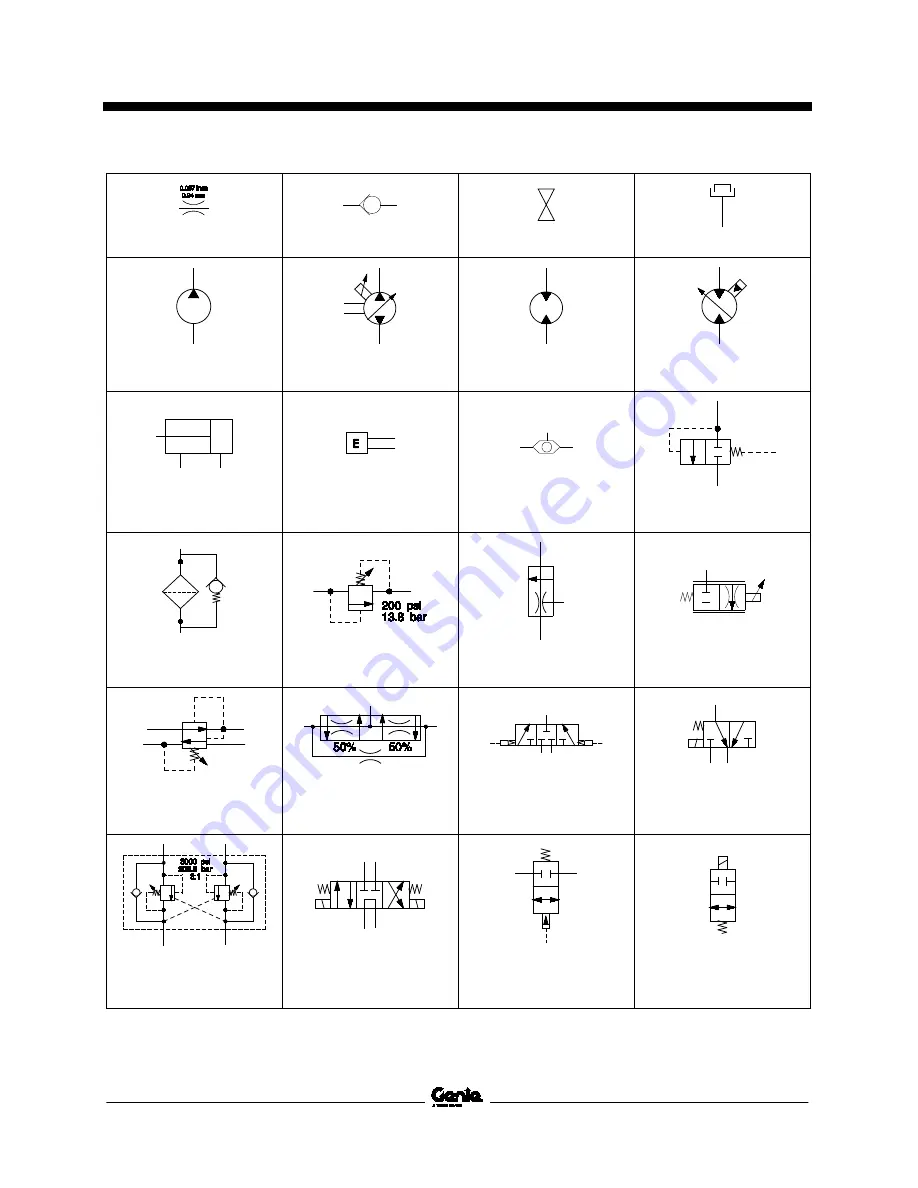
October 2016
Service and Repair Manual
Hydraulic Symbols Legend
Part No. 1269074
S-80 • S-85 • S-80X
121
Orifice with size
Check valve
Shut off valve
Brake
Pump, fixed displacement
Pump, bi-directional
variable displacement
Motor, bi-directional
Motor, 2 speed
bi-directional
Cylinder, double acting
Pump, prime mover (engine
or motor)
Shuttle valve. 2 position,
3 way
Differential sensing valve
Filter with bypass relief
valve
Relief valve with pressure
setting
Priority flow regulator
Solenoid operated
proportional valve
Pressure reducing valve
Flow divider/combiner valve
Pilot operated 3 position,
3 way shuttle valve
Solenoid operated
2 position, 3 way directional
valve
Counterbalance valve with
pressure and pilot ratio
Solenoid operated
3 position 4 way directional
valve
Pilot operated 2 position,
2 way directional valve
2 position, 2 way solenoid
valve
Содержание S-80
Страница 16: ......
Страница 76: ...Service and Repair Manual October 2016 Manifolds 60 S 80 S 85 S 80X Part No 1269074 ...
Страница 86: ...Service and Repair Manual October 2016 Manifolds 70 S 80 S 85 S 80X Part No 1269074 ...
Страница 144: ...Service and Repair Manual October 2016 128 Continental TME27 Engine Harness ...
Страница 145: ...October 2016 Service and Repair Manual Part No 1269074 S 80 S 85 S 80X 129 Continental TME27 Engine Harness ...
Страница 147: ...October 2016 Service and Repair Manual 131 S 80X Ground Control Box Wiring Diagram ...
Страница 148: ...Service and Repair Manual October 2016 132 Deutz TD2 9 L4 Engine Harness ...
Страница 149: ...October 2016 Service and Repair Manual Part No 1269074 S 80 S 85 S 80X 133 Deutz TD2 9 L4 Engine Harness ...
Страница 150: ...Service and Repair Manual October 2016 134 S 80 S 85 S 80X Part No 1269074 Perkins 404F 22T Engine Harness ...
Страница 151: ...October 2016 Service and Repair Manual 135 Perkins 404F 22T Engine Harness ...
Страница 152: ...Service and Repair Manual October 2016 136 Electrical Schematic S 80X Deutz TD2 9 L4 Models ANSI CSA ...
Страница 155: ...October 2016 Service and Repair Manual 139 Electrical Schematic S 80X Deutz TD2 9 L4 Models ANSI CSA ...
Страница 156: ...Service and Repair Manual October 2016 140 Ground Control Box S 80X Deutz TD2 9 L4 Models ANSI CSA ...
Страница 160: ...Service and Repair Manual October 2016 144 Platform Control Box S 80X Deutz TD2 9 L4 Models ANSI CSA ...
Страница 161: ...October 2016 Service and Repair Manual 145 Electrical Schematic S 80X Deutz TD2011L04i Models ANSI CSA ...
Страница 164: ...Service and Repair Manual October 2016 148 Electrical Schematic S 80X Deutz TD2011L04i Models ANSI CSA ...
Страница 165: ...October 2016 Service and Repair Manual 149 Ground Control Box S 80X Deutz TD2011L04i Models ANSI CSA ...
Страница 168: ...Service and Repair Manual October 2016 152 Platform Control Box S 80X Deutz TD2011L04i Models ANSI CSA ...
Страница 169: ...October 2016 Service and Repair Manual 153 Electrical Schematic S 80X Perkins 404F 22T Models ANSI CSA ...
Страница 172: ...Service and Repair Manual October 2016 156 Electrical Schematic S 80X Perkins 404F 22T Models ANSI CSA ...
Страница 173: ...October 2016 Service and Repair Manual 157 Ground Control Box S 80X Perkins 404F 22T Models ANSI CSA ...
Страница 176: ...Service and Repair Manual October 2016 160 Platform Control Box S 80X Perkins 404F 22T Models ANSI CSA ...
Страница 177: ...October 2016 Service and Repair Manual 161 Electrical Schematic S 80X Perkins 804D 33 Models ANSI CSA ...
Страница 180: ...Service and Repair Manual October 2016 164 Electrical Schematic S 80X Perkins 804D 33 Models ANSI CSA ...
Страница 181: ...October 2016 Service and Repair Manual 165 Ground Control Box S 80X Perkins 804D 33 Models ANSI CSA ...
Страница 184: ...Service and Repair Manual October 2016 168 Platform Control Box S 80X Perkins 804D 33 Models ANSI CSA ...
Страница 185: ...October 2016 Service and Repair Manual 169 Electrical Schematic S 80X Continental TME27 Models ANSI CSA ...
Страница 188: ...Service and Repair Manual October 2016 172 Electrical Schematic S 80X Continental TME27 Models ANSI CSA ...
Страница 189: ...October 2016 Service and Repair Manual 173 Ground Control Box S 80X Continental TME27 Models ANSI CSA ...
Страница 192: ...Service and Repair Manual October 2016 176 Platform Control Box S 80X Continental TME27 Models ANSI CSA ...
Страница 193: ...October 2016 Service and Repair Manual 177 Electrical Schematic S 80 S 85 Deutz TD2 9 L4 Models ANSI CSA ...
Страница 196: ...Service and Repair Manual October 2016 180 Electrical Schematic S 80 S 85 Deutz TD2 9 L4 Models ANSI CSA ...
Страница 197: ...October 2016 Service and Repair Manual 181 Ground Control Box S 80 S 85 Deutz TD2 9 L4 Models ANSI CSA ...
Страница 200: ...Service and Repair Manual October 2016 184 Platform Control Box S 80 S 85 Deutz TD2 9 L4 Models ANSI CSA ...
Страница 201: ...October 2016 Service and Repair Manual 185 Electrical Schematic S 80 S 85 Deutz TD2011L04i Models ANSI CSA ...
Страница 204: ...Service and Repair Manual October 2016 188 Electrical Schematic S 80 S 85 Deutz TD2011L04i Models ANSI CSA ...
Страница 205: ...October 2016 Service and Repair Manual 189 Ground Control Box S 80 S 85 Deutz TD2011L04i Models ANSI CSA ...
Страница 208: ...Service and Repair Manual October 2016 192 Platform Control Box S 80 S 85 Deutz TD2011L04i Models ANSI CSA ...
Страница 209: ...October 2016 Service and Repair Manual 193 Electrical Schematic S 80 S 85 Perkins 404F 22T Models ANSI CSA ...
Страница 212: ...Service and Repair Manual October 2016 196 Electrical Schematic S 80 S 85 Perkins 404F 22T Models ANSI CSA ...
Страница 213: ...October 2016 Service and Repair Manual 197 Ground Control Box S 80 S 85 Perkins 404F 22T Models ANSI CSA ...
Страница 216: ...Service and Repair Manual October 2016 200 Platform Control Box S 80X Perkins 404F 22T Models ANSI CSA ...
Страница 217: ...October 2016 Service and Repair Manual 201 Electrical Schematic S 80 S 85 Perkins 804D 33 Models ANSI CSA ...
Страница 220: ...Service and Repair Manual October 2016 204 Electrical Schematic S 80 S 85 Perkins 804D 33 Models ANSI CSA ...
Страница 221: ...October 2016 Service and Repair Manual 205 Ground Control Box S 80 S 85 Perkins 804D 33 Models ANSI CSA ...
Страница 224: ...Service and Repair Manual October 2016 208 Platform Control Box S 80 S 85 Perkins 804D 33 Models ANSI CSA ...
Страница 225: ...October 2016 Service and Repair Manual 209 Electrical Schematic S 80 S 85 Continental TME27 Models ANSI CSA ...
Страница 228: ...Service and Repair Manual October 2016 212 Electrical Schematic S 80 S 85 Continental TME27 Models ANSI CSA ...
Страница 229: ...October 2016 Service and Repair Manual 213 Ground Control Box S 80 S 85 Continental TME27 Models ANSI CSA ...
Страница 232: ...Service and Repair Manual October 2016 216 Platform Control Box S 80 S 85 Continental TME27 Models ANSI CSA ...
Страница 233: ...October 2016 Service and Repair Manual 217 Electrical Schematic S 80 S 85 Deutz TD2 9 L4 Models CE ...
Страница 236: ...Service and Repair Manual October 2016 220 Electrical Schematic S 80 S 85 Deutz TD2 9 L4 Models CE ...
Страница 237: ...October 2016 Service and Repair Manual 221 Ground Control Box S 80 S 85 Deutz TD2011L04i Models CE ...
Страница 240: ...Service and Repair Manual October 2016 224 Platform Control Box S 80 S 85 Deutz TD2011L04i Models CE ...
Страница 241: ...October 2016 Service and Repair Manual 225 Electrical Schematic S 80 S 85 Deutz TD2011L04i Models CE ...
Страница 244: ...Service and Repair Manual October 2016 228 Electrical Schematic S 80 S 85 Deutz TD2011L04i Models CE ...
Страница 245: ...October 2016 Service and Repair Manual 229 Ground Control Box S 80 S 85 Deutz TD2011L04i Models CE ...
Страница 248: ...Service and Repair Manual October 2016 232 Platform Control Box S 80 S 85 Deutz TD2011L04i Models CE ...
Страница 249: ...October 2016 Service and Repair Manual 233 Electrical Schematic S 80 S 85 Perkins 804D 33 Models CE ...
Страница 252: ...Service and Repair Manual October 2016 236 Electrical Schematic S 80 S 85 Perkins 804D 33 Models CE ...
Страница 253: ...October 2016 Service and Repair Manual 237 Ground Control Box S 80 S 85 Perkins 804D 33 Models CE ...
Страница 256: ...Service and Repair Manual October 2016 240 Platform Control Box S 80 S 85 Perkins 804D 33 Models CE ...
Страница 257: ...October 2016 Service and Repair Manual 241 Electrical Schematic S 80 S 85 Continental TME27 Models CE ...
Страница 260: ...Service and Repair Manual October 2016 244 Electrical Schematic S 80 S 85 Continental TME27 Models CE ...
Страница 261: ...October 2016 Service and Repair Manual 245 Ground Control Box S 80 S 85 Continental TME27 Models CE ...
Страница 264: ...Service and Repair Manual October 2016 248 Platform Control Box S 80 S 85 Continental TME27 Models CE ...
Страница 265: ...October 2016 Service and Repair Manual 249 Electrical Schematic S 80 S 85 Deutz TD2011L04i Models AS ...
Страница 268: ...Service and Repair Manual October 2016 252 Electrical Schematic S 80 S 85 Deutz TD2011L04i Models AS ...
Страница 269: ...October 2016 Service and Repair Manual 253 Ground Control Box S 80 S 85 Deutz TD2011L04i Models AS ...
Страница 272: ...Service and Repair Manual October 2016 256 Platform Control Box S 80 S 85 Deutz TD2011L04i Models AS ...
Страница 273: ...October 2016 Service and Repair Manual 257 Electrical Schematic S 80 S 85 Perkins 804D 33 Models AS ...
Страница 276: ...Service and Repair Manual October 2016 260 Electrical Schematic S 80 S 85 Perkins 804D 33 Models AS ...
Страница 277: ...October 2016 Service and Repair Manual 261 Ground Control Box S 80 S 85 Perkins 804D 33 Models AS ...
Страница 280: ...Service and Repair Manual October 2016 264 Platform Control Box S 80 S 85 Perkins 804D 33 Models AS ...
Страница 281: ...October 2016 Service and Repair Manual 265 Electrical Schematic S 80 S 85 Continental TME27 Models AS ...
Страница 284: ...Service and Repair Manual October 2016 268 Electrical Schematic S 80 S 85 Continental TME27 Models AS ...
Страница 285: ...October 2016 Service and Repair Manual 269 Ground Control Box S 80 S 85 Continental TME27 Models AS ...
Страница 288: ...Service and Repair Manual October 2016 272 Platform Control Box S 80 S 85 Continental TME27 Models AS ...
Страница 289: ...October 2016 Service and Repair Manual 273 Continental Options Schematic ...
Страница 292: ...Service and Repair Manual October 2016 276 Deutz and Perkins Options Schematic ...
Страница 293: ...October 2016 Service and Repair Manual 277 Platform Level Cutout CTE Option ...
Страница 296: ...Service and Repair Manual October 2016 280 12 kW Hydraulic Generator Wiring Diagram ...
Страница 297: ...October 2016 Service and Repair Manual 281 12 kW Hydraulic Generator Electrical Schematic ...
Страница 300: ...Service and Repair Manual October 2016 284 Belt Driven Generator Option ...
Страница 301: ...October 2016 Service and Repair Manual 285 Hydraulic Schematic 2WD Models ...
Страница 305: ......