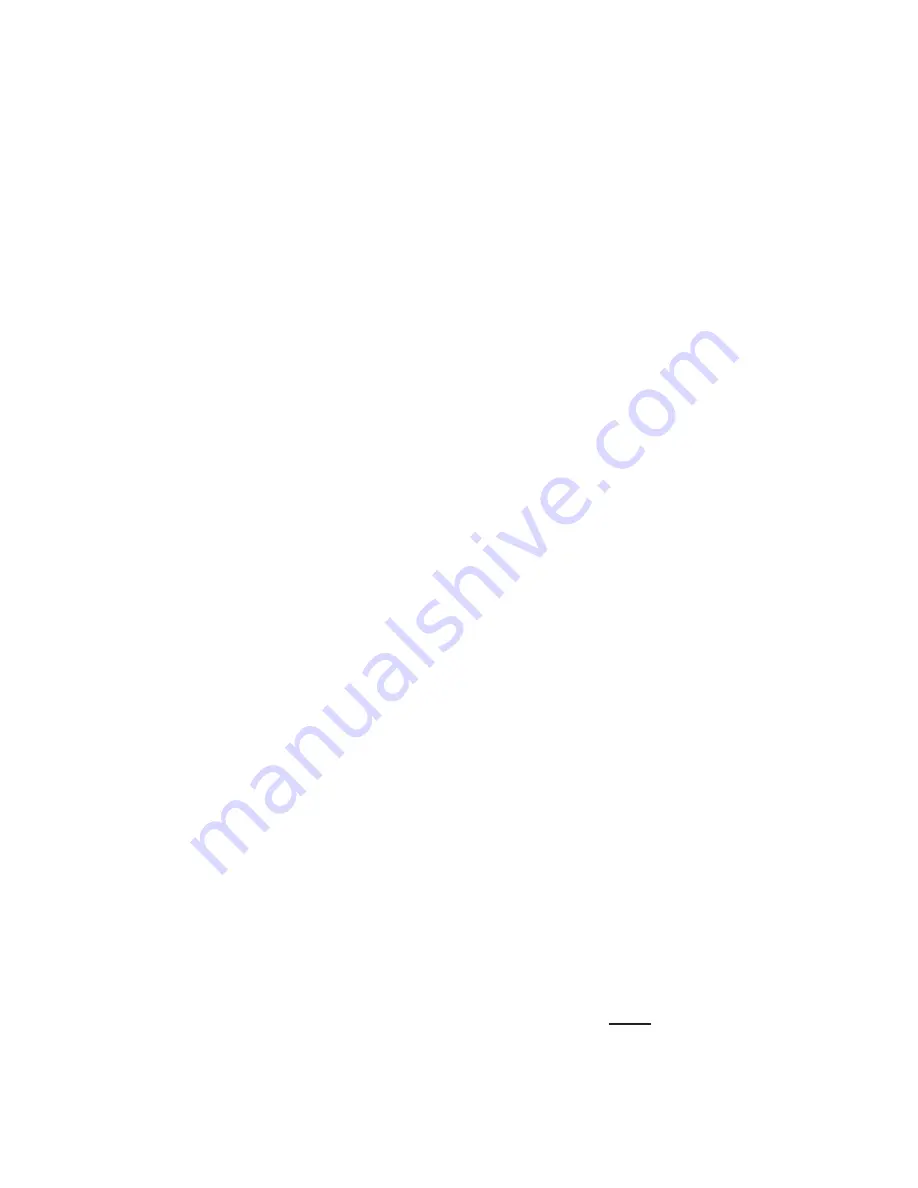
10
Mounting Valve Casing:
Press seal cases (38) (with the stepped OD diameter 65mm) carefully to its stop in the centering holes of the
intermediate casing. Mount fl at leakage seal (62D).
Important!
The fl at leakage seal (62D) must be positioned with its 3mm diameter bore onto the notched pin
(62C) on the intermediate casing. The leakage return bores in the intermediate casing and in the seal sleeves
must remain clear of the cutouts in the seal (62D). Push valve casing (50) together with intermediate casing
(62) carefully on to the centering studs (50A). Tighten hexagon nuts evenly and crosswise to 265 Ft-lbs. (360
NM).
Important!
The torque tension on the screws (49A) must be checked after 8-10 operating hours; the pump
must be at zero pressure. Thereafter the tension is to be checked every 200 operating hours.
To Dismantle Reduction Gear
Take out plungers and seal sleeves (as described above). Drain oil by taking off plug (12). After removing
the clip ring (33B), pry out the seal retainer (33) with a screwdriver. Open hose adapter (K11). Remove gear
cover (K3) and remove the cooling vane plate (K1) by removing the screws (K4). Remove connecting rod
screws (24).
Important!
Connecting rods are marked for identifi cation. Do not twist connecing rod halves or interchange
them. When reassembling, the connecting rods must be fi tted in their exact original position on the crank-
shaft journals. Push connecting rod halves together with the crosshead as far as possible into the crosshead
guide. Remove bearing cover (14), remove shims (21A/B).
To Dismantle Reduction Gear
Remove screws (67). Press off gear cover (66) by screwing two screws into both thread bores. Remove
screw (72) and take off fi tting disc (69). Remove the cogwheel from the shaft with a bearing puller tool. Using
a rubber hammer, tap out the crankshaft towards bearing cover (14). Check surfaces on the connecting rods
(24), crankshaft (22), and crossheads (25). Check the surfaces of the crosshead guides in the crankcase for
any unevenness.
Reassemble in reverse order. Thread the crankshaft in from the bearing cover side until the bearing rests
cleanly in the outer ring on fl ange (19).
Press in the outer ring from bearing (20) and use shims (21A/B), adjust the bearing to be free of play. To
achieve this, add shims, screw on cover (14) and turn the crankshaft until it can no longer be turned by hand.
Then remove a shim and establish whether the crankshaft can now be turned. A crankshaft that can be too
easily turned may cause damage to the bearings and connecting rods due to axial movements in the conical
bearing shells. Mount connecting rod halves in their exact original position and tighten at 37 Ft.-Lbs. (50 NM).
Important!
Connecting rods must be able to move slightly sideways on the stroke journals.
To Mount Reduction Gear
Before pressing the ball bearings (75 and 74) onto the pinion, heat them up. Press the cogwheel slightly on to
the crankshaft so that the pinion (69) together with the bearing (74) can still be inserted.
Move the pinion (69) against the cogwheel and make them mate perfectly when mounting. Then carefully tap
the cogwheel and the pinion simultaneously on to the crankshaft and into the bearing seat.
Fit fi tting disc (69), and secure screw (72) with Loctite. Fit the seal (76) on to the cylindrical pins (68). Care-
fully push the gear cover (66) onto the bearing (75). Make sure that the radial shaft seal (73) does not be-
come damaged during fi tting on to the pinion shaft.
With their respective seals (K2), mount cooling plate (K1) and gear cover (K3). When assembling the cooling
circuit line, make sure that the oil cooler connection (K7) is always joined to the upper connection (K3) of the
gear cover.
Important!
Before putting in to operation again, turn the reduction gear shaft per hand at least four full turns
to make sure the gear is correctly aligned.
GP8135 and GP8140 Pump Repair Instructions