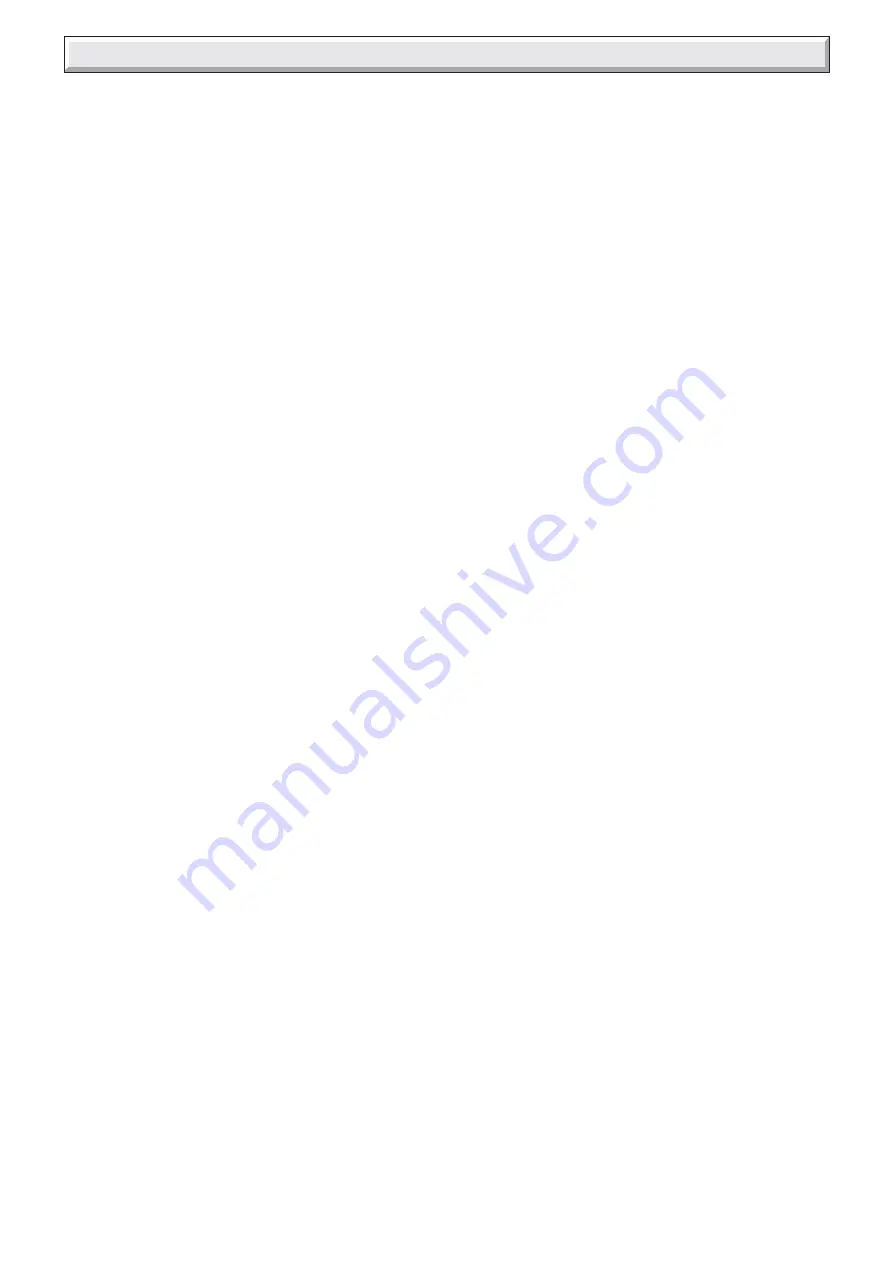
3
2000225013B
Important Information
Spare Parts
REMEMBER, When replacing a part on this appliance, use only
spare parts that you can be assured conform to the safety and
performance specification that we require. Do not use
reconditioned or copy parts that have not been clearly authorised
by Hepworth Heating Ltd.
Manual Handling Guidance
During the appliance installation and the replacement of the
heat exchanger it will be necessary to employ caution and
assistance whilst lifting as the appliance or component exceeds
the recommended weight for a one man lift.
In certain situations it may be required to use a mechanical
handling aid.
Take care to avoid trip hazards, slippery or wet surfaces.
Gas Leak or Fault
If a gas leak or fault exists or is suspected,
turn the boiler
mains electrical supply off and turn off the gas supply at the
meter.
Consult your local gas company or your local installation/
servicing company.
Electrical Supply Failure
The boiler must be earthed.
The boiler will not work without an electrical supply.
Normal opration of the boiler should resume when the electrical
supply is restored.
Reset any external controls, to resume normal operation of the
central heating.
If the boiler does not resume normal operation turn the mains
reset switch off and on. If the boiler does not resume normal
operation and an 'F9' fault code is indicated on the digital
display, the overheat stat may have operated. The overheat
stat would only operate under abnormal conditions and, under
these circumstances; it would be advisable to consult your
installation/servicing company.
Maintenance and Servicing
If this appliance is installed in a rented property there is a duty
of care imposed on the owner of the property by the current
issue of the Gas Safety (Installation and Use) Regulations,
Section 35.
Servicing/maintenance should be carried out by a competent
person in accordance with the rules in force in the countries of
destination.
To obtain service, please call your installer or Heatcall (Glow-
worm’s own service organisation) using the telephone number
on the front cover of this booklet.
Please be advised that the installation engineer on completion
of commissioning and servicing should complete the ‘Benchmark’
logbook.
All CORGI Registered Installers carry a CORGI ID card, and
have a registration number. Both should be recorded in your
boiler Logbook. You can check your installer is CORGI registered
by calling CORGI direct on: 01256 372300.
Boilers Installed in a Compartment or
Cupboard
If the boiler is fitted into a compartment or cupboard, it does not
require any ventilation openings. Do not use the compartment
or cupboard for storage.
Protection Against Freezing
The boiler has a built in frost protection programme as long as
the electricity and gas are left switched on.
This device operates the burner and system pump when the
temperature inside the boiler falls to 3
°
C.
Any other exposed areas of the system should be protected by
a separate frost thermostat.
If the mains electricity and gas are to be turned off for any long
periods during severe weather, it is recommended that the
whole system, including the boiler, should be drained to avoid
the risk of freezing. Make sure that, if fitted, the immersion
heater in the cylinder is switched off.
Contact your installation/servicing company as draining, refilling
and pressurising MUST be carried out by a competent person.
As a safety feature the boiler will stop working if the condensate
drain becomes blocked. During freezing conditions this may be
due to the forming of ice in the condense drain external to the
house. Release an ice blockage by the use of warm cloths on
the pipe. The boiler should then restart. Contact your installation/
servicing company if the fault persists.
Clearances
If fixtures are positioned close to the boiler, space must be left
as shown in diagram 2.1. Enough space must also be left in
front of the boiler to allow for servicing.
Boiler Casing
Do not remove or adjust the casing in any way, as incorrect
fitting may result in incorrect operation or failure to operate at all.
Pluming from flue terminal
Like all condensing boilers this appliance will produce a plume
of condensation from the flue terminal in cool weather. This is
due to the high efficiency and hence low flue gas temperature
of the boiler. It is normal and not a fault indication
Cleaning
This appliance contains metal parts and care should be taken
when handling and cleaning with particular regard to edges.
The boiler casing can be cleaned using a mild liquid detergent
with a damp cloth, then a dry cloth to polish.
Do not use any form of abrasive or solvent cleaner as you may
damage the paintwork.
Replacement Parts
If replacement parts are required contact Heatcall (Glow-worm’s
own service organisation) using the telephone number on the
front cover of this booklet.
Please quote the name of the appliance, this information will be
on the front of the appliance.
If in doubt seek advice from the local gas company or Heatcall.