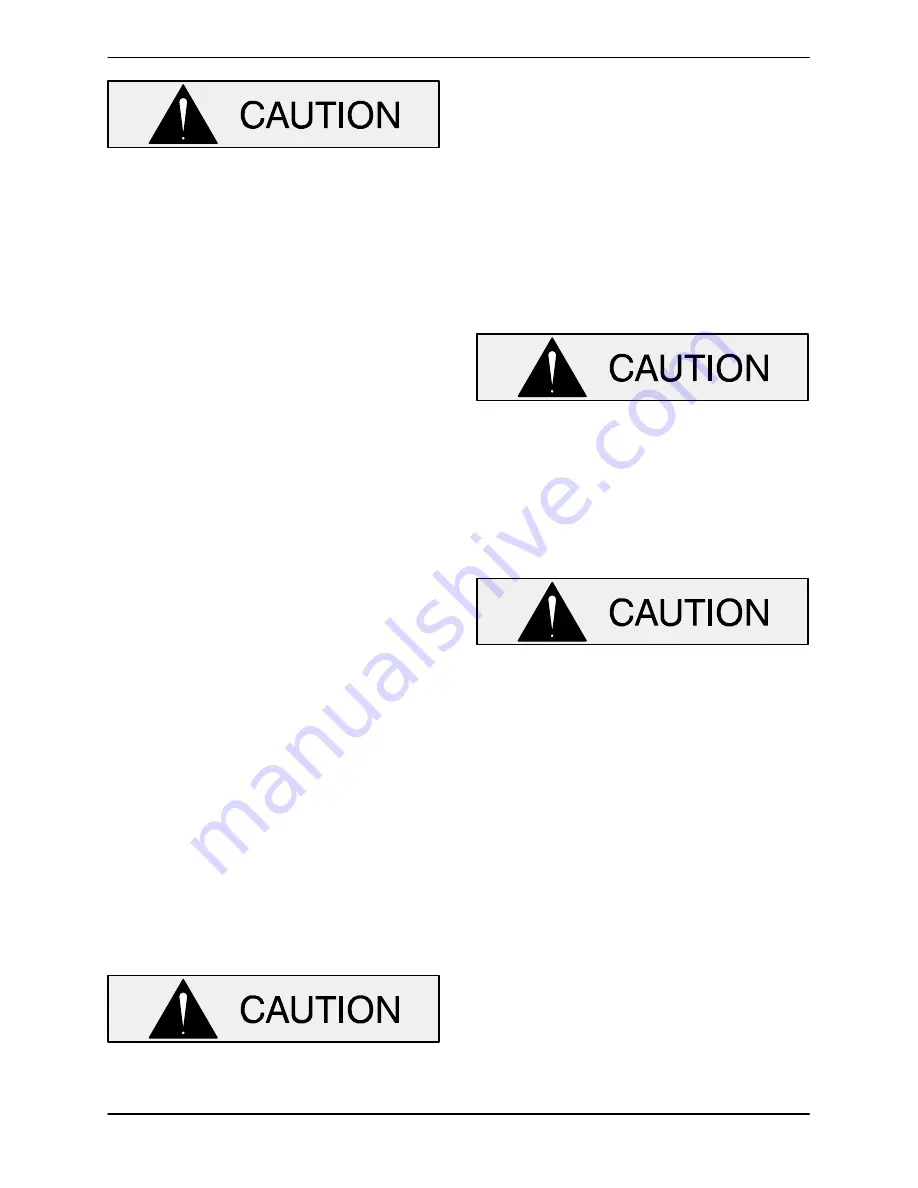
OM-06575
PA SERIES
MAINTENANCE & REPAIR
PAGE E - 17
The standard seal is not designed for oper
ation at temperatures above 160
F (71
C).
Do not use at higher operating tempera
tures.
Lubricate the outboard stationary seat O‐ring with
water or light oil. Position the seal plate with the im
peller side up and press the stationary subas
sembly (consisting of the stationary seat, O‐rings
and stationary element) into the front of the seal
plate until it seats squarely against the bore shoul
der.
Slide the seal plate and stationary portion of the
seal over the shaft until it is seated against the ped
estal (20).
Be careful
not to damage the stationary
element or roll or cut the lip of the oil seal (23) on the
shaft keyway. Secure the seal plate to the pedestal
with the previously removed hardware (16 and 17).
Lubricate the seal sleeve O‐ring with a
small
amount of light oil and install it in the groove in the
I.D. of the sleeve.
Lubricate the seal sleeve with a
small
amount of
light oil and slide the rotating subassembly (con
sisting of rotating element, bellows and retainer),
onto the sleeve until the rotating element is
just
flush
with the
turned
end of the sleeve.
Slide the sleeve and subassembled seal onto the
shaft until the seal faces contact and the sleeve
seats against the shaft shoulder.
Install the seal spring. Lubricate the seal as indi
cated in
LUBRICATION
after the impeller, remain
ing pump components, bottle oiler and piping are
installed.
Impeller Installation
(Figure 2)
Proper wear ring replacement requires
machining and dynamic balancing the im
peller assembly after the wear ring is
welded to the impeller. Failure to properly
install the wear ring and machine and bal
ance the impeller assembly can result in
premature shaft, seal or bearing failure, or
other damage to the pump.
Inspect the impeller, and replace it if cracked or
badly worn. If the impeller wear ring was removed,
chill the impeller by refrigeration and use an induc
tion heater or oven to heat the new wear ring. Slide
the wear ring onto the impeller until fully seated
against the shoulder and allow it to cool.
The wear ring
must
seat squarely on the
impeller; otherwise binding and/or exces
sive wear will occur. Use caution when han
dling hot parts to prevent burns.
Spot weld the wear ring to the impeller at three
places, equally spaced at the vanes. After welding,
machine the wear ring as shown in Figure 5.
The impeller assembly must be machined
and balanced as shown in Figure 5. Other
wise, premature shaft, seal or bearing fail
ure, or other damage to the pump may oc
cur.
After machining, dynamically balance the impeller
assembly per plane 1.05 oz./in. (11.7 g/cm).
Install the same thickness of impeller adjusting
shims (42) as previously removed. Install the shaft
key (33, Figure 3) and press the impeller assembly
onto the shaft until fully seated.
A clearance of approximately .015 inch (0,38 mm)
between the impeller and the seal plate is recom
mended for maximum pump efficiency. Measure
this clearance, and add or remove impeller adjust
ing shims as required.
After the impeller clearance has been set, align the
pin (9) in the impeller washer (8) with the hole in the
impeller and install the washer. Apply “Never‐
Seez” or equivalent compound on the threads of