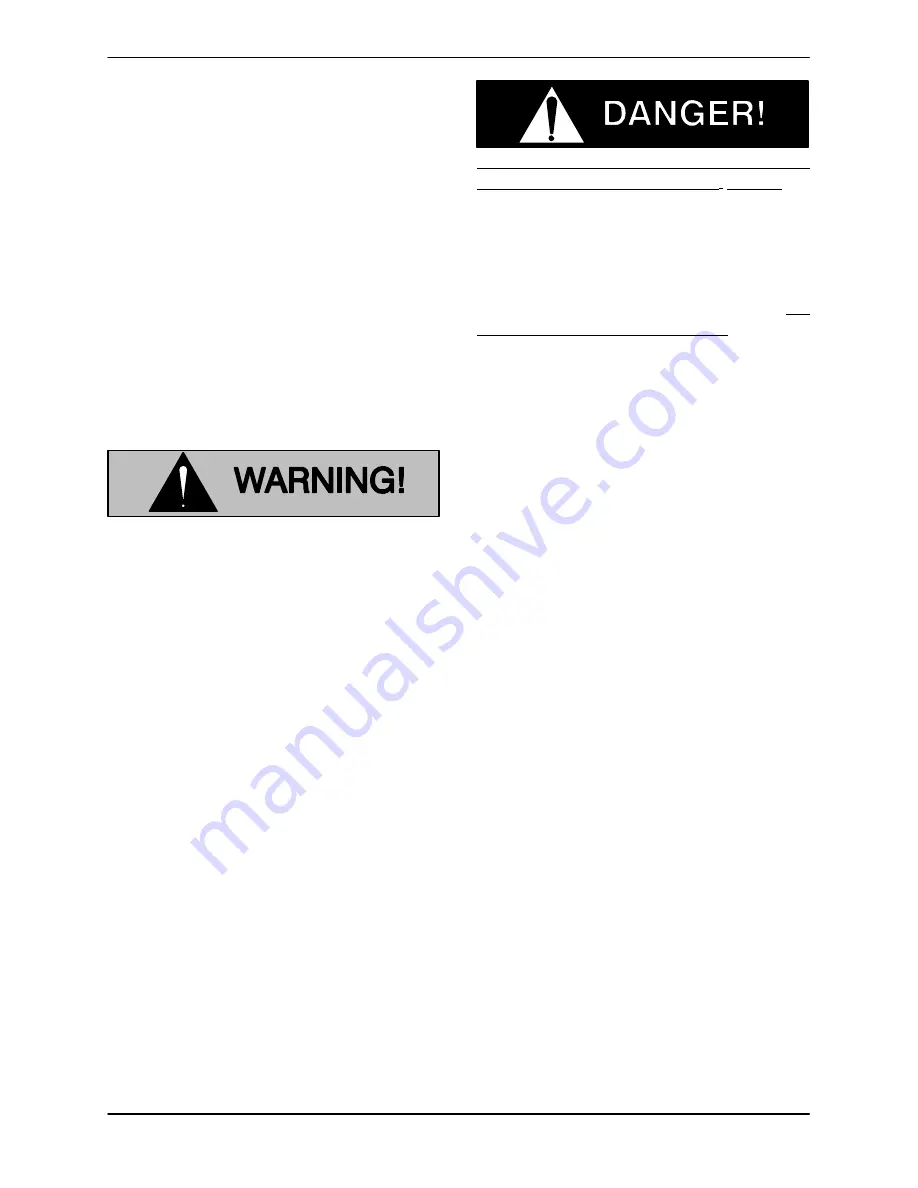
0 SERIES
OM-01160
OPERATION
PAGE C - 2
Lines Without a Bypass
Open all valves in the discharge line and start the
power source. Priming is indicated by a positive
reading on the discharge pressure gauge or by a
quieter operation. The pump may not prime imme
diately because the suction line must first fill with
liquid. If the pump fails to prime within five minutes,
stop it and check the suction line for leaks.
After the pump has been primed, partially close the
discharge line throttling valve in order to fill the line
slowly and guard against excessive shock pres
sure which could damage pipe ends, gaskets,
sprinkler heads, and any other fixtures connected
to the line. When the discharge line is completely
filled, adjust the throttling valve to the required flow
rate.
Do not operate the pump against a
closed discharge throttling valve for
long periods of time. If operated against
a closed discharge throttling valve,
pump components will deteriorate, and
the liquid could come to a boil, build
pressure, and cause the pump casing to
rupture or explode.
Leakage
No leakage should be visible at pump mating sur
faces, or at pump connections or fittings. Keep all
line connections and fittings tight to maintain maxi
mum pump efficiency.
Liquid Temperature And Overheating
The
maximum
liquid temperature for this pump is
160
F (71
C). Do not apply it at a higher operat
ing temperature.
Overheating can occur if operated with the valves
in the suction or discharge lines closed. Operating
against closed valves could bring the liquid to a
boil, build pressure, and cause the pump to rup
ture or explode. If overheating occurs, stop the
pump and allow it to cool before servicing it. Refill
the pump casing with cool liquid.
Allow an over‐heated pump to com
pletely cool before servicing
.
Do not re
move plates, covers, gauges, or fittings
from an over‐heated pump. Liquid with
in the pump can reach boiling tempera
tures, and vapor pressure within the
pump can cause parts being disen
gaged to be ejected with great force. Af
ter the pump completely cools, drain the
liquid from the pump by removing the
casing drain plug. Use caution when re
moving the plug to prevent injury to per
sonnel from hot liquid.
Strainer Check
If a suction strainer has been shipped with the
pump or installed by the user, check the strainer
regularly, and clean it as necessary. The strainer
should also be checked if pump flow rate begins to
drop. If a vacuum suction gauge has been in
stalled, monitor and record the readings regularly
to detect strainer blockage.
Never
introduce air or steam pressure into the
pump casing or piping to remove a blockage. This
could result in personal injury or damage to the
equipment. If backflushing is absolutely neces
sary, liquid pressure
must
be limited to 50% of the
maximum permissible operating pressure shown
on the pump performance curve.
Pump Vacuum Check
With the pump inoperative, install a vacuum gauge
in the system, using pipe dope on the threads.
Block the suction line and start the pump. At oper
ating speed the pump should pull a vacuum of 20
inches (508,0 mm) or more of mercury. If it does
not, check for air leaks in the seal, gasket, or dis
charge valve.
Open the suction line, and read the vacuum gauge
with the pump primed and at operation speed.
Shut off the pump. The vacuum gauge reading will
immediately drop proportionate to static suction
lift, and should then stabilize. If the vacuum reading
falls off rapidly after stabilization, an air leak exists.