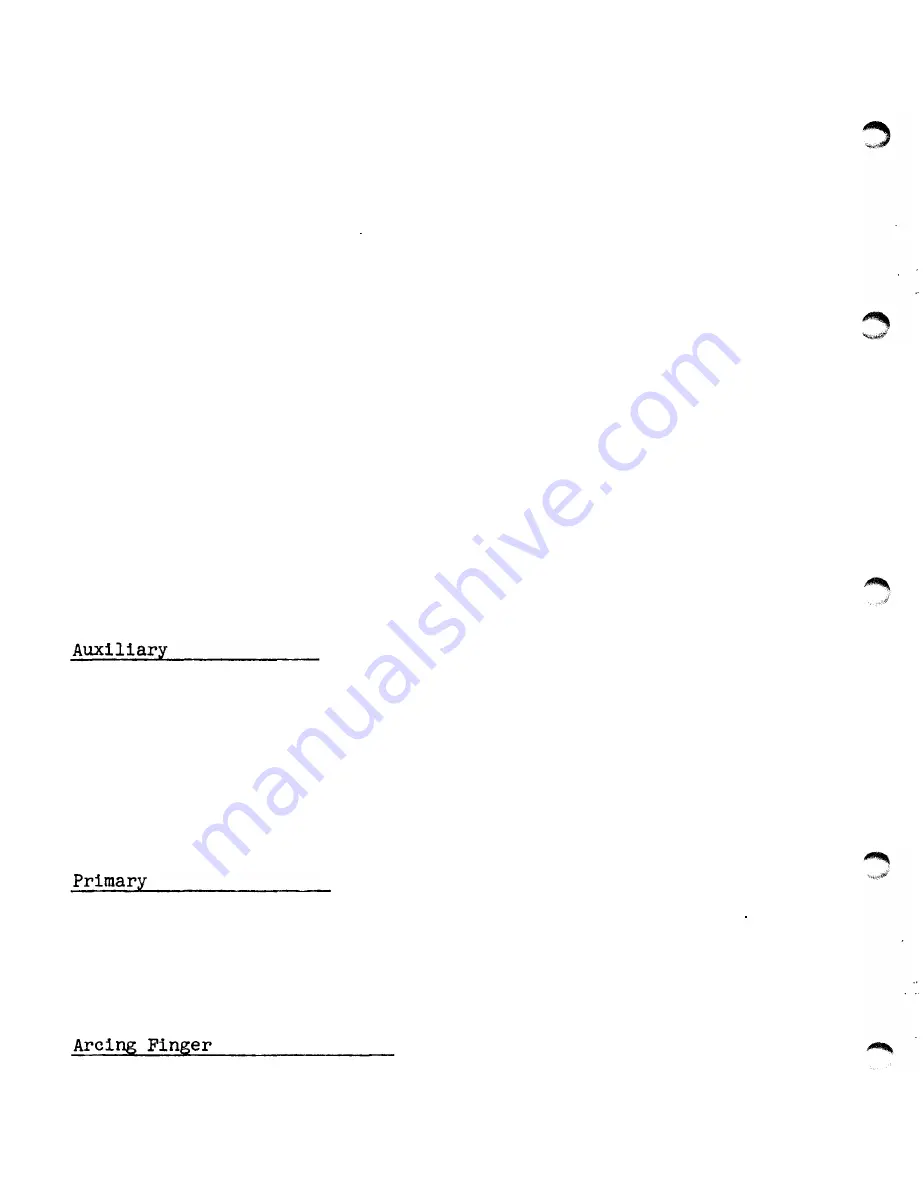
GEI-88767
(10) Fig. 7 at the bottom of the chute. Position the chute so that
the blade will travel the full length without binding or heavy scrap
ing, and tighten the bolts.
A dimension of 1-1/6" should be maintained from the rear edge of the
arc chute to the front edge of the primary finger contact support at
all times when moving or re-aligning the chute. Re�er to Fig. 7. The
auxiliary blade contacts (2) Fig. 4 inside the chute should be proper
ly positioned to latch the auxiliary blade when this dimension is
maintained.
The auxiliary blade must be released by the contacts when the primary
blade has been opened to a predetermined gap. With the operating
springs blocked, open the primary contacts and slowly move the primary
blade until the auxiliary blade is released. At the point of release
the gap from the lower edge of the primary finger (the bottom finger
(2) Fig. 9 to the buffer stop or spacer (3) should be 4-7/8" to 5-3/8"
on the 4. 8KV and 7-1/811 to 7-3/4" on the 13. 2 KV switch. If the gap
is not correct the vertical location of the chute must be changed.
For gaps greater than the above range, the chute must be lowered, for
gaps that are less the chute must be raised. To adjust the chute, re
move the upper and lower mounting bolts (2
&
10) Fig. 7. Move shims
(3) from the bottom to the top of the support to decrease the gap.
To increase the gap, move some of the top shims to the bottom support.
When the release gap is properly set, check again the dimension from
the back edge of the chute to the primary contact finger support and
the alignment of the auxiliary blade in the chute opening.
Blade Release
The auxiliary blade release hook (14) Fig. 7 should be adjusted to
hold the bladb out of the arc chute until a predetermined position
in the closing operation.
Close the switch slowly with the maintenance handle and note the posi
tion of the primary blades when the auxiliary blade is released by the
hook. The hook should be adjusted by setting the camming screw (8)
Fig. 4 to release the auxiliary blade within the range of 1/2
11
before
Primary contacts touch . . After adjustment is made the lock nut (9)
Fig. 4 should be tigntened.
Contact Pressure
The primary finger pressure has been adjusted at the factory to be 12
pounds per contact on the 600A switch and 24 pounds per contact on the
1200A. This can be measured with a pull scale exerting a pressure
against the contact surface. The contact pressure of each finger (5)
Fig.
7
should be measured individually. Increase or decrease the con
tact pressure by loosening or tightening the contact bolts (4) Fig. 7.
Contact Pressure
The arcing finger contact pressure should be 12 pounds on all 600A and
16 pounds on all 1200A switches. This pressure can again be measured
8
{