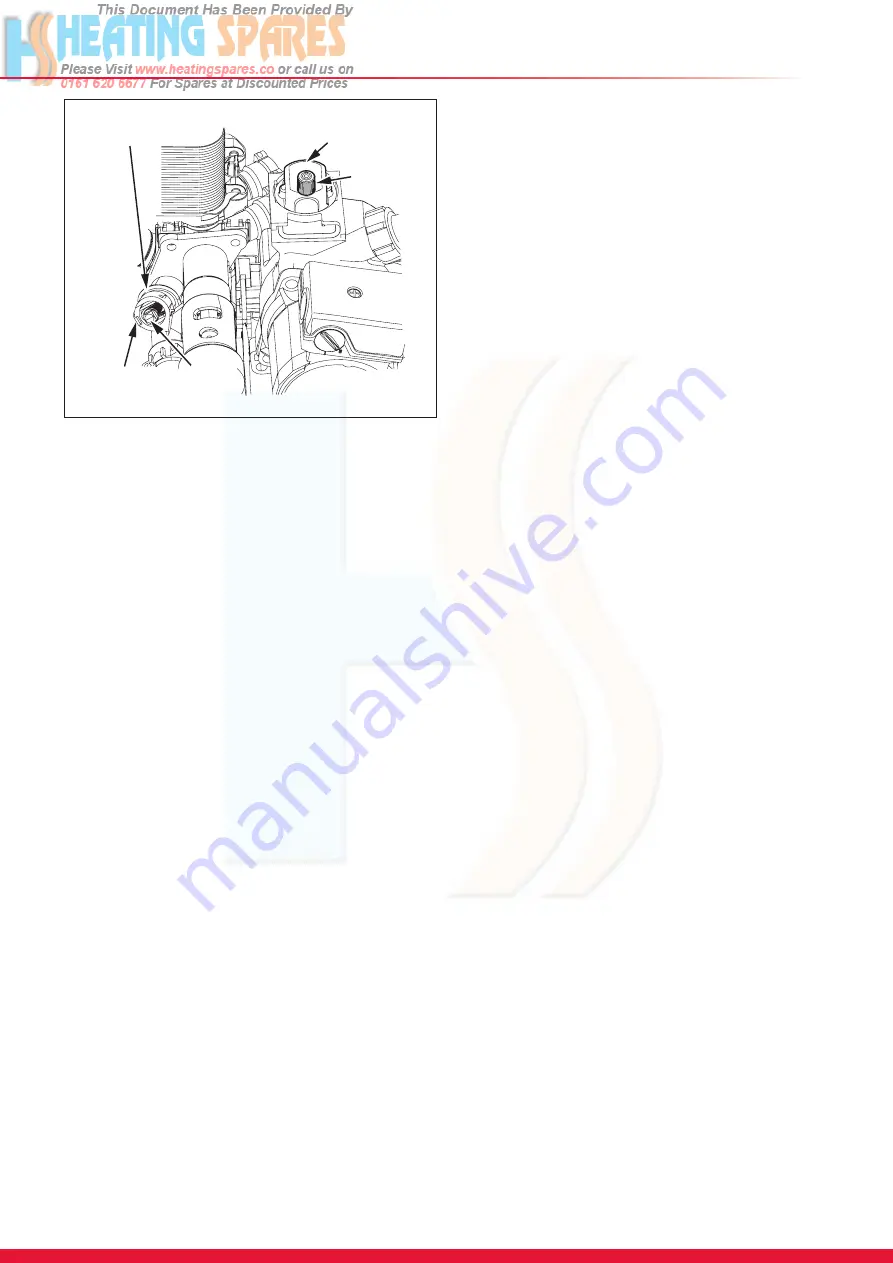
Supplied By www.heating spares.co Tel. 0161 620 6677
43
12.9 Completion
Fit the boiler module front panel, see diagram 8.2.
Fit the tank module front panel, this is a push-fit.
Ensure that the magnetic lighting instruction label is placed on
the surface of the boiler casing
GB:
It is a requirement that the “Benchmark” Installation,
Commissioning and Service Record is completed and left with
the user.
IE:
it is necessary to complete a “Declaration of Conformity” to
indicate compliance to I.S.813. An example of this is given in
the current edition of I.S.813.
12.10 Instruct the User
● Demonstrate, then instruct the User about the lighting
procedure and heating system controls operation.
● Advise that to ensure the continued efficient and safe
operation of the boiler it is recommended that it is checked
and serviced at regular intervals. The frequency of servicing
will depend upon the installation conditions and usage, but in
general, once a year should be enough.
● Draw attention, if applicable, to the current issue of the Gas
Safety (Installation and Use) Regulations, Section 35, which
imposes a duty of care on all persons who let out any property
containing a gas appliance in the UK.
● The user shall not interfere with or adjust sealed
components.
● It is the Law that any servicing is carried out by a competent
person approved at the time by the Health and Safety
Executive.
● Advise the user that, like all condensing boilers this
appliance will produce a plume of condensation from the flue
terminal in cool weather. This is due to the high efficiency and
hence low flue gas temperature of the boiler.
● Advise the user of the precautions necessary to prevent
damage to the system, boiler and the building, in the event of
the heating system being out of use during frost or freezing
conditions.
● Advise the user that the permanent mains electrical supply
SHOULD NOT be switched off, as the built in frost protection
and pump saver program will not operate.
12 Commissioning
● Advise the User if the mains electricity and gas are to be
turned off for any long periods during severe weather, it is
recommended that the whole system, including the boiler,
should be drained to avoid the risk of freezing.
Note: Sealed System: Contact your installation/servicing
company as draining, refilling and pressurising MUST be
carried out by a competent person approved at the time by the
Health and Safety Executive.
● Leave these instructions and the ‘Benchmark’ Installation,
Commissioning and Service Record with the user.
12.11 LPG CONVERSION
Do Not operate the boiler without water.
During the conversion to Propane use of a suitable flue gas
analyser is necessary.
Ensure that the appliance supply pressure = 37mbar.
(1) To access the gas valve you will need to remove the
silencer tube, see diagram 13.7 and section 13.4.
(2) Refer to diagram 13.13 and turn the gas valve throttle
fully clockwise using a small flat blade screwdriver.
(3) Turn the throttle back anti-clockwise by 2
1
/
4
turns.
(4) Ensure that the gas analyser is set to the correct fuel
setting - Propane.
(5) Attach combustion analyser to the combustion test
point. See diagram 13.1.
NOTE:
Before measuring combustion the silencer must
be replaced.
(6) Turn on the gas service isolation valve, see diagram
12.1.
Turn on the electrical supply, the appliance will begin the
ignition sequence.
Monitor the combustion reading and after 5 mins at max
rate, the reading should be:-
G31 - 10.2% ± 0.5 case on, 10.0% ± 0.5 case off after
5 minutes.
To achieve maximum rate (input) press the “reset”
button on the controls fascia, release and immediately
press and hold in the “+” button. After approximately 5
seconds “Hi” will be displayed.
Pressing the mode button when “Hi” is selected will
force the boiler to maximum rate, the display will flash
between “Hi” and the “default display” this will indicate
the boiler has been forced to maximum.
If adjustment proves necessary then proceed as follows:
Adjust the maximum rate CO
2
by turning the throttle
anti-clockwise to increase, clockwise to decrease, see
diagram 13.13.
NOTE:
Adjust only in very small increments (approx.
1
/
16
turn) and wait approx. 1 minute after each adjustment
until the value stabilises.
To exit the check sequences press the “+” button, this
will reset the boiler to the default display.
(7) Remove analyser probe from the test point and replace
the cap.
(8)
IMPORTANT: Fit the LPG conversion label supplied
in the documentation pack to the base panel
alongside the data label. Ensure the silencer is fitted
and front panel replaced.
AUTOMATIC
AIR VENT
AUTOMATIC
BYPASS
BYPASS
SCREW
RETAINING
CLIP
CAP
15346
Diagram 12.5
Содержание 100sxi
Страница 8: ...Supplied By www heating spares co Tel 0161 620 6677 8 1 Boiler Specifications 13247 Diagram 1 1 ...
Страница 9: ...Supplied By www heating spares co Tel 0161 620 6677 9 Diagram 1 2 13290 1 Boiler Specifications ...
Страница 52: ...Supplied By www heating spares co Tel 0161 620 6677 52 14 Fault Finding 13412 Diagram 14 4 Fault Codes ...
Страница 70: ...Supplied By www heating spares co Tel 0161 620 6677 70 17 Declaration of Conformity ...
Страница 71: ...Supplied By www heating spares co Tel 0161 620 6677 71 Notes ...