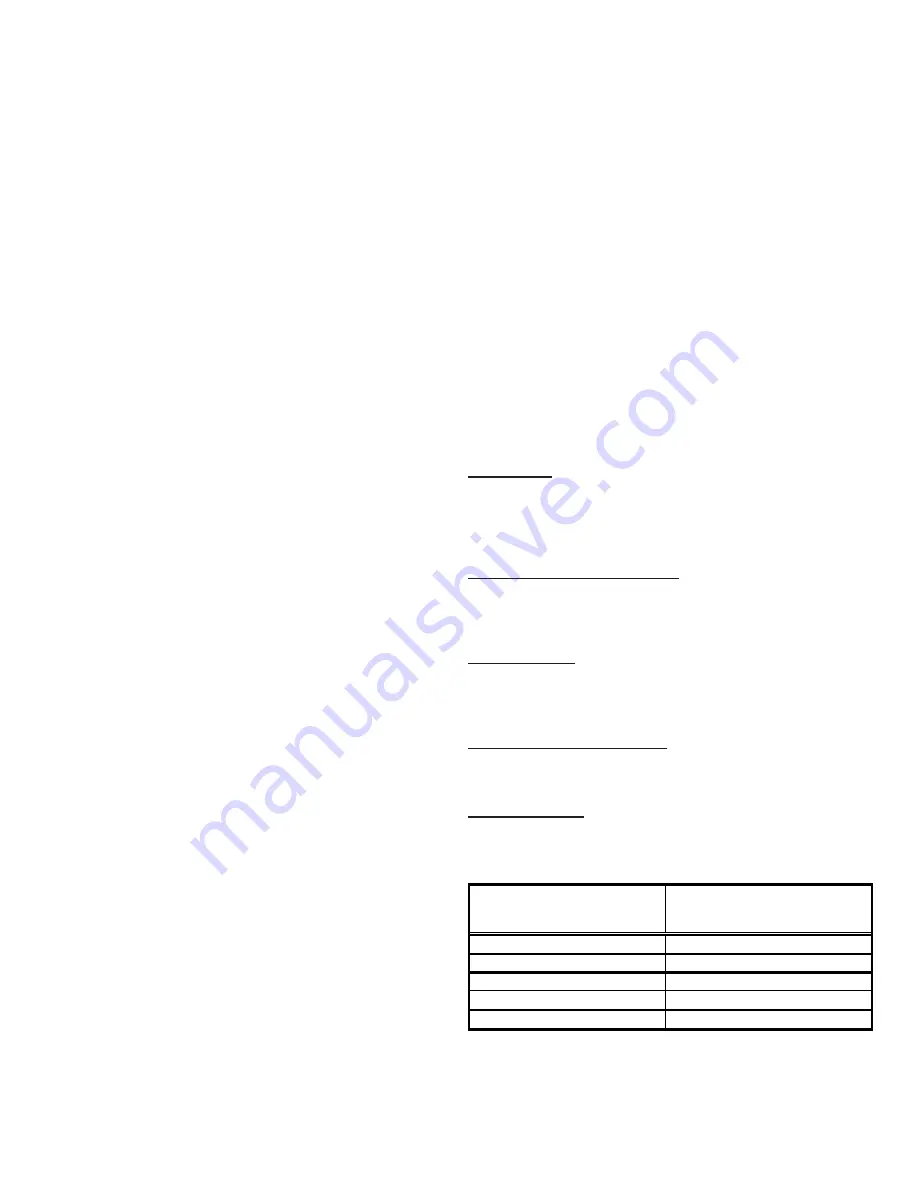
9
During defrost the following actions occur:
1. The reversing valve is energized and the heat pump
operates in the cooling mode.
NOTE:
A 30 second compressor delay at defrost initiation/
termination is optional. As shipped from the factory, the
control is set for the delay (“DLY”), which will turn the
compressor off for 30 seconds while the reversing valve
shifts to/from the cooling mode position. To bypass the
delay, which typically reduces sound levels during de-
frost mode, change the pin settings from “DLY” to
“NORM”.
2. The airhandler auxiliary heat (if equipped) is activated.
3. The condenser fan motor is shut-off.
If the defrost cycle has not terminated after ten (12) minutes
the control will override the defrost sensor and revert to a
heating mode.
The defrost control has test pins which can be useful when
troubleshooting in the heating mode. These test pins accel-
erate the compressor run time counter. The suggested
method for accessing this feature is:
1. Run unit in heat mode.
2. Check unit for proper charge.
NOTE:
Bands of frost indicate low refrigerant charge.
3. Shut off power to unit.
4. Disconnect outdoor fan by removing the purple lead from
the Condenser Fan Defrost Relay.
5. Restart unit and allow frost to accumulate.
6. After a few minutes the defrost thermostat should close.
To verify the position of the thermostat check for 24V
between “DFT” and “C” on the defrost board. Should
the defrost thermostat fail to close after a heavy build-
up of frost and the thermostat is less than 28
°
, the ther-
mostat is to be replaced.
7. After the thermostat has closed, short across the test
pins with the a screw
driver blade until the reversing valve
shifts. This could take up to 22 seconds depending upon
the position of the timing setting on the defrost board.
Immediately upon the action of the reversing valve, re-
move the short.
Note:
If this short is not removed im-
mediately, the defrost activity will last only 3 seconds.
8. After defrost has terminated (up to 12 minutes) check
the defrost thermostat for 24V between “DFT” and “C”.
This reading should be 0V (open sensor).
9. Shut off power to the unit.
10. Replace outdoor fan motor wire removed in Step d.
NOTE:
The compressor “run time’ is accumulative during
multiple heating cycles. The timer will reset to zero only when
the defrost sensor returns to an open condition. If the room
thermostat is operating in the “EM HT” mode, no accumulation
of compressor time is recorded.
Troubleshooting (Qualified Installer/Servicer
Only)
When troubleshooting, the first step should always be to check
for clean coils, clean filter(s), and proper airflow. Indoor air-
flow should be 375 to 425 CFM per ton of cooling based on
the size of the outdoor unit. The most common way of estab-
lishing indoor airflow is heating temperature rise. Indoor air-
flow will then be (Heating output of equipment) / (1.1 x temp.
rise). In other cases, measurement of external static pres-
sure is helpful. For details, see the Installation Instructions
for your indoor unit.
Common Causes for Unsatisfactory Operation
of Heat Pumps in Heating Mode
Dirty Filters
Dirty filters or inadequate airflow through the indoor coil. Fail-
ure to keep clean filters and adequate airflow (375-425 CFM/
ton) will cause excessive discharge pressures that may cause
the high-pressure switch to function.
Low Return Air Temperatures
Return ductwork temperatures that are less than 60°F will
cause low discharge pressure, low suction pressure and ex-
cessive defrost cycling.
Undercharging
An undercharged system will cause low discharge pressure,
low suction pressure and an accumulation of frost on the lower
section of the outdoor coil.
Poor Termination of Defrost
The defrost sensor must make good contact with the outside
coil return bend or a non-termination of defrost may occur.
Reversing Valve
A reversing valve may not function correctly for the following
reasons:
Solenoid does not energize
when voltage is present.
Replace t he reversing valve.
No voltage to the solenoid.
Check the wiring.
The valve will not shift.
a. Undercharged
Check for leaks
b. Valve body damage
Replace t he reversing valve
c. Valve sticking
Replace t he reversing valve
Содержание CONDENSING UNIT
Страница 11: ...11 THIS PAGE INTENTIONALLY LEFT BLANK ...
Страница 23: ...11 THIS PAGE INTENTIONALLY LEFT BLANK ...