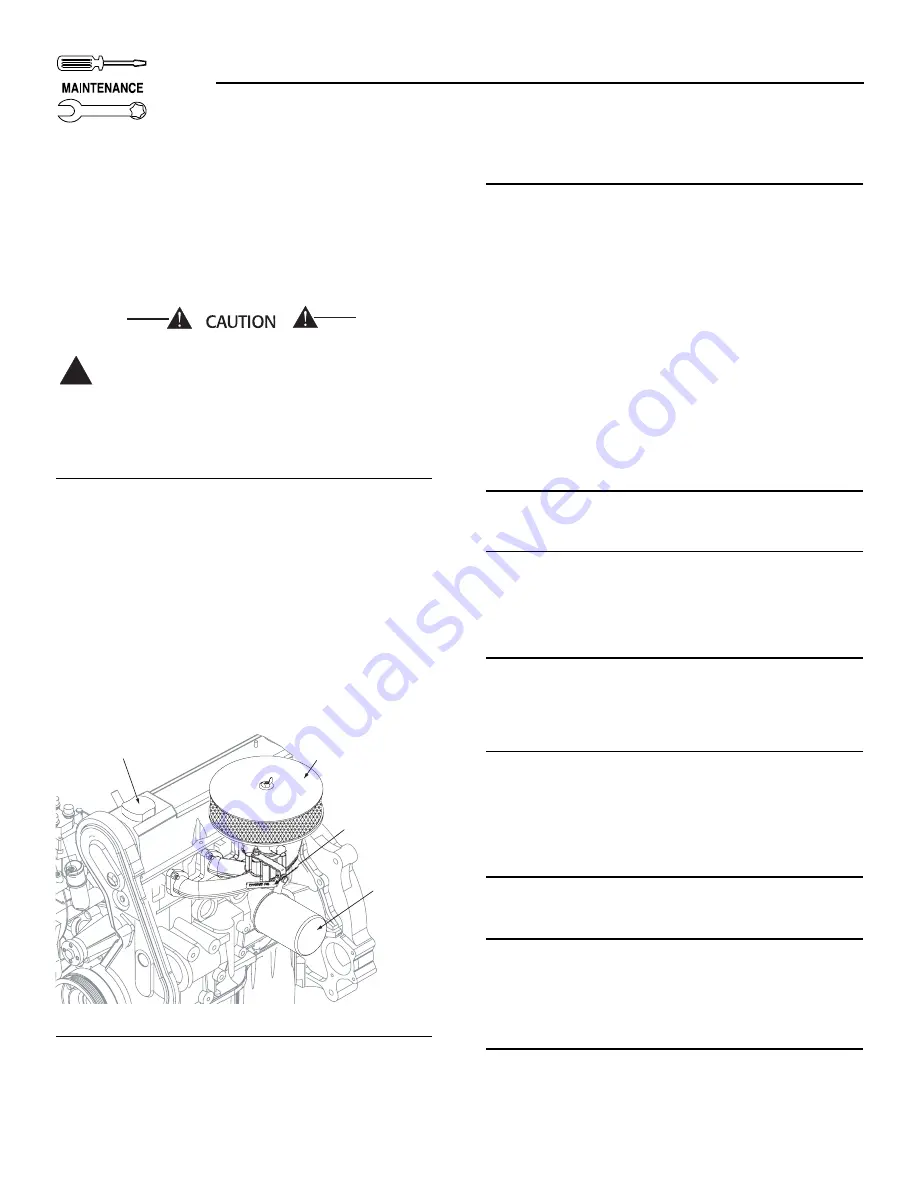
18 Generac
®
Power Systems, Inc.
4.6
OVERLOAD PROTECTION FOR
ENGINE DC ELECTRICAL SYSTEM
Engine cranking, start up and running are controlled
by a solid state Engine Controller circuit board.
Battery voltage is delivered to that circuit board via a
15 amp fuse. These overcurrent protection devices
will open if the circuit is overloaded.
If a circuit breaker opens or a fuse element
melts, find the cause of the overload before
resetting the circuit breaker or replacing the
fuse.
4.7
CHECKING FLUID LEVELS
4.7.1
CHECK ENGINE OIL
Check engine crankcase oil level (Figure 4.3) at least
every 20 hours of operation, or prior to use.
• Remove oil dipstick and wipe dry with a clean,
lint-free cloth.
• Install oil dipstick, then remove again.
• Oil should be between FULL and ADD marks.
• If oil level is below the dipstick ADD mark, remove
oil fill cap. Add the recommended oil to bring oil
level up to the FULL mark. DO NOT FILL ABOVE
THE “FULL” MARK. See “Engine Oil Recommen-
dations” for recommended oils.
Figure 4.3 - Oil Dipstick and Oil Fill Cap
4.7.2
BATTERY FLUID
Check battery electrolyte fluid based on the
Maintenance Schedule. Fluid should cover separa-
tors in all battery cells. If fluid level is low, add dis-
tilled water to cover tops of separators. DO NOT USE
TAP WATER IN BATTERY.
4.7.3
ENGINE COOLANT
Check coolant level in coolant recovery bottle. See
Specifications.
• Add recommended coolant mixture as necessary.
• Periodically remove radiator pressure cap (only
when engine has cooled down) to make sure the
coolant recovery system is functioning properly.
Coolant should be at bottom of radiator filler neck.
If coolant level is low, inspect gasket in radiator
pressure cap. Replace cap, if necessary. To have
pressure cap tested, contact an authorized
Generac Service Dealer. Inspect cooling system
and coolant recovery system for leaks.
4.8
MAINTENANCE OWNER/
OPERATOR CAN PERFORM
4.8.1 CHECK ENGINE OIL LEVEL
Refer to “Checking Fluid Levels”.
4.8.2 CHECK BATTERY
• See “Checking Fluid Levels”.
• Check battery cables for condition, tightness, cor-
rosion or damage. Clean, tighten or replace as
necessary.
4.8.3 EXERCISE SYSTEM
Start the generator engine at least once every seven
days and let it run at least 20 minutes. See “Weekly
Exercise Cycle”.
4.8.4 INSPECT COOLING SYSTEM
• Inspect engine cooling system. See “Maintenance
Schedule”.
• Check hoses for damage, deterioration, leaks, etc.
Correct any discrepancies found.
• Check hose clamps for tightness.
4.8.5 CHECK ENGINE COOLANT LEVEL
See “Checking Fluid Levels”.
4.8.6 PERFORM VISUAL INSPECTION
Complete a thorough visual inspection of the entire
engine-generator monthly. Look for obvious damage,
loose, missing or corroded nuts, bolts and other fas-
teners. Look for fuel, oil or coolant leaks.
4.8.7 INSPECT EXHAUST SYSTEM
Inspect the exhaust system at least once every three
months. Check all exhaust system pipes, mufflers,
clamps, etc. for condition, tightness, leaks, security,
damage.
Oil Dipstick
Oil
Filter
Oil Fill Cap
Engine
Air Cleaner
!
Section 4 — Maintenance
Guardian Liquid-cooled 25 kW Generator