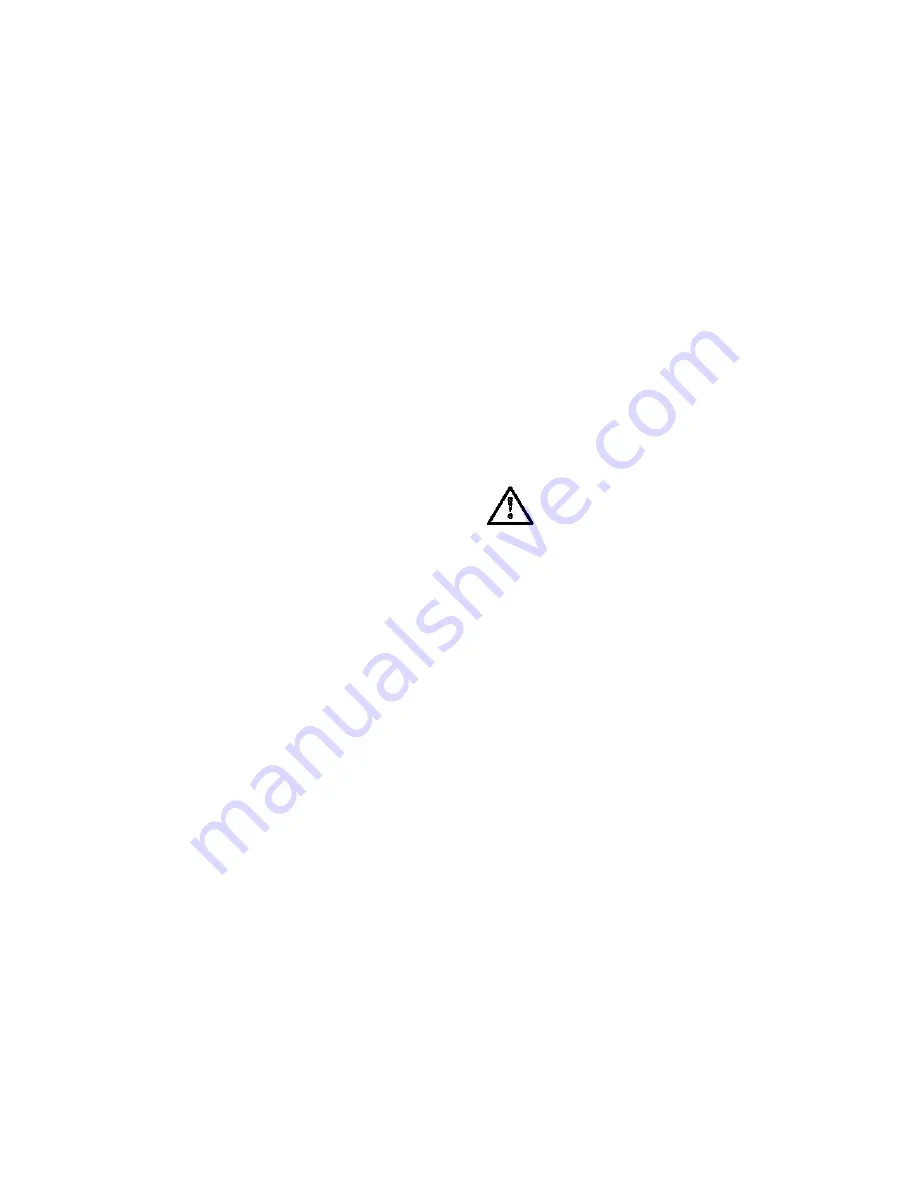
2
The stated figures are for maximum pressure and maximum
speed (rpm) and apply for interval operation with cold water.
Required NPSH refers to water (specific weight 1kg/dm
3
,
viscosity 1°E) at maximum permissible pump revolutions.
Fluid medium: Clean water filtered to 50µm.
Operation and Maintenance
Check oil level prior to starting and ensure trouble-free water
supply.
IMPORTANT!
If there is a danger of frost, the water in the
pump and in the pump fittings (particularly the unloader valve)
must be emptied. The second discharge port can also be
used and the pump run “dry” for 1-2 minutes for this purpose.
Oil: Use only 3.3 gallons (12.5 liters) of Giant Oil (p/n 01154)
or ISO VG 220 GL4 (e.g. Aral Degol BG220) or SAE 90 GL4
gear oil. Initial change after 50 operating hours and then every
1000 operating hours or after one year of operation.
IMPORTANT!
when operating in damp places or with high
temperature fluctuations. Oil must be changed immediately
should condensate (frothy oil) occur in the gear box.
NPSH values must be observed
Cooling the Gear Oil
IMPORTANT!
When using the integrated cooling system for
cooling the gear oil, the water inlet pressure must not exceed
29 PSI (2 bar).
If a separate cooling circuit is installed, it is then possible to
have an inlet pressure up to a maximum of 145 PSI (10 bar)
on the inlet side.
Make sure that suction pulsation is sufficiently dampened –
water column resonance must be avoided.
IMPORTANT!
The pumps can be run without gear oil cooling
in continuous operation
up to
a power rating of
107 hp (80
kW)
or with major intermittent operation at full performance
(see below regarding the definition for intermittent operation).
If operational power exceeds
107 hp (80 kW)
or if continuous
operation is the case, the pump must be run with the inte
-
grated oil cooling system.
Definition of intermittent operation:
operation at full per
-
formance for not more than 20 minutes in any given hour. In
between the pump is running without pressure or turned off.
For example, this can be full load operation for 5 minutes four
times an hour with 10 minute breaks in between or continu-
ous full load operation for 20 minutes followed by a 40 minute
break.
The maximum temperature of the water being pumped and
which is also fed through the cooling system must not exceed
86 °F (30 °C). The water amount which is fed into the cooling
system depends on the pump speed and is approximately
1.85 gpm (7.0 l/min.) at 580 pump rpm. The cooling water
is sucked in by one of the pumping chambers and pumped
away.
IMPORTANT!
If higher medium temperatures or liquids
other than water are involved or aggressive media such as
seawater, demineralised water etc., the pump must be fitted
with a separate cooling circuit. The separate cooler must have
a cooling efficiency of 1700 watt. If there is a danger of frost,
an appropriate amount of antifreeze must be mixed into the
cooling circuit.
When starting up for work, the pump must run first at zero
pressure for approximately 1 minute.
IMPORTANT!
The GP8000 series has a black arrow on the
crankcase which shows the preferred direction of rotation.
The preferred direction of rotation ensures oil is splashed onto
the crosshead guides in the correct manner via the motion of
the connecting rods – which is a particular advantage where
INSTALLATION INSTRUCTIONS
continuous operation is involved.
The pump can also be run against the recommended direction
of rotation if operated periodically or at reduced pressure. If
so, the pump must be run in in this direction to smoothen the
bearing areas. This is done by initially operating the pump
at zero pressure for 30 minutes; thereafter the pressure is to
be slowly increased over a period of an hour to the desired
maximum operating pressure. Check the oil temperature dur
-
ing this process.
IMPORTANT!
If there is a danger of frost, the pump and cool
-
ing system must be emptied. Note that travel wind can cause
water in pumps fitted on open vehicles to freeze even if the
outside temperature is above freezing point.
To empty the cooling circuit, remove the L-joints (K11) on the
pump head (50). Blow out the circuit liquid at the joint connec-
tion (K11/K7) using compressed air.
The torque tension on the valve casing nuts (49A) is to be
checked after approximately 200 operating hours. Please see
page 8 for torque specifications.
When checking the torque tension, the pump must be at zero
pressure.
IMPORTANT!
The service life of the seals is maximized if a
minimal amount of leakage is present. A few drops of water
can drip from each plunger every minute. Leakage has to
be examined every day; the plunger seals must be changed
should leakage become excessive i.e. constant dripping.
Safety Rules
The operating instructions must be read and adhered to
before performing any work on the pump or complete
assembled unit. No responsibility will be carried by us
for damage to materials or persons caused by improper
handling of our pumps.
Access to the pump is not allowed for unauthorized person-
nel. A safety valve is to be installed in accordance with the
guidelines for liquid spraying units so that the admissible
operating pressure cannot be ex- ceeded by more than 10%.
Pump operation without a safety valve as well as any excess
in temperature or speed limits automatically voids the war
-
ranty.
When the pump is in operation, the driven shaft side and its
coupling must be covered by a protective guard. The plunger
area must also be covered by the protective plate (30).
Do not step onto the protective plate (30) or put weight on it.
Pressure in the discharge line and pump must be at zero
before carrying out any maintenance work to the pump or unit.
Close off suction line. Disconnect fuses to ensure that the
driving motor cannot be accidentally switched on. Make sure
that the pump, the cooling system and all parts on the pres
-
sure side of the unit are vented and refilled, with pressure at
zero, before starting the pump.
In order to prevent air or an air/water-mixture being absorbed
and cavitation occurring, the pump npshr (net positive suction
head required) and water temperature must be respected.
Cavitation and/or compression of gases lead to uncon
-
trollable pressure-kicks which can ruin the pump and unit
parts and also be dangerous to the operator or anyone
standing nearby.
Giant plunger pumps are suitable for pumping clean water
and other non-aggressive or non-abrasive media with a spe-
cific weight similar to water.
Before pumping other liquids - especially inflammable,
explosive and toxic media - the pump manufacturer must
be consulted with regard to the resistance of the pump
material. It is the responsibility of the equipment manu
-
facturer and/or operator to ensure that all pertinent safety
regulations are followed.