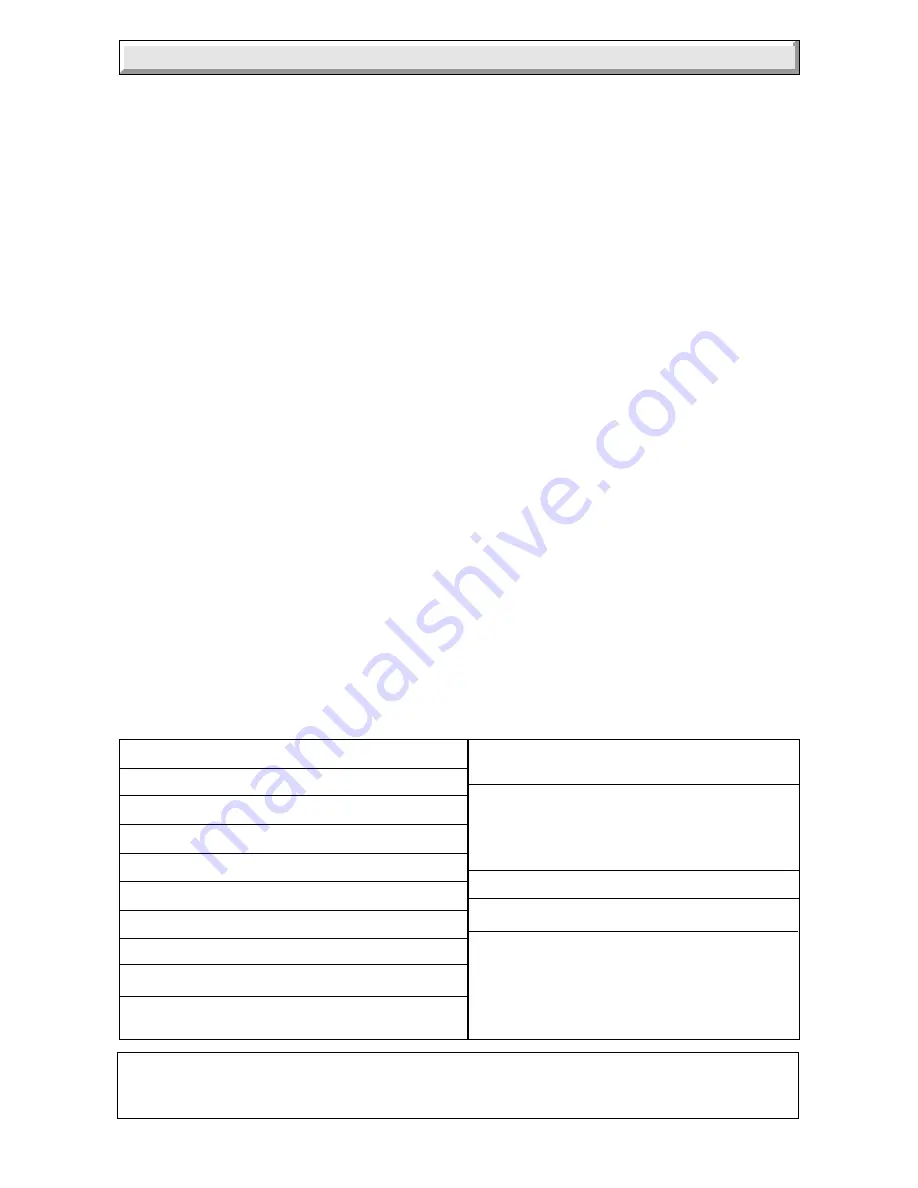
3
221138C
❋
D.H.W
0.5 to 10bar
working pressure
(7.25 to 188lbf/in
2
)
■
Maximum Heating
119 litres
system water
(26.2 gallons)
content using
with a cold
fitted expansion
fill pressure
vessel.
of 0.7bar
Electrical supply
230V~50Hz
Electrical rating
154W fused 3A
Internal Fuse rating
1) Type T2A
2) Type T630mA
Lift Weight
37.0kg (81.4lb)
Total Weight
50.4kg (111lb)
●
Gas connection
Rc
1
/
2
(
1
/
2
in BSPT)
●
Heating and return
22mm compression
●
Domestic hot water
15mm compression
Safety valve
Preset 3bar (43.5lbf/in
2
)
Safety valve discharge
15mm copper
Water content
1.74 litres (0.38 gallon)
■
Expansion vessel capacity 8 litres (1.76 gallons)
Heating cold fill
0.7bar
pressure minimum
(10.1lbf/in
2
)
1 G e n e r a l
■
For larger systems use an additional expansion vessel, see Section 4.
❋
Boiler starts at an inlet pressure of 0.5bar but requires 0.8bar for maximum output.
●
Ball valves are fitted in water and gas connections, plus a drain point on all water connections.
TABLE 2
1 General
The instructions consist of three parts, Installation,
Servicing and Instructions for Use, which includes the
Guarantee Registration Card. The instructions are an
integral part of the appliance and must, to comply with
the current issue of the Gas Safety (Installation and Use)
Regulations, be handed to the user on completion
of installation.
Testing and Certification
This boiler is tested and certificated for safety and
performance. It is therefore important that no alteration
is made to the boiler, without permission, in writing,
from Hepworth Heating Ltd.
Any alteration not approved by Hepworth Heating Ltd.,
could invalidate the certification, boiler warranty and
may also infringe the current issue of the Statutory
Requirements, see Section 1.4.
CE Mark
This boiler meets the requirements of Statutory
Instrument No. 3083 The boiler (Efficiency)
Regulations, and therefore is deemed to meet the
requirements of Directive 92/42/EEC on the efficiency
requirements for new hot water boilers fired with liquid
or gaseous fuels.
Type test for purposes of Regulatioon 5 certified by:
Notified body 0087.
Product/production certified by:
Notified body 0087.
The CE mark on this appliance shows compliance with:
1. Directive 90/396/EEC on the approximation of the
laws of the Member States relating to appliances burning
gaseous fuels.
2. Directive 73/23/EEC on the harmonization of the
Laws of the Member States relating to the electrical
equipment designed for use within certain voltage limits.
3. Directive 89/336/EEC on the approximation of the
Laws of the Member States relating to
electromagnetic compatibility.
1.1 Installation
Materials and equipment should be fit for their purpose
and of suitable quality and workmanship.
1.2 Important Notice
This boiler is for use only on natural gas, G20.
1.3 Sheet Metal Parts
WARNING. When installing or servicing this boiler
care should be taken when handling the edges of sheet
metal parts to avoid any possibility of personal injury.
1.4 Requirements
The installation of this boiler must be carried out by a
competent person in accordance with the rules in force in
the countries of destination.
Manufacturer’s instructions, supplied.
Manufacturer’s instructions must not be taken as
overriding statutory requirements.
1.5 Data Label
The data label is on the inner case cover.
1.6 Data
See tables 1 and 2