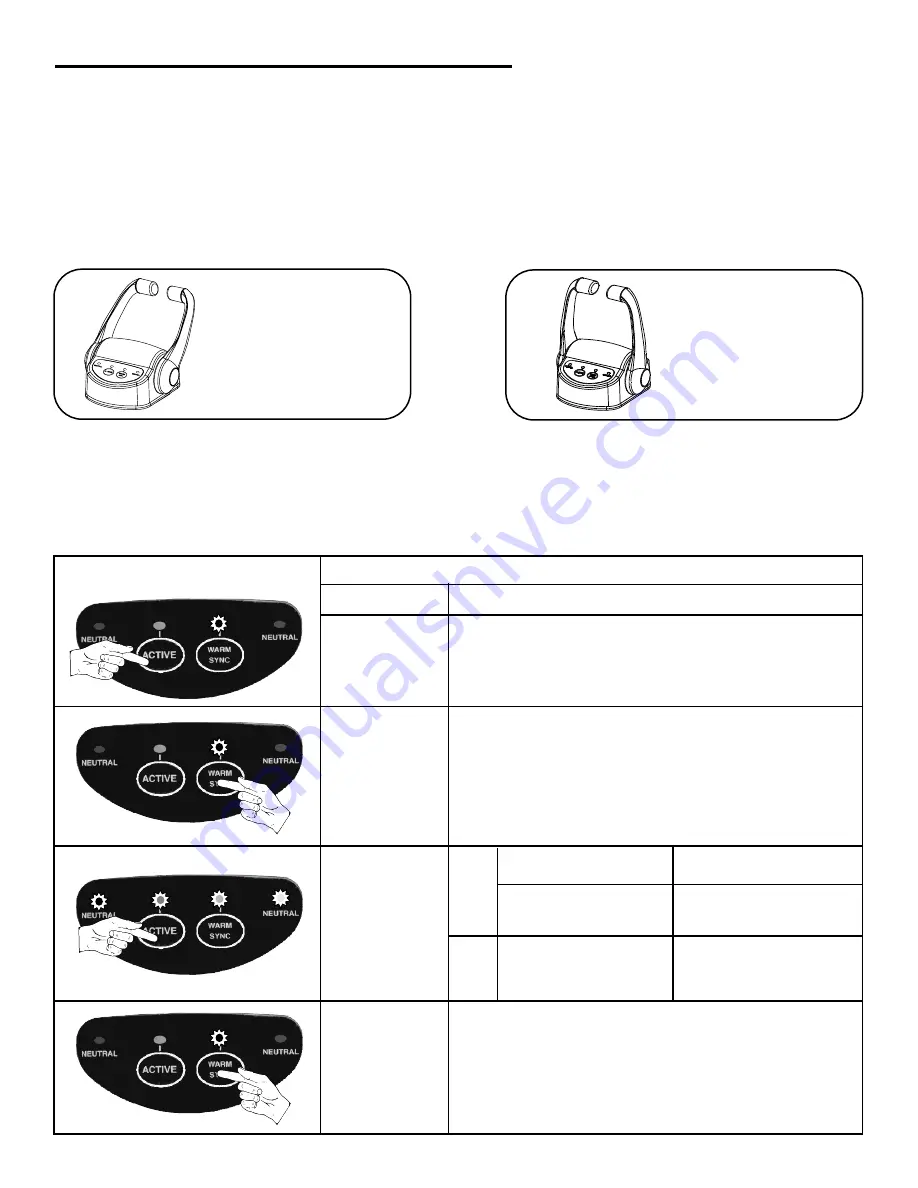
31
Section 2.0 — Appendix / Reference
OR
Station Transfer Options
The Station Transfer Option allows you to configure the EEC system to transfer station control under-
way above idle or with handles at the Neutral position only.
Press ACTIVE
9 times for
Station
Transfer Option
PORT Neutral & STBD Neutral LEDs will
begin to flash
Press
WARM to
activate
selection
NO LEDs will be illuminated
Press
WARM to
save option
selection
You may continue to other configuration options
on the following pages or you may choose to
EXIT CONFIGURATION MODE by turning
system OFF, moving control handles back to
NEUTRAL, and then turn system ON again.
Press &
Release
ACTIVE
to cycle
through Station
Transfer
Options
1
2
ACTION
LEDs ON
OPTION
None
Underway Transfer
(Default)
Port Neutral
Transfer At Neutral
Position only
RESULT
Choose “underway transfer” when you want
to transfer control when handles are in appropriate
position—not limited to Neutral gear only
(Default)
Choose “Neutral transfer” when you want to transfer
control when handles are in Neutral only
Inactive Station “taking
control” must be at Neutral
position in order to transfer
control from Active Station
Inactive Station “taking
control” must have control
handles at Neutral or in the
same gear at same or lower
speed as Active Station
To Change Station Transfer Setting Follow These Steps:
NOTE: Active Station can be at any handle position during station transfer
Enter Configuration Mode as described in section 2.4A (pg. 29)
Содержание EEC4
Страница 20: ...EEC4 Installation Manual 16...
Страница 26: ...EEC4 Installation Manual 22...
Страница 27: ...23 Section 2 0 Appendix Reference 3 25 Cutout Template for Control Head Top Mount...
Страница 28: ...EEC4 Installation Manual 24...