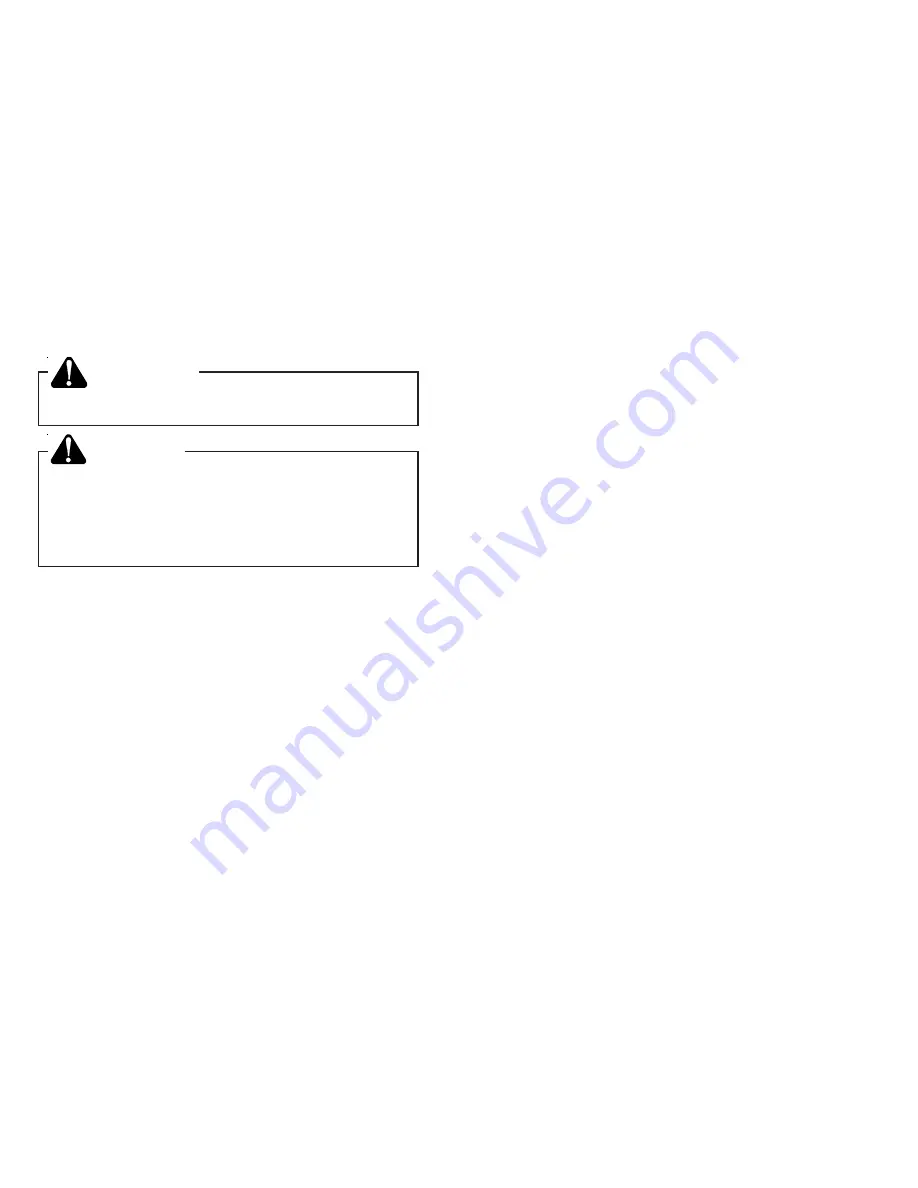
IO-213D
2/04
16
This control is located in the circulating air blower
compartment. Upon a demand for heat, the venter is
energized. After a short purge, the electronic ignition device
is energized. The burners are ignited after a short delay and
the burner flame is proven. The circulating air blower is
energized at approximately 30 seconds after the burners
are ignited. The circulating air blower off time is field
selectable at 90, 120 or 150 seconds. THIS CONTROL IS
NOT FIELD SERVICEABLE.
CIRCULATING AIR FILTERS
One of the most common causes of problems in a forced
air heating system is blocked or dirty filters. Circulating air
filters must be inspected monthly for dirt accumulation and
replaced if necessary. Failure to maintain clean filters can
cause premature heat exchanger failure. A new home may
require more frequent replacement until all construction dust
and dirt is removed. Circulating air filters must be installed
external to the furnace cabinet.
CAUTION
BEFORE PERFORMING ANY SERVICE ON THIS FURNACE,
DISCONNECT THE MAIN POWER SUPPLY.
CAUTION
DO NOT
OPERATE THE FURNACE WITHOUT THE
CIRCULATING AIR FILTERS IN PLACE. DUST AND DIRT IN
THE AIR WILL RESTRICT THE AIR MOVEMENT OVER THE
SECONDARY COIL CAUSING NUISANCE CYCLING OF
SAFETY CONTROLS, WHICH MAY RESULT IN A “NO HEAT
CONDITION.”
TEMPERATURE RISE
The temperature difference between the outlet air and the
inlet air of the furnace is known as the temperature rise.
This furnace is designed to operate within the temperature
rise displayed on the furnace series and rating plate. To
ensure satisfactory performance, the temperature rise of
the furnace must be measured and adjusted if necessary.
Use the following procedure to measure and adjust the
temperature rise;
• Prior to starting the furnace, visually inspect all joints and
seams in the supply and return air ducts for leaks. Repair
them if necessary.
• Adjust the room thermostat to obtain constant operation.
• Allow the furnace to operate for at least fifteen (15) minutes.
• With an accurate thermometer, measure the temperature
at the return air grille. If a combination indoor / outdoor
system is used, the temperature must be measured
downstream of the connection.
• Measure the outlet air temperature at a point approximately
twelve to eighteen (12 -18) inches from the supply air duct
opening of the furnace. It may be necessary to measure
the outlet air at several places to obtain an accurate
average. NOTE: IF AN AIR CONDITIONING COIL IS
INSTALLED, TAKE CARE SO AS NOT TO DAMAGE THAT
COIL.
• Adjust the temperature rise by changing circulating air
blower speed tap.
MOTOR LUBRICATION AND MAINTENANCE
The circulating air blower is equipped with bearings that are
permanently lubricated by the motor manufacturer and
require no additional lubrication. At the time of the monthly
filter inspection, clean the exterior of the circulating air motor,
especially around the perimeter air holes to prevent the
possibility of overheating due to an accumulation of dust or
dirt on the windings and motor casing. As suggested
elsewhere in these instructions, the air filters are to be kept
clean. Dirty filters will restrict the airflow over the motor
windings and possibly cause an overheating condition. The
venter motor has bearings that are prelubricated by the motor
manufacturer and require no attention.
SERVICE INSTRUCTIONS
•
DO
keep the circulating air filters clean. The heating system
will operate more efficiently and economically.
•
DO
arrange drapes and furniture so that the supply air
registers and return air grilles are unobstructed.
•
DO
close doors and windows. This will reduce the heat
load on the system.
•
DO
avoid excessive use of bathroom and kitchen exhaust
fans.
•
DO NOT
let heat generated by televisions, lamps, direct
sunlight, etc. influence the thermostat operation.
•
DO NOT
use the furnace room as a storage area.
•
DO NOT
store gasoline or other flammable liquids or vapors
in the vicinity of the furnace.
•
EXCLUSIVE
of the mounting platform, keep all
combustible materials at least 3 feet from the Furnace.
SEQUENCE OF OPERATION
This appliance is controlled by the thermostat. Within this
section, the term lockout is referenced. This lockout is a
“soft” lockout, which will reset after one hour. It is the
obligation of the installer to educate the user on the proper
use of the thermostat and the sequence of operation in both
the heating and cooling modes. It is also important that any
repair or service be performed by a QUALIFIED service
person, not by the user.
Heating Mode
• The furnace control checks for an open main limit (this
limit is normally closed). If the limit is open, the furnace
will remain inoperable until the limit is closed. During an
open limit, the circulating air blower will be energized. The
status light will blink four (4) times.
• The room thermostat reacts to a demand for heat.
• The control will then check to insure that the vent pressure
switch is open. If, at this point, the vent pressure switch is
closed, the control will blink two (2) times and will remain
inoperable until this situation is corrected.
• The venter blower is energized.
• The vent pressure switch will close when it detects a
pressure in excess of its setting. If the pressure switch
fails to close, the status light will flash three (3) times. The
sequence cannot continue until the pressure switch closes.
• After a pre-purge of about fifteen (15) seconds, the
electronic ignition device will be energized.
• The flame rollout switches are then checked to assure
they are in the closed position.
• After a slight delay, the gas valve will open if the flame
rollout switches are closed.
• The burners will ignite and the flame sensor will detect the
presence of flame. The ignition device will deenergize. If
the sensor does not detect the burner flame, the gas valve
will close and the ignition cycle will be repeated for a total
of three attempts. If, after the third attempt, the presence of
flame is not detected, the furnace will go into a lockout
condition for one (1) hour. It will then repeat the ignition
cycle. This one (1) hour lockout and retry will occur
indefinitely.