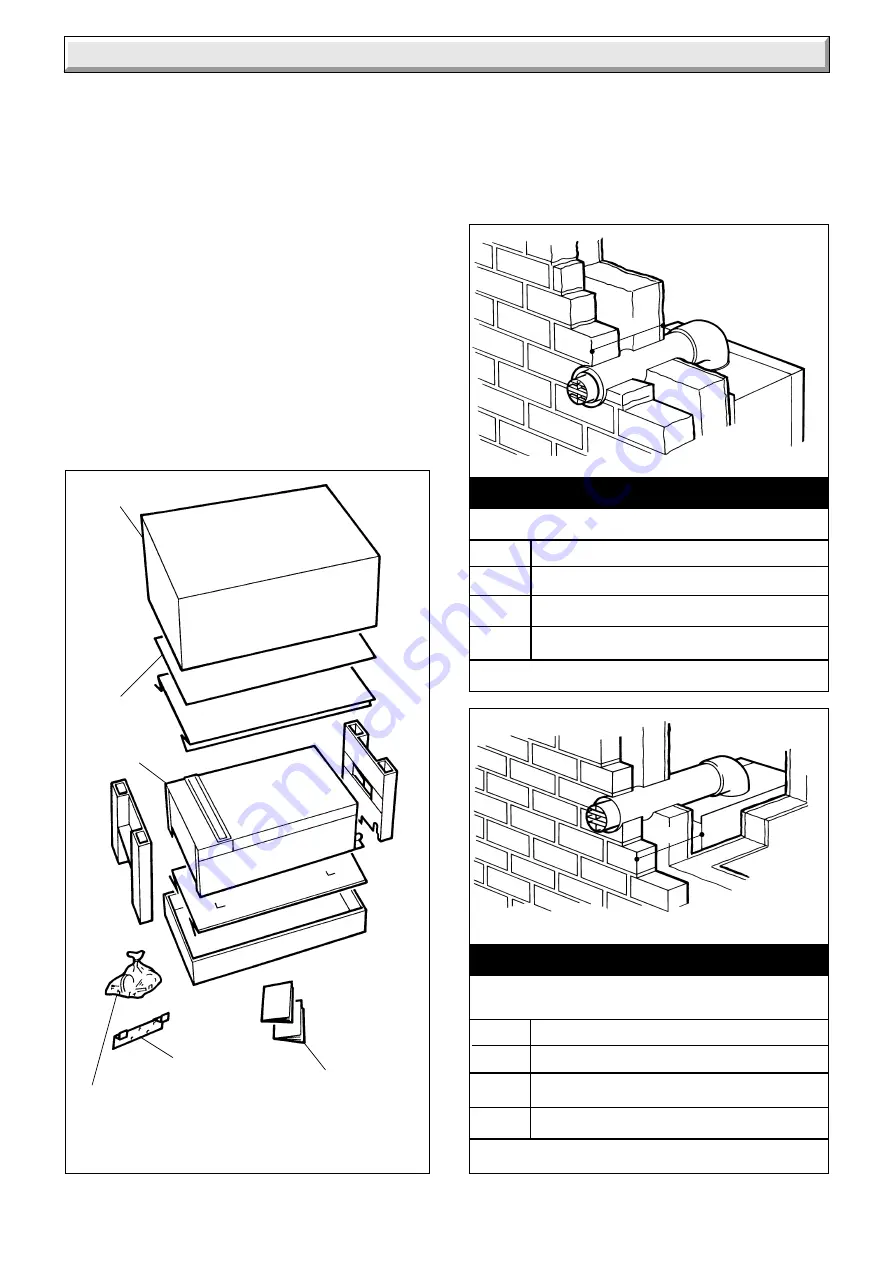
13
221966B
4.1 Unpacking
Open the carton, check the items supplied against the boiler
pack contents list on the flap, see diagram 4.1.
4.2 Flue Position and Length
Determine flue applications, length and terminal position before
starting.
Refer to diagram 4.2 or 4.3.
Note. If a longer flue duct is required DO NOT extend the
ducting.
A 1, 2 or 3metre flue system and terminal MUST be used, for the
100FF and 1 or 2 metre only for the 120FF.
Note: If required, an optional Wall Liner Kit, part No.452481, is
available, complete with fixing instructions.
4.3 Flue Preparation
All flue assemblies are designed for internal installation (optional
wall liner is required), given that there is sufficient clearances
opposite to the flue for the installation of the flue.
If there is insufficient clearance the flue can be installed from
outside.
Diagram 4.3
6854
Diagram 4.1
4792
CARTON
Standard Flue terminal illustrated.
MOUNTING
BRACKET
INSTRUCTIONS
LOOSE
ITEMS PACK
BOILER
WALL
TEMPLATE
'S'
SIDE FLUE LENGTHS
Distance S = External wall face to boiler case
STD.
81mm to 346mm
1M
81mm to 830mm
2M
81mm to 1830mm
*3M
81mm to 2830mm *100FF ONLY
Diagram 4.2
4275
Standard Flue terminal illustrated.
REAR FLUE LENGTHS
Distance R = Wall thickness
STD.
75mm to 438mm
1M
75mm to 928mm
2M
75mm to 1928mm
*3M
75mm to 2928mm *100FF ONLY
'R'
For a wall thickness up to 300mm, provided that there is
sufficient space and the optional wall liner kit is used the flue can
be fully installed from the inside.
For a wall thickness of over 300mm the external flue hole will
need to be made good from the outside. This applies also if you
use the flue kit without the optional kit, irrespective of wall
thickness.
4 Flue and Appliance Preparation