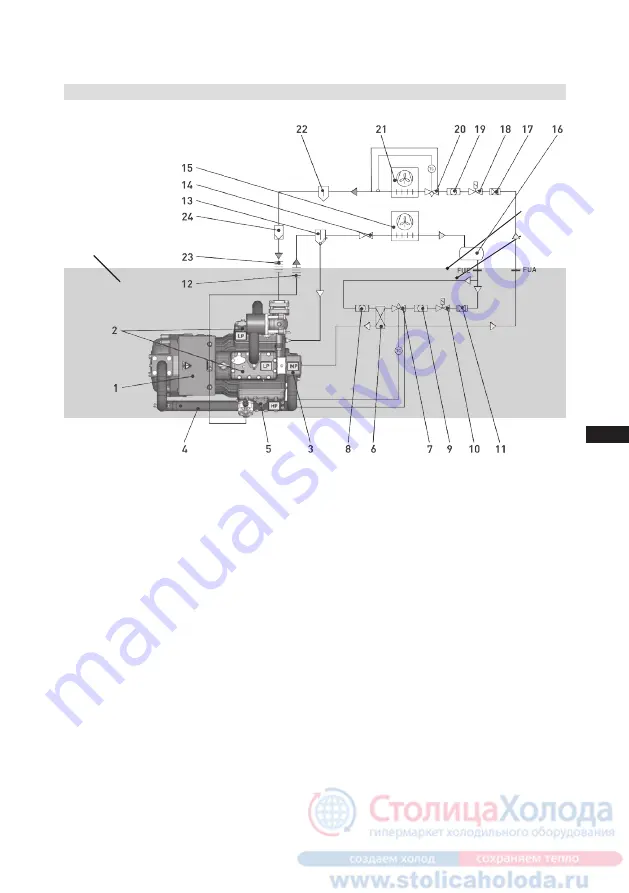
D
GB
F
E
13
09726-09.2013-DGbF
4
|
Description of functions
Explanations
1 Compressor
2 Cylinder LP-stage
3 Intermediate pressure chamber MP
4 Intermediate pressure line MP
5 Cylinder HP-stage
6 Liquid subcooler
7 Reinjection valve
8 Sight glass
9 Sight glass
10 Solenoid valve
11 Filter drier
12 Damper, pressure line
13 Oil separator
14 Non-return valve
15 Condenser
16 Refrigerant receiver
17 Filter drier
18 Solenoid valve
19 Sight glass
20 Expansion valve (evaporator)
21 Evaporator
22 Liquid separator
23 Damper, suction line
24 Filter suction line
LP = Low pressure
MP = Intermediate pressure
HP = High pressure
FUE = Liquid subcooler, inlet
FUA = Liquid subcooler, outlet
Scope of supply
Line A
Line B
4.1
Two-stage refrigeration cycle with liquid subcooler
Fig. 13
Содержание Bock HGZ Series
Страница 41: ...D GB F E 41 09726 09 2013 DGbF...