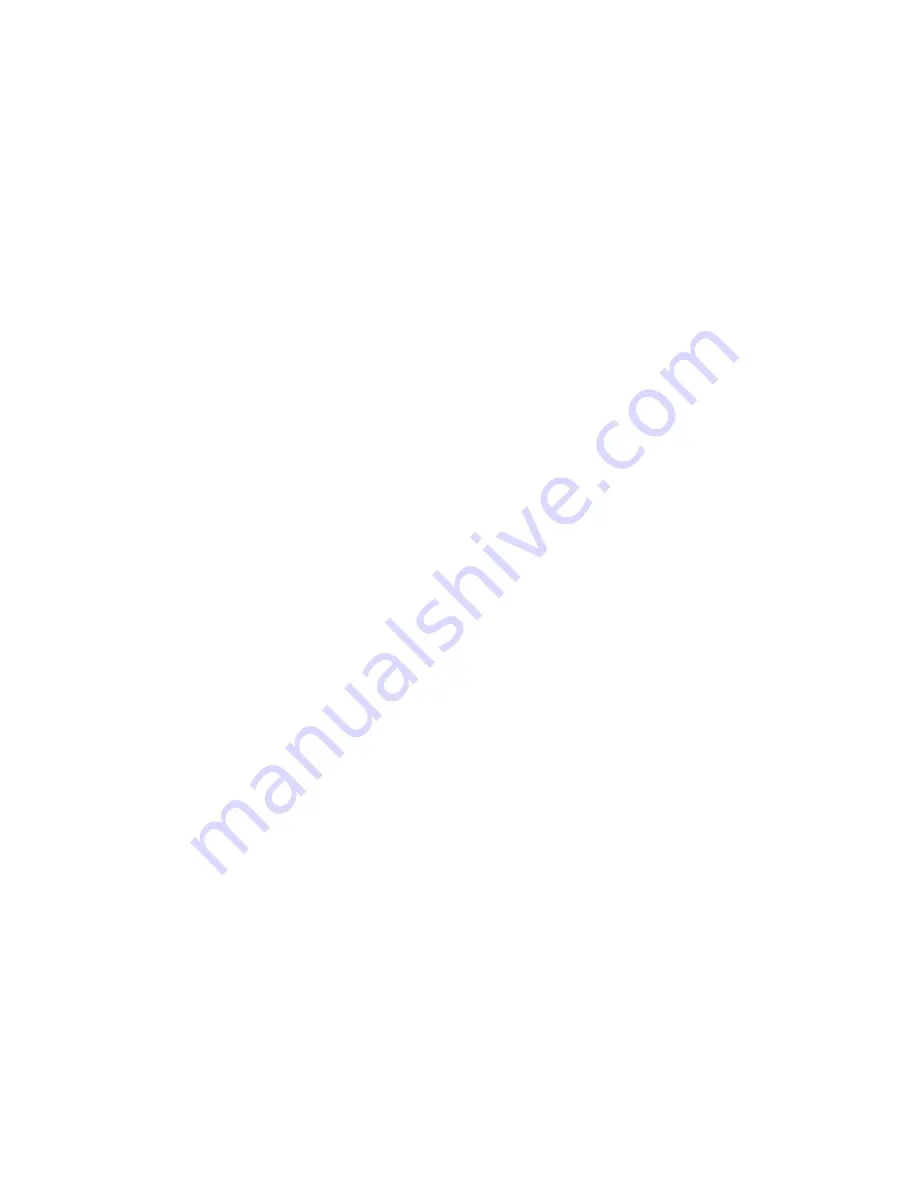
© AGCO Corporation, 2008 All rights reserved.
Part Number 79032998 A Rev. (English)
Printed in U.S.A.
August 2008
Gleaner
®
A66 / A76
Rotary Combine
SERVICE MANUAL
79032998 A Rev.
CONTENTS
GENERAL INFORMATION ....................................................................................................................................01
SPECIFICATIONS ..................................................................................................................................................02
ENGINE WORKSHOP MANUAL ........................................................................................................................ 03A
ENGINE - DRIVES, COOLING AND FUEL......................................................................................................... 03B
MATERIAL HANDLING..........................................................................................................................................04
MATERIAL DISCHARGE .......................................................................................................................................05
REAR AXLE ...........................................................................................................................................................06
THRESHING AND SEPARATING..........................................................................................................................07
FRONT AXLE .........................................................................................................................................................08
HYDRAULICS..................................................................................................................................................................... 09
ELECTRICAL...................................................................................................................................................................... 10
ELECTRONICS................................................................................................................................................................... 11
CAB AND HVAC ................................................................................................................................................................. 12
GRAIN HEADER................................................................................................................................................................. 13
CORN HEADER.................................................................................................................................................................. 14
RESERVED......................................................................................................................................................................... 15