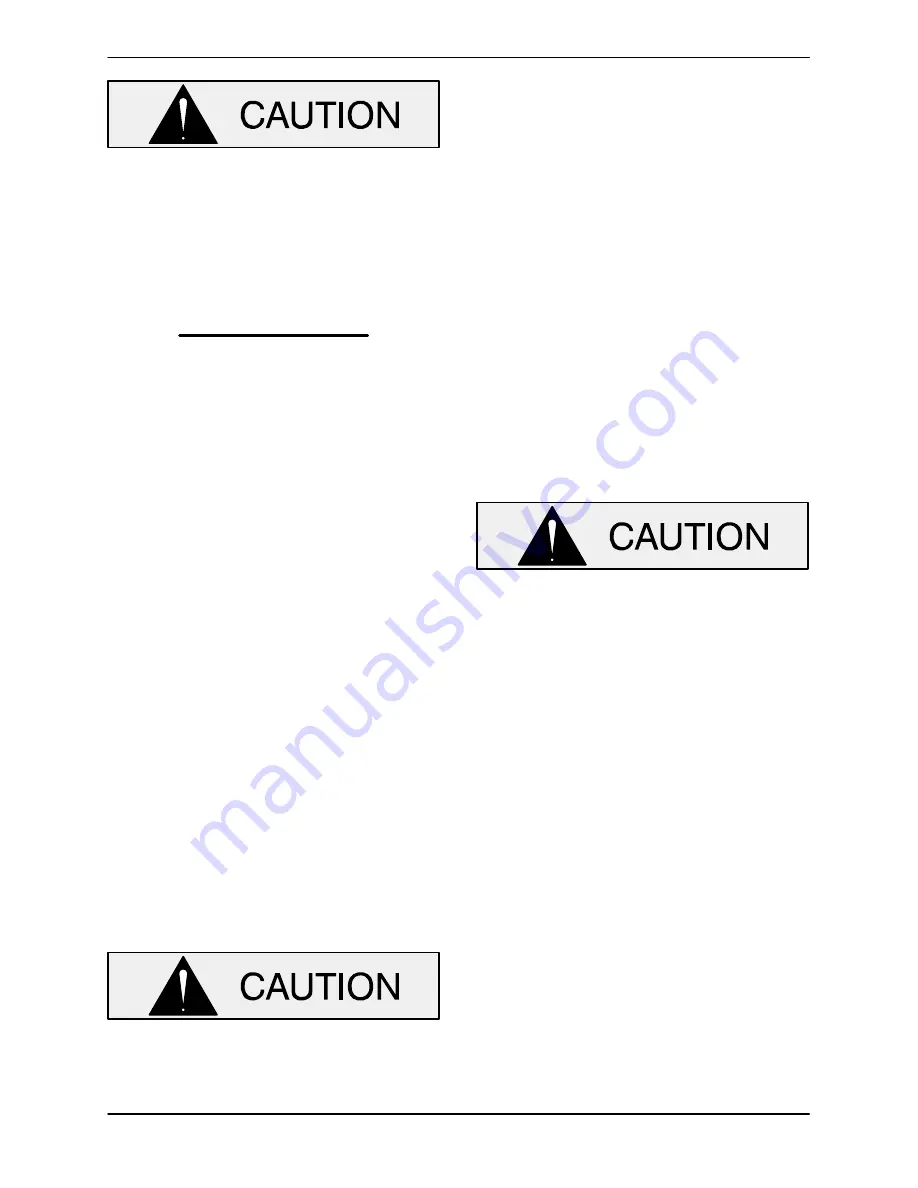
PA SERIES
OM-06575
MAINTENANCE & REPAIR
PAGE E - 14
Use caution when handling hot bearings to
prevent burns.
NOTE
If a hot oil bath is used to heat the bearings, both the
oil and the container must be
absolutely
clean. If
the oil has been previously used, it must be
thor
oughly
filtered.
Heat the bearings to a uniform temperature
no
higher than
250
F (120
C). Position the roller
bearing (34) on the shaft with the internal snap ring
positioned away from the impeller end of the shaft.
Slide the roller bearing onto the shaft until fully
seated against the shaft shoulder. This should be
done quickly, in one continuous motion, to prevent
the bearings from cooling and sticking on the shaft.
After the bearing has been installed and allowed to
cool, check to ensure that it has not moved away
from the shaft shoulder in shrinking. If movement
has occurred, use a suitably sized sleeve and a
press to reposition the bearing against the shaft
shoulder.
Secure the roller bearing on the shaft with the bear
ing retaining ring (55).
Slide the heated outboard bearings (30) onto the
shaft, one at a time, with the larger inner races of
each bearing positioned away from each other as
shown in Detail E, Figure 3.
If heating the bearings is not practical, use a suit
ably sized sleeve and an arbor (or hydraulic) press
to install the bearings on the shaft.
When installing the bearings onto the
shaft,
never
press or hit against the outer
race, balls, or ball cage. Press
only
on the
inner race.
After the bearings have been installed and allowed
to cool, check to ensure that they have not moved
away from the shaft shoulders in shrinking. If
movement has occurred, use a suitably sized
sleeve and a press to reposition the bearings
against the shaft shoulder.
Secure the assembled shaft and bearings by
clamping on the surface between the bearings.
Use caution not to scratch or mar the part number
etched into the shaft in this area. Install the tab
washer (28) and bearing lock nut (27). Torque the
lock nut to 150 ft. lbs. (1800 in. lbs. or 20,7 m. kg.).
Locate the tab on the lock washer that aligns with a
slot in the lock nut, and bend the tab over into the
slot.
Slide the shaft and assembled bearings into the
pedestal from the drive end until the outer race on
the inboard ball bearing (30) seats against the ped
estal bore.
When installing the shaft and bearings into
the bearing bore, push against the outer
race.
Never
hit the balls or ball cage.
Press the oil seal (23) into the bearing cap (24) with
the lip positioned as shown in Figure 3. Lubricate
and install a new bearing cap O‐ring (25) and se
cure the bearing cap with the capscrews (22). Use
caution not to cut or roll the lip of the oil seal when
installing the bearing cap.
Press the oil seal (23) into the bearing cap (35) with
the lip positioned as shown in Figure 3. Replace
the bearing cap gasket (29) and secure the bear
ing cap with the capscrews (22). Use caution not to
cut or roll the lip of the oil seal when installing the
bearing cap.
Lubricate the pedestal as indicated in
LUBRICA
TION
.
Seal Reassembly and Installation
(Figures 2 and 6)
Clean the bore of the seal plate (40), the seal plate
cover (45) and the shaft (32) with a cloth soaked in
fresh cleaning solvent.