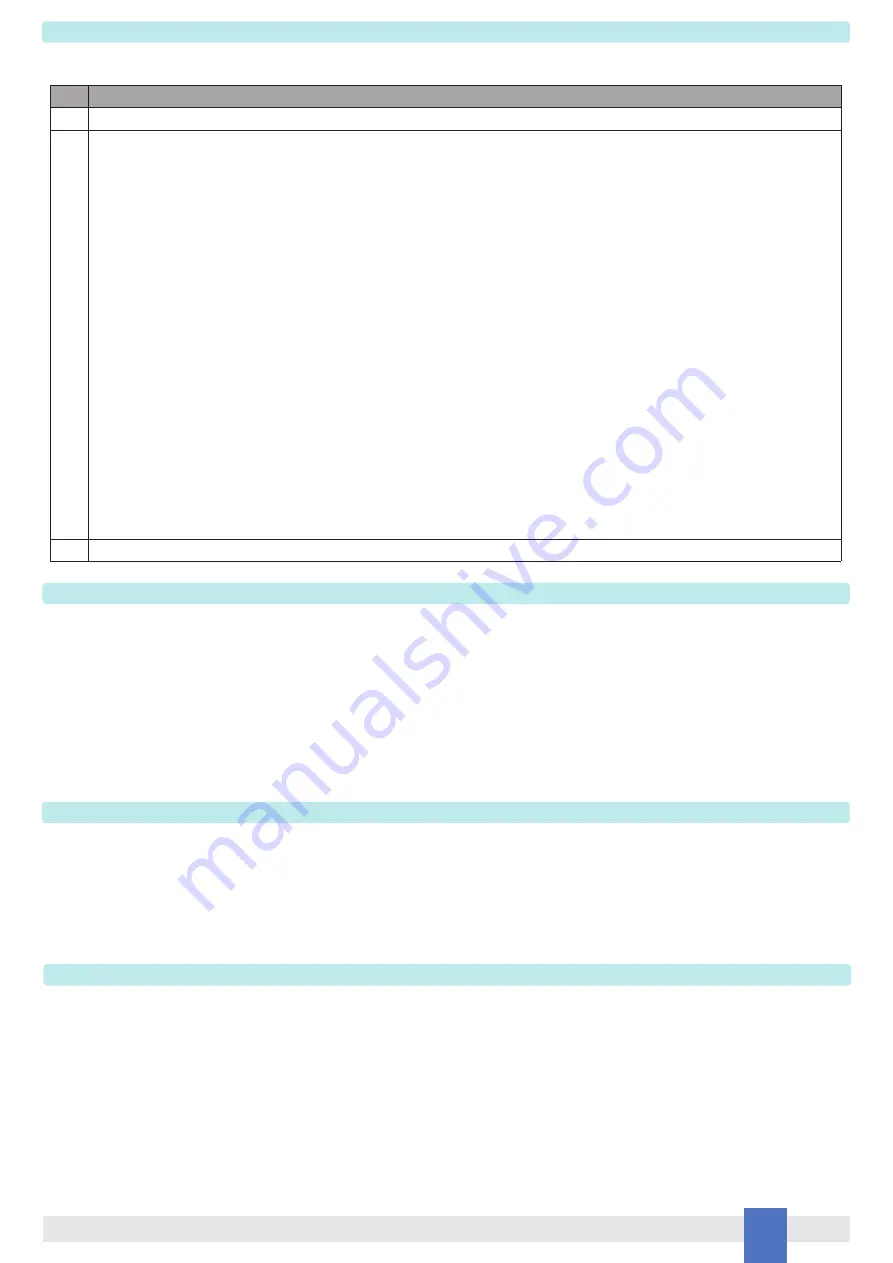
7
D5091
- 5 A SIL 3 Relay Output Module for ND Load with ND or NE Relay condition
G.M. International ISM0110-12
The proof test shall be performed to reveal dangerous faults which are undetected by diagnostic. This means that it is necessary to specify how dangerous undetected faults, which
have been noted during the FMEDA, can be revealed during proof test. The Proof test consists of the following steps:
Testing procedure at T-proof
Steps
Action
1
Bypass the safety-related PLC or take other appropriate action to avoid a false trip when removing the unit for test.
2
For the single channel, verify the input-to-output functionality:
1. For De-energized relays and open contacts, terminals “7”-“8”, the output load is normally de-energized when the input channel is off, while the activation of the input
channel energizes the load (safe state).
2. For Energized relays and open contacts, terminals “9”-“10”, the output load is normally de-energized when the input is supplied, while the shutdown of the input
channel energizes the load (safe state).
The channel functionality must be verified for a min to max input voltage change (21.6 to 27.6 Vdc).
In addition, the use of three relays for the single output channel, where the contacts are connected in parallel, requires to control the single coils by means of DIP-switch
(n°1, 3, 5) and to check the ohmic continuity of the contacts, as described in the following procedures.
1. Do not supply the input channel (terminals “1”-“2”) of the unit under test and verify that the ohmic continuity at the output contact terminals “7”-“8” is absent (i.e. the
parallel connection of the 3 NO contacts is open:
1
st
requisite is verified
). But this condition could also be true if all contacts are normally open except one, which is
blocked (for welding) into open position: this will be verified testing the channel when input is supplied (see
3
rd
requisite
). Instead, the presence of ohmic continuity
implies that at least one relay contact is blocked (for welding) into closed position: this could only be verified disassembling and individually testing each relay.
2. Do not supply the input channel (terminals “1”-“2”) of the unit under test and verify that the ohmic continuity at the output contact terminals “9”-“10” is present (i.e. the
parallel connection of the 3 NC contacts is closed:
2
nd
requisite is verified
). But this condition could also be true if only one contact is closed and others are blocked
(for welding) into closed or open position: this will be verified testing the channel when input is supplied (see
4
th
requisite
). Instead, the absence of ohmic continuity
implies that all relay contacts are blocked (for welding) into open position.
3. Supply the input channel (terminals “1”-“2”) of the unit under test and verify that the ohmic continuity at the output contacts (terminals “7”-“8”) is present (i.e. the
parallel connection of the 3 NO contacts is closed:
3
rd
requisite is verified
). The absence of ohmic continuity implies that all relay contacts are blocked (for welding)
into
open position. Instead, to verify if a single contact is blocked (for welding) into open position, use the DIP-switches (n°1, 3, 5) to short circuit each possible couple
among the 3 relay coils (starting with 1
st
& 2
nd
coils by DIP-switches n°1 & 3, then going with 1
st
& 3
rd
ones by DIP-switches n°1 & 5, and finally proceeding with 2
nd
&
3
rd
ones by DIP-switches n°3 & 5), verifying that ohmic continuity is always present between terminals “7”-“8”. In this situation, the absence of ohmic continuity implies
that a relay contact (the only one with energized coil because the others are de-energized) is blocked (for welding) into open position.
4. Supply the input channel (terminals “1”-“2”) of the unit under test and verify that the ohmic continuity at the output contacts (terminals “9”-“10”) is absent (i.e. the
parallel connection of the 3 NC contacts is closed:
4
th
requisite is verified
). The presence of ohmic continuity implies that at least one relay contact is blocked (for
welding) into closed position: this could only be verified after disassembling and individually testing each relay. Instead, to verify if a contact is blocked (for welding)
into open position, use internal DIP-switches (n°1, 3, 5) to put in short circuit one relay coil at a time (starting with the 1
st
coil by DIP-switch n°1, then going on with the
2
nd
one by DIP-switch n°3, and finally proceeding with the 3
rd
one by DIP-switch n°5), verifying that the ohmic continuity is always present between terminals “9” &
“10”. In this situation, the absence of ohmic continuity implies that a relay contact (the only one with de-energized coil) is blocked (for welding) into open position.
3
Remove the bypass from the safety-related PLC or restore normal operation inserting the unit.
This test reveals almost 99 % of all possible Dangerous Undetected failures in the relay module.
Warning
Operation
D5091S relay module is suitable for the switching of safety related circuits, providing isolation between the input and output contacts.
D5091S provides 1 SPDT contact for two different safety functions:
1) SIL 3 Safety Function for Normally De-Energized load (energized in fail safe state) is available at Terminal Blocks 7-8. The driving signal is normally low (0 Vdc),
the relay is normally de-energized, contact is open and load is de-energized. The safety function is met when the driving signal is high (24 Vdc), the relay is energized,
contact is closed and load is energized. At Terminal Blocks 9-10 is also available a service contact (for service load) with opposite (not SIL) function.
2) SIL 3 Safety Function for Normally De-Energized load (energized in fail safe state) is available at Terminal Blocks 9-10. The driving signal is normally high (24 Vdc),
the relay is normally energized, contact is open and load is de-energized. The safety function is met when the driving signal is low (0 Vdc), the relay is de-energized,
contact is closed and load is energized. At Terminal Blocks 7-8 is also available a service contact (for service load) with opposite (not SIL) function.
A “RELAY STATUS” yellow led lights when input is powered, showing that relay is energized.
Installation
D5091 series are relay output module housed in a plastic enclosure suitable for installation on EN/IEC60715 TH 35 DIN-Rail or on customized Termination Board.
D5091 series can be mounted with any orientation over the entire ambient temperature range.
Electrical connections are accommodated by polarized plug-in removable screw terminal blocks which can be plugged in/out into a powered unit without suffering or causing any damage
(for Zone 2 installations check the area to be nonhazardous before servicing).
Connect only one individual conductor per each clamping point, use conductors up to 2.5 mm²
(13 AWG) and a torque value of 0.5
-
0.6 Nm. Use only cables that are suitable for a temperature of at least 85°C.The wiring cables have to be proportionate in base to the current and the
length of the cable.
On the section “Function Diagram” and enclosure side a block diagram identifies all connections.
Identify the function and location of each connection terminal using the wiring diagram on the corresponding section, as an example:
Connect positive input at terminal “1” and negative input at “2”.
Connect positive or AC load supply line to SPDT Output Common pole (terminal “7” or “9”).
Connect SIL 3 Normally De-Energized load between negative or AC load supply line and the terminal “8” (when relays are normally de-energized) or the terminal “10” (when relays are
normally energized), as previously shown in the Functional Safety applications.
Installation and wiring must be in accordance to the relevant national/international installation standards (e.g. EN/IEC60079
-
14 Electrical apparatus for explosive gas atmospheres
-
Part
14: Electrical installations in hazardous areas (other than mines)), make sure that conductors are well isolated from each other and do not produce any unintentional connection.
Connect load relay contacts checking the load rating to be within the contact maximum rating (5 A 250 Vac 1250 VA, 5 A 250 Vdc 140 W resistive load).
D5091 series are electrical apparatus installed on EN/IEC60715 TH 35 standard DIN-Rail located in Safe Area/Non Hazardous Locations or Zone 2, Group IIC T4 or Class I, Division 2,
Group A, B, C, D, T4 Hazardous Area within the specified operating temperature limits Tamb - 40 to +70 °C.
D5091 series must be installed, operated and maintained only by qualified personnel, in accordance to the relevant national/international installation standards (e.g. IEC/EN60079-14
Electrical apparatus for explosive gas atmospheres - Part 14: Electrical installations in hazardous areas (other than mines)), following the established installation rules. De-energize
power source (turn off power supply voltage) before plug or unplug the terminal blocks when installed in Hazardous Area or unless area is known to be nonhazardous.
Warning: substitution of components may impair suitability for Zone 2/Division 2. Avertissement: la substitution des composants peut nuire à l’aptitude à la Zone 2/Div. 2.
Explosion Hazard: to prevent ignition of flammable atmospheres, disconnect power before servicing or unless area is known to be nonhazardous. Danger d'Explosion: pour
éviter l’inflammation d’atmosphères inflammables, débrancher l’alimentation avant l’entretien ou à moins que région est connue pour être non dangereuse.
Warning: de
-
energize main power source (turn off power supply voltage) and disconnect plug
-
in terminal blocks before opening the enclosure to avoid electrical shock
when connected to live hazardous potential. Avertissement: débrancher l’alimentation (couper la tension d'alimentation) et les blocs de jonction enfichables avant d’ouvrir
le boîtier pour éviter les chocs électriques lorsqu’ils sont connectés à un potentiel dangereux.
Failure to properly installation or use of the equipment may risk to damage the unit or severe personal injury.
The unit cannot be repaired by the end user and must be returned to the manufacturer or his authorized representative. Any unauthorized modification must be avoided.