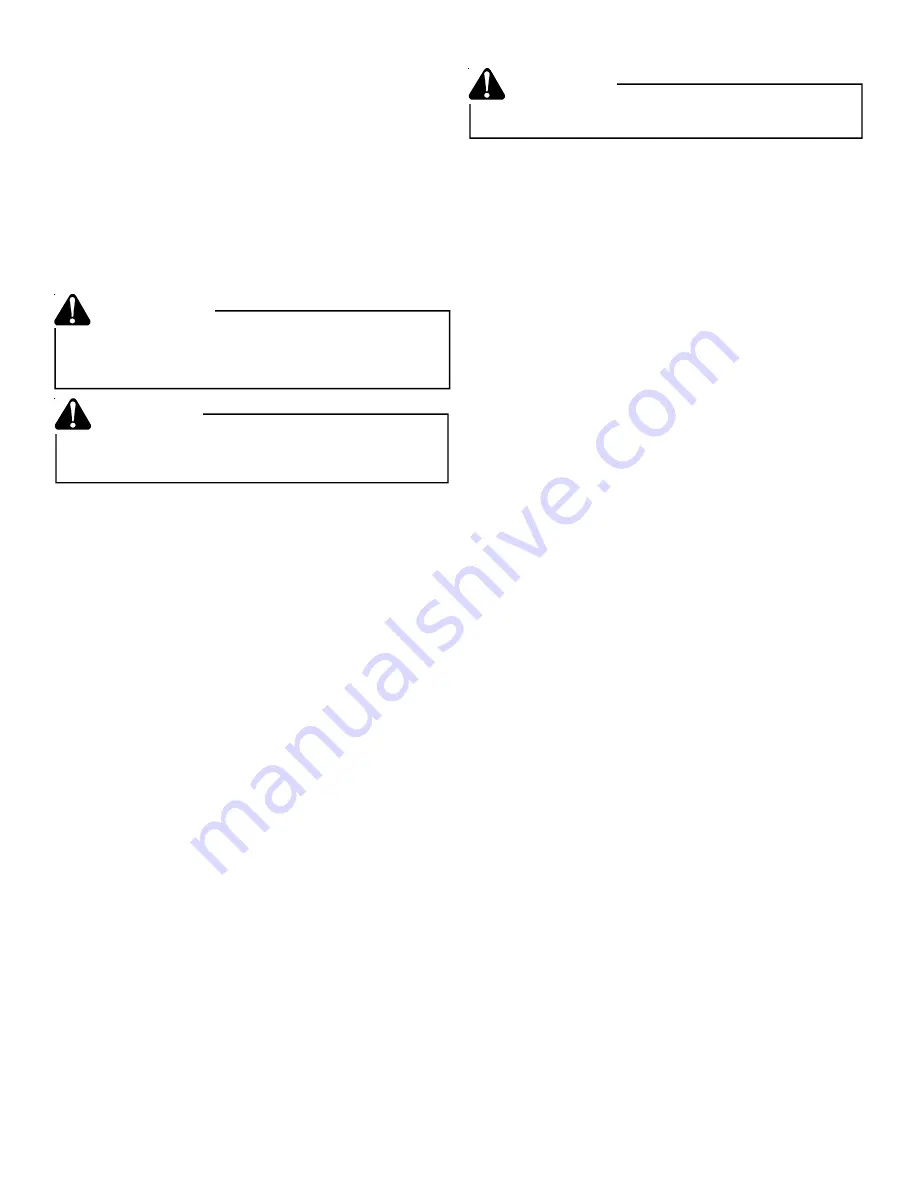
4
Special Instructions
This airhandler comes equipped with an evaporator coil with a
check style flowrator assembly, an indoor blower and all nec-
essary internal electrical wiring. For most installations with
matching applications, no change to the flowrator orifice is re-
quired. However, in mix-matched applications, a flowrator
change may be required. See the Goodman piston kit chart or
consult your local distributor for details regarding mix-matched
orifice sizing. If the mix-match application requires a different
piston size, change the piston in the distributor on the indoor
coil before installing the coil and follow the procedure in this
section.
The evaporator coil is shipped from the factory with
approximately 90 PSI tracer gas charge. Use caution
when relieving pressure.
WARNING
To prevent feeder tube damage, hold the distributor body
with a 3/4" open end wrench when removing or replacing
the 13/16" flare nut.
CAUTION
1. Remove the valve core to allow high pressure tracer gas
to escape. No gas indicates a possible leak.
2. Remove the 13/16" flare nut and tailpiece.
3. Unsweat the access fitting on the tailpiece
4. Remove the check piston to verify it is correct and then
replace the piston. See piston kit chart in instructions.
5. Unsweat the cap on the suction line.
6. Slide the 13/16" flare nut over the tailpiece
.
7. Braze tailpiece to the lineset liquid tube.
8. Insert the suction line into the connection, slide the insu-
lation at least 18" away from the braze joint. Braze suc-
tion line.
9.
AFTER THE TAILPIECE HAS COOLED
, confirm posi-
tion of the white Teflon® seal and hand tighten the 13/16"
flare nut.
10. Torque the 13/16" flare nut to 10-25 ft-lbs or tighten 1/6th
turn.
Excessive torque can cause orifices to stick. Use the proper
torque settings when tightening orifices.
CAUTION
11. Replace suction line insulation.
12. After installation, evacuation and charging of the low side
is complete, check fittings for leaks.
NOTE:
With the piston in the distributor, the seal end should
point inside the distributor body and should not be seen when
looking into the end of distributor. Make sure the piston is free
to rotate, and move up and down in the distributor body.
MAINTENANCE
Periodic Checkup and Service
This unit is designed to provide many years of dependable,
trouble-free comfort when properly maintained. Proper mainte-
nance will consist of annual checkups and cleaning of the in-
ternal electrical and heat transfer components by a qualified
service technician. Failure to provide periodic checkup and
cleaning can result in excessive operating cost and/or equip-
ment malfunction.