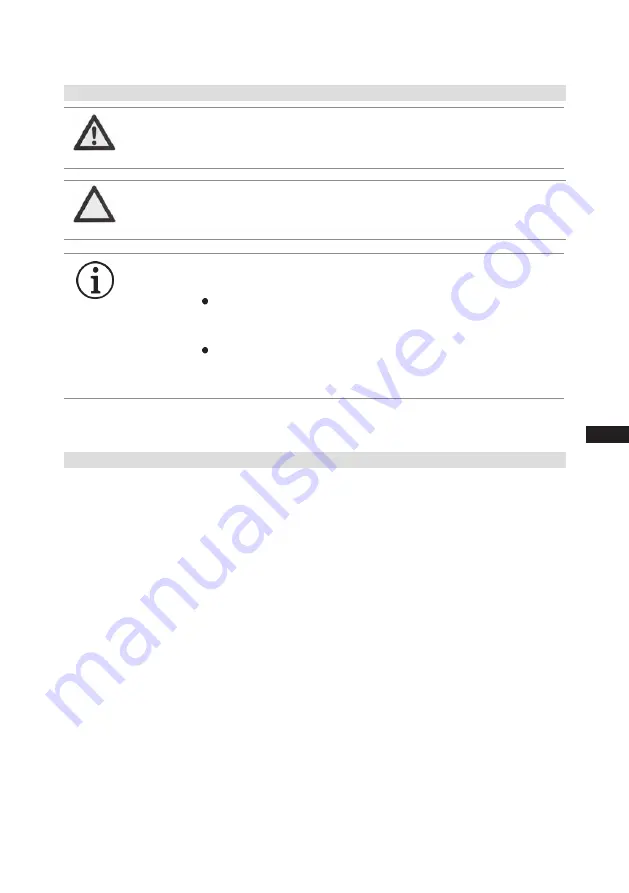
D
GB
F
E
21
09726-09.2015-DGbF
6
|
Electrical connection
6.1 Information for contactor and motor contactor selection
INFO
Connect the compressor motor in accordance with the circuit diagram
(see inside of terminal box).
Use suitable cable entry point of the correct protection type (see
name plate) for routing cables into the terminal box. Insert the strain
reliefs and prevent chafe marks on the cables.
Compare the voltage and frequency values with the data for the
mains power supply.
Only connect the motor if these values are the same.
DANGER
Risk of electric shock! High voltage!
Only carry out work when the electrical system is disconnected
from the power supply!
6 Electrical connection
All protection devices and switching or monitoring units must be fitted in accordance with the local
safety regulations and established specifications (e.g. VDE) as well as with the manufacturer’s infor
-
mation.
Motor protection switches are required!
Motor contactors, feed lines, fuses and motor
protection switches must be rated on the basis of the maximum working current (see
name plate
).
For motor protection use a current-dependent and time-delayed overload protection device for moni-
toring all three phases. Set the overload protection device so that it must be actuated within 2 hours,
if there is 1.2 times the max. working current.
ATTENTION When attaching accessories with an electrical cable, a minimum
bending radius of 3 x the cable diameter must be maintained for
laying the cable.
Содержание HGZ7 Series
Страница 41: ...D GB F E 41 09726 09 2015 DGbF...