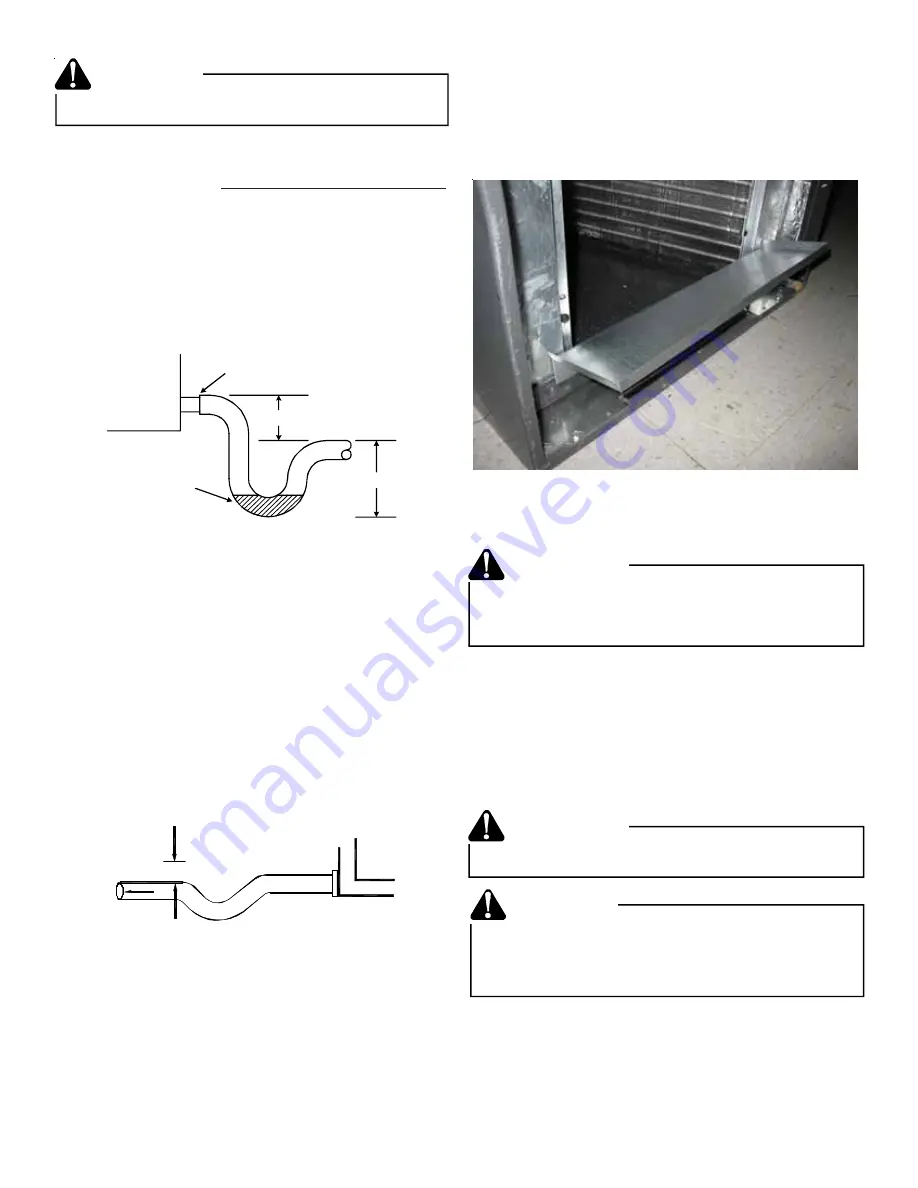
3
If secondary drain is not installed, the secondary access
must be plugged.
CAUTION
NOTE:
Trapped lines are required by many local codes. In the
absence of any prevailing local codes, please refer to the
requirements listed in the Uniform Mechanical Building Code.
A drain trap in a
draw-through
application prevents air from
being drawn back through the drain line during fan operation
thus preventing condensate from draining, and if connected to
a sewer line to prevent sewer gases from being drawn into the
airstream during blower operation. In a
blow-through
applica-
tion the drain trap prevents conditioned air from escaping. It is
permissible in this application to use a shallow trap design
sometimes referred to as a running trap.
Cased Coil
3" MIN.
POSITIVE LIQUID SEAL
REQUIRED AT TRAP
Drain
Connection
2" MIN.
Figure 4
Condensate Drain Trap
The depth of a running trap (Figure 5) should be either 1" or a
depth that permits unrestricted condensate drainage without
excessive air discharge.
Field experience has shown condensate drain traps with an
open vertical Tee between the air handler and the condensate
drain trap can improve condensate drainage in some applica-
tions, but may cause excessive air discharge out of the open
Tee. The manufacturer does not prohibit this type of drain but
we also do not recommend it due to the resulting air leakage.
Regardless of the condensate drain design used, it is the
installer’s responsibility to ensure the condensate drain sys-
tem is of sufficient design to ensure proper condensate re-
moval from the coil drain pan.
PITCH
TOWARDS
DRAIN
1” MIN
TRAP
CONDENSATE
DRAIN CONN.
CONNECT DRAIN
SAME SIZE AS ON
UNIT OR LARGER
Figure 5
Running Trap
Horizontal Coil Water Blower-Off Bracket
CHPF4860 coils are shipped with an accessory kit containing
a sheet metal bracket. For horizontal-left applications where
the airflow may exceed 1600 CFM, this bracket must be
installed on the left side of the drain pan as shown in Figure 6.
Figure 6
Horizontal Blow-Off Bracket
Refrigerant Lines
A quenching cloth is strongly recommended to
prevent scorching or marring of the equipment
finish when welding close to the painted surfaces.
Use brazing alloy of 5% minimum silver content.
WARNING
All cut ends are to be round, burr free, and cleaned. Any other
condition increases the chance of a refrigerant leak. Use a
pipe cutter to remove the closed end of the spun closed suc-
tion line.
To avoid overheating after brazing, quench all welded joints
with water or a wet rag.
For the correct tubing size, follow the specification for the con-
denser/heat pump
The coil is shipped under pressure. Follow these
instructions to prevent injury.
WARNING
Applying too much heat to any tube can melt the tube. Torch
heat required to braze tubes of various sizes must be
proportional to the size of the tube. Service personnel must
use the appropriate heat level for the size of the tube being
brazed.
CAUTION
NOTE:
Tubes of smaller size require less heat to bring the
tube to brazing temperature before adding brazing alloy. The
use of a heat shield when brazing is recommended to avoid
burning the serial plate or the finish on the unit.