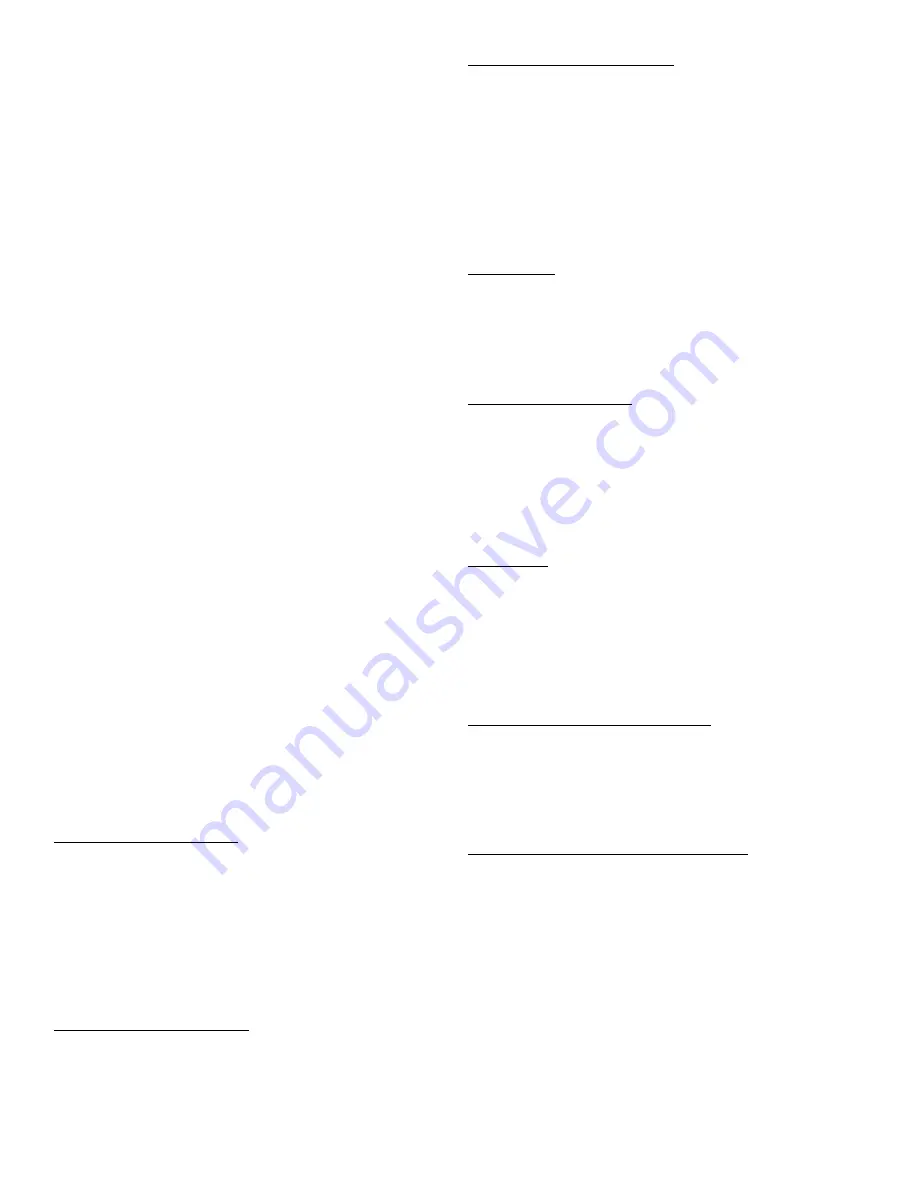
18
cycle is completed, and ignition is reattempted. The control
will repeat this routine three times if a measurable combustion
is not established. The control will then shut off the induced
draft blower and go into a lockout state.
If flame is established but lost, the control will energize the
circulator blower at the heat speed and then begin a new
ignition sequence. If flame is established then lost on
subsequent attempts, the control will recycle for four (4)
consecutive ignition attempts (five attempts total) before
locking out.
The diagnostic fault code is 1 flash for a lockout due to failed
ignition attempts or flame dropouts. The integrated control
will automatically reset after one hour, or it can be reset by
removing the thermostat signal or disconnecting the electrical
power supply for over five seconds. If the diagnostic LED
indicates an external lockout, perform the following checks:
•
Check the supply and manifold pressures
•
Check the gas orifices for debris
•
Check gas valve for proper operation
•
Check secondary limit
A dirty filter, excessive duct static, insufficient air flow, a
faulty limit, or a failed circulator blower can cause this
limit to open. Check filters, total external duct static,
circulator blower motor, blower motor speed tap (see
wiring diagram), and limit. An interruption in electrical
power during a heating cycle may also cause the
auxiliary limit to open. The automatic reset secondary
limit is located on top of the circulator blower assembly.
•
Check rollout limit
If the burner flames are not properly drawn into the
heat exchanger, the flame rollout protection device will
open. Possible causes are restricted or blocked flue
passages, blocked or cracked heat exchanger, a failed
induced draft blower, or insufficient combustion air. The
rollout protection device is a manual reset limit located
on the burner bracket. The cause of the flame rollout
must be determined and corrected before resetting
the limit.
•
Check flame sensor
A drop in flame signal can be caused by nearly invisible
coating on the sensor. Remove the sensor and carefully
clean with steel wool.
•
Check wiring
Check wiring for opens/shorts and miswiring.
Important:
If you have to frequently reset your gas/electric
package unit, it means that a problem exists that should
be corrected. Contact a qualified servicer for further
information.
Pressure Switch Stuck Open
A pressure switch stuck open can be caused by a faulty
pressure switch, faulty wiring, a disconnected or damaged
hose, a blocked or restricted flue, or a faulty induced draft
blower.
If the control senses an open pressure switch during the pre-
purge cycle, the induced draft blower only will be energized. If
the pressure switch opens after ignition has begun the gas
valve is de-energized, the circulator blower heat off cycle
begins, and the induced draft blower remains on. The
diagnostic fault code is two flashes.
Pressure Switch Stuck Closed
A stuck closed pressure switch can be caused by a faulty
pressure switch or faulty wiring. If the control encounters a
pressure switch stuck closed, the induced draft blower
remains off. The diagnostic LED code for this fault is three (3)
flashes.
Open Thermal Protection Device
If the primary limit switch opens, the gas valve is immediately
de-energized, the induced draft and air circulating blowers
are energized. The induced draft and air circulator blowers
remain energized until the limit switch recloses. The
diagnostic fault code for an open limit is four (4) flashes.
A primary limit will open due to excessive supply air
temperatures. This can be caused by a dirty filter, excessive
duct static, insufficient air flow, or a faulty limit. Check filters,
total external duct static, blower motor, blower motor speed
tap (see wiring diagram), and limit. This limit will automatically
reset once the temperature falls below a preset level.
Primary Limit
A primary limit will open due to excessive supply air
temperatures. This can be caused by a dirty filter, excessive
duct static, insufficient air flow, or a faulty limit. Check filters,
total external duct static, blower motor, blower motor speed
tap (see wiring diagram), and limit. This limit will automatically
reset once the temperature falls below a preset level.
Auxiliary/Secondary Limit
A dirty filter, excessive duct static, insufficient air flow, a faulty
limit, or a failed circulator blower can cause this limit to open.
Check filters, total external duct static, circulator blower motor,
blower motor speed tap (see wiring diagram), and limit. An
interruption in electrical power during a heating cycle may
also cause the auxiliary limit to open. The automatic reset
secondary limit is located on top of the circulator blower
assembly.
Rollout Limit
If the burner flames are not properly drawn into the heat
exchanger, the flame rollout protection device will open.
Possible causes are restricted or blocked flue passages,
blocked or cracked heat exchanger, a failed induced draft
blower, or insufficient combustion air. The rollout protection
device is a manual reset limit located on the burner bracket.
The cause of the flame rollout must be determined and
corrected before resetting the limit.
Flame Detected with Gas Valve Closed
If flame is detected with the gas valve de-energized, the
combustion and air circulator blowers are energized. The
diagnostic fault code is five (5) flashes for this condition. The
control can be reset by removing the power supply to the unit
or it will automatically reset after one hour. Miswiring is the
probable cause for this fault.
Low Flame Signal (Two-Stage Models ONLY)
Under some conditions, the fuel or air supply can create a
nearly invisible coating on the flame sensor. This coating acts
as an insulator causing a drop in the flame signal. If the flame
signal drops below a predetermined value, the ignition control
will display an error code of (1) flash on the amber diagnostic
LED. The unit will continue to operate until the control can no
longer detect flame.
Содержание Maytag Amana A/GPG14 M Series
Страница 38: ...38 THIS PAGE LEFT INTENTIONALLY BLANK...
Страница 39: ...39 THIS PAGE LEFT INTENTIONALLY BLANK...