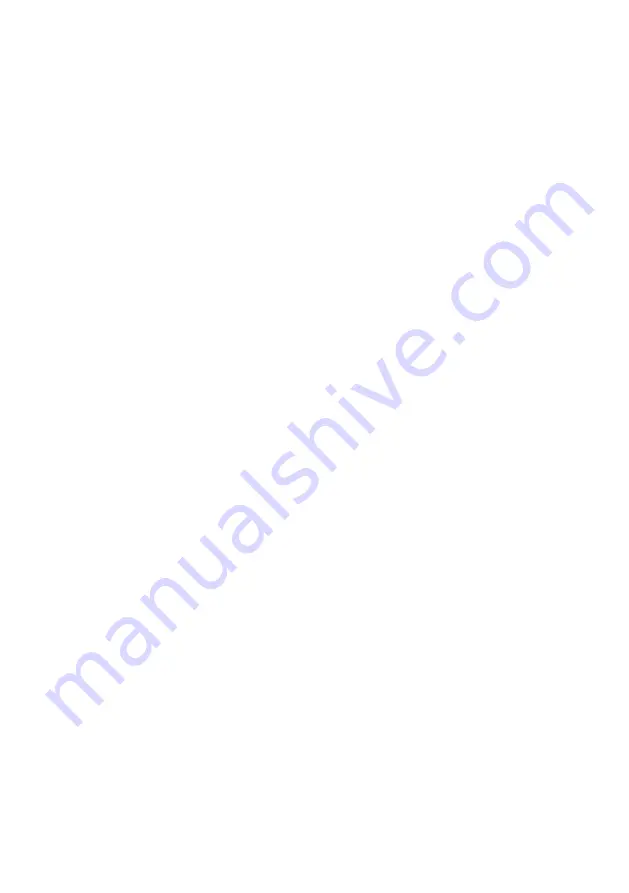
16
Removing and cleaning the strainer
To remove and, if required, clean or replace the
strainer proceed as follows:
Use a 30 mm open-end spanner (US: wrench) to
unscrew the sealing plug from the body.
Remove the gasket.
Take out the strainer.
Clean the sealing plug, the gasket and the
strainer with fresh water and a clean lint-free
cloth.
Clean gasket seating surfaces.
Checking the component parts for damage
Check the removed parts for visible signs of
wear or damage.
Discard and replace any damaged part.
Mounting the strainer
To remove the strainer proceed as follows:
Apply heat-resistant lubricant to the thread of
the sealing plug.
If the gasket is damaged replace it with a new
one.
Put the gasket onto the sealing plug.
Insert the strainer into the sealing plug.
Use a 30 mm open-end spanner (US: wrench) to
screw the sealing plug into the body and tighten
with a torque of 75 Nm.
Содержание RHOMBUSline MK 45 A-1
Страница 1: ...Steam Trap MK 45 1 MK 45 2 MK 45 A 1 MK 45 A 2 Original Installation Instructions 810348 12 ...
Страница 26: ...26 ...
Страница 27: ...27 ...