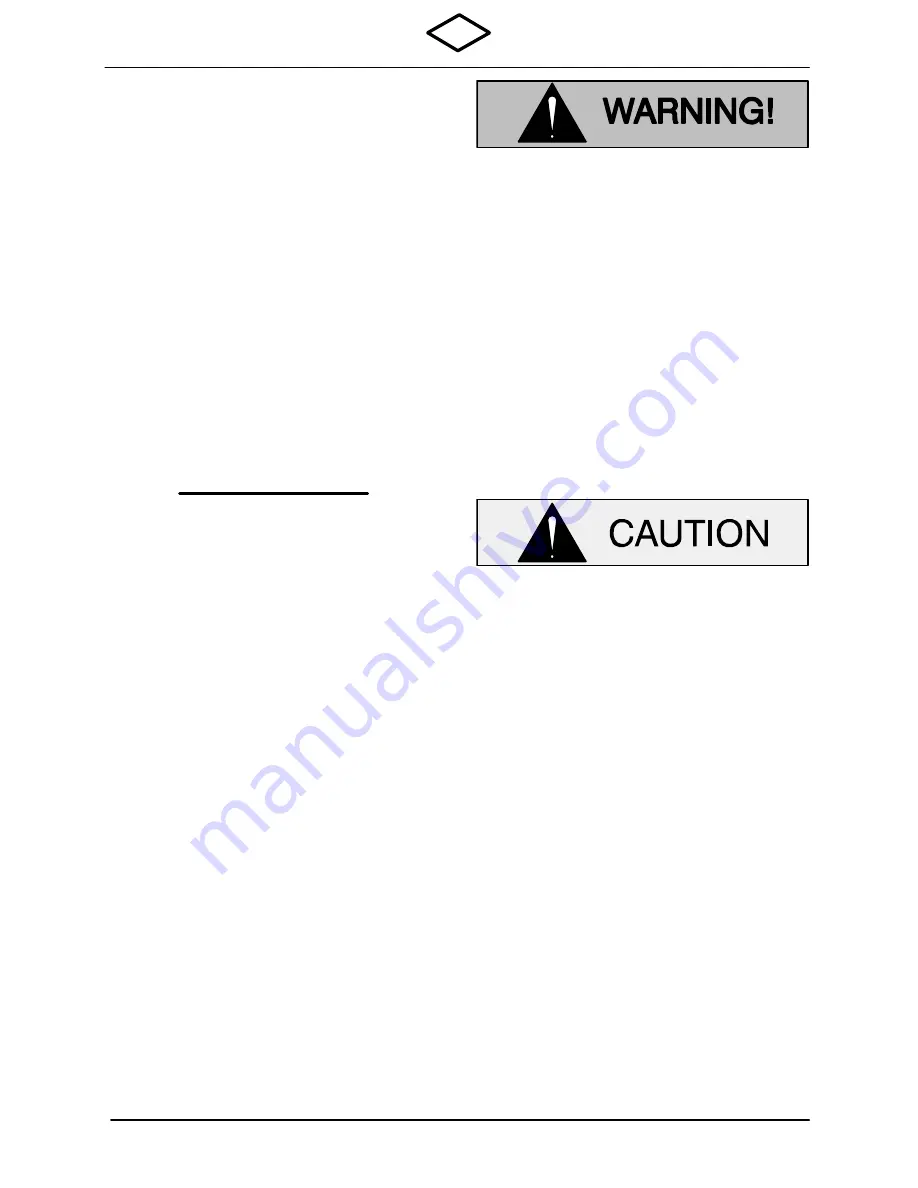
MR−03955
JS SERIES PUMPS
FM
APPROVED
PAGE C − 7
MAINTENANCE AND REPAIR
If no further disassembly is required, refer to
IN-
SPECTION AND CLEANING
, followed by
PUMP
END REASSEMBLY
.
Upper Seal Removal
References are to FIGURES C−2 and C−3.
1. Remove the screws (254) securing the seal
housing housing (257) to the stator housing.
Use a soft-faced mallet to tap around the seal
housing until it comes free of the lower bearing
housing (213). Slide the seal housing off the
shaft.
NOTE
Use caution in Step 2, tension on the seal clamp
springs will be released.
2. Loosen the drive screw, and remove the retain-
er and springs.
3. Lightly oil the shaft, and remove the seal rotat-
ing element and O-ring.
4. Work a pair of stiff wires with hooked ends be-
tween the stationary seal seat and the bearing
housing (213), and pull the stationary seat and
O-ring out of the bearing housing.
If no further disassembly is required, refer to
IN-
SPECTION AND CLEANING
, followed by
PUMP
END REASSEMBLY
.
INSPECTION AND CLEANING
Carefully inspect all O-ring seating areas to deter-
mine if they formed a proper seal. If sealing was
faulty, determine the cause before reassembling
the pump. After inspection, remove and discard all
O-rings.
Most cleaning solvents are toxic and
flammable. Use them only in a well-ven-
tilated area free from flame, sparks, and
excessive heat. Read and follow all pre-
cautions printed on solvent containers.
Reusable Parts (Except Seal Assemblies)
1. Thoroughly clean all reusable parts.
2. Inspect all mating surfaces for nicks or burrs,
and restore to original contours with emery
cloth or a fine file. If the surface cannot be re-
stored, replace the part.
Cleaning Seal Assemblies
Seal faces are precision-finished and sub-
ject to wear patterns which cannot be re-
aligned during assembly. The seal assem-
bly should be replaced completely at each
overhaul to ensure trouble-free operation.
If necessary to use an old seal in an emer-
gency,
never
mix old and new seal parts;
seal performance will be severely affected.
1. Inspect the seal assembly for wear, scoring,
grooves, and other damage that might cause
leakage.
2. Wash all seal parts in fresh cleaning solvent and
allow to dry thoroughly. Re-inspect the parts af-
ter cleaning.
3. If needed, clean the seal faces with a clean, lint-
free cloth. Wipe lightly in a concentric pattern to
avoid scratching the faces.