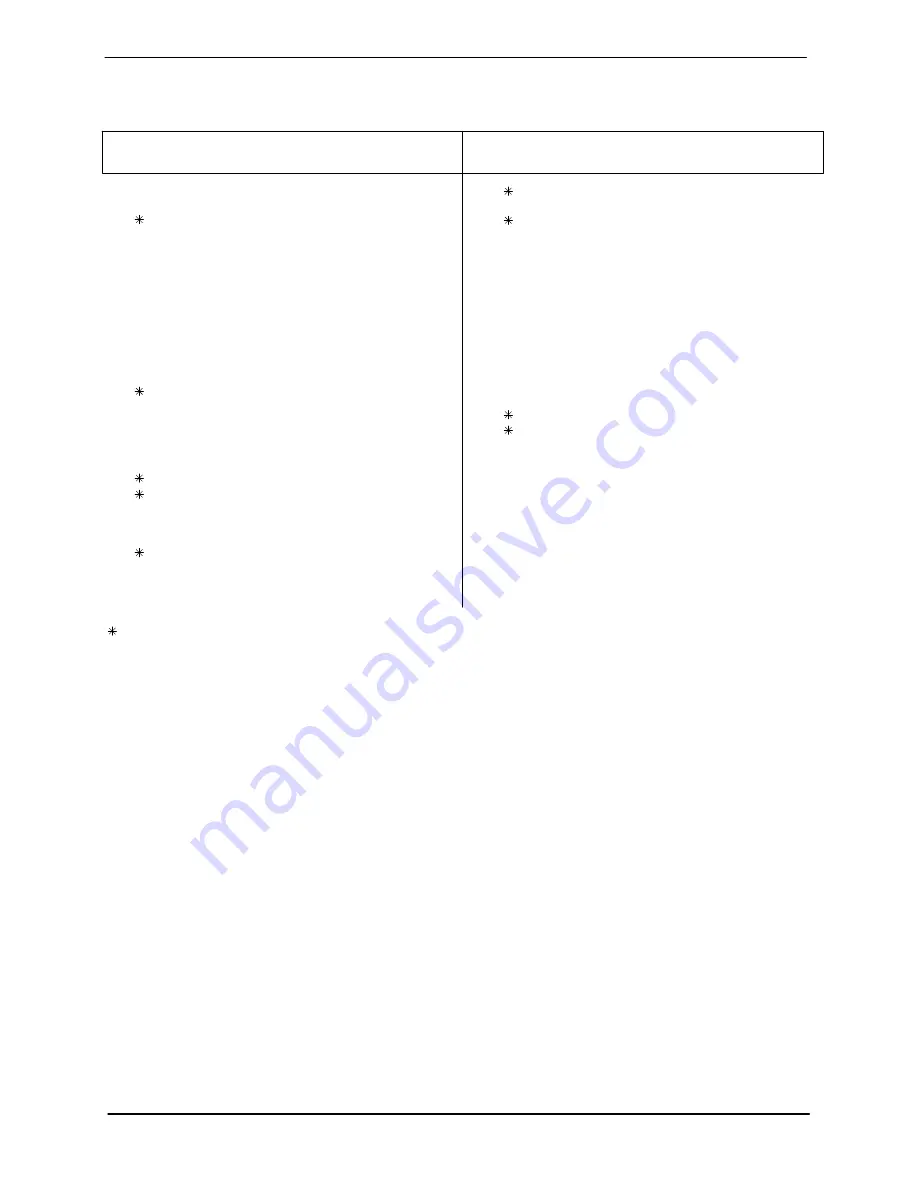
ITEM
NO.
PART NAME
PART
NUMBER
QTY
ITEM
NO.
PART NAME
PART
NUMBER
QTY
SUPER T SERIES
OM-07080
MAINTENANCE & REPAIR
PAGE E - 7
PARTS LIST
Pump End Assembly
.
1
REPAIR PUMP CASING
SEE NOTE BELOW
1
.
2
PIPE PLUG
P04 15079
3
3
GASKET
25113-034 1
4
4" NPT FLANGE
1756 10010
1
5
CLOSE PIPE NIPPLE
T64 15070
1
6
PIPE ELBOW
R64 11990
1
7
LOCK WASHER
J10 15991
16
8
HEX HEAD CAP SCREW
B1007 15991
8
9
SCREW-CLAMP BAR
31912-009 15000
1
.
10
MACHINE BOLT
A1014 15991
2
11
CLAMP BAR
38111-004 11010
1
12
FILL COVER PLATE ASSY 42111-344 1
-WARNING PLATE
38816-097 13990
1
-DRIVE SCREW
BM#04-03 17000
2
-FILL COVER GASKET
50G 19210
1
13
ADJ SHIM
13130-3 17040
8
14
LOCK WASHER
J08 15991
8
15
HEX HEAD CAP SCREW
B0806 15991
4
16
DRIVE ASSY
44162-160
1
17
REPAIR ROTATING ASSY
44163-347
1
18
O‐RING
S1674 2
19
O‐RING
25152-273 2
20
DRIVE SCREW
BM#04-03 17000
4
21
NAMEPLATE BLANK
38819-002 13000
1
.
22
PIPE PLUG
P20 10009
1
23
WEAR PLATE ASSY
10532A 15990
1
24
LOCK WASHER
J06 17090
2
25
HEX NUT
D06 17090
2
26
BACK COVER ASSY
42111-834 1
27
O‐RING
S1472 1
28
INSPECTION COVER ASSY42111-451 1
-PRESSURE RELIEF VLV 26662-005
1
-DRIVE SCREW
BM#04-03 17000
4
-WARNING PLATE
2613EV 13990
1
29
HANDLE
12354 13010
1
30
LOCK WASHER
J06 15991
2
31
HEX HEAD CAP SCREW
B0604 15991
2
32
BACK COVER NUT
31871-075 15000
2
33
HEX HEAD CAP SCREW
B0804-1/2 15991
4
34
BACK COVER NUT
31871-073 15000
4
35
ADJUSTING SCREW
31871-070 1500G
4
36
LOCK COLLAR
38115-551 15001
4
37
HEX HEAD CAP SCREW
B1008 15991
8
38
SUCTION FLANGE
11389 10010
1
39
CHECK VALVE PIN
11557 17010
1
40
SUCT FLANGE GASKET
11389G 19370
1
41
4'' FLAP VALVE ASSY
46411-062
1
.
42
STUD
C1213 15991
4
.
43
PIPE PLUG
P08 15079
1
NOT SHOWN:
G-R DECAL
GR-03
1
LUBRICATION DECAL
38817-084 1
WARNING DECAL
2613FE
1
SUPER "T" DECAL
38812-089 1
4" STRAINER ASSEMBLY
2690C 24000
1
DISCHARGE STICKER
6588BJ
1
SUCTION STICKER
6588AG
1
FILL TO PRIME STICKER
6588AH
1
INSTRUCTION TAG
38817-085 1
INDICATES PARTS RECOMMENDED FOR STOCK
.
INCLUDED WITH REPAIR
46472-721
1
PUMP CASING ASSY