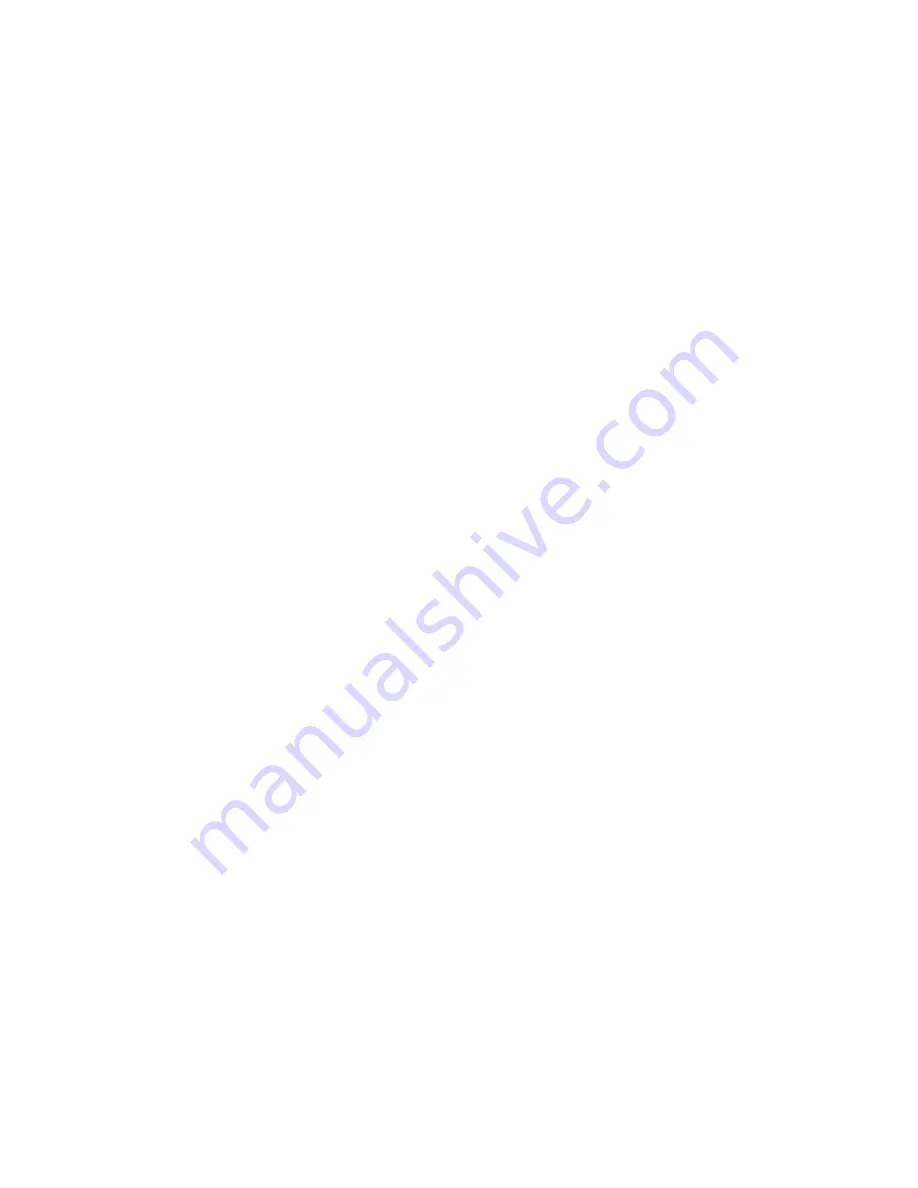
Application
8. Repeat 200% calibration test.
9.
Dielectric voltage withsta nd:
The tested breaker m ust
withstand applied voltage of twice rated plus 1000 volts
(2200 volts for 600V rated breaker) for one minute be
tween:
a) line and load terminals,
b) poles of opposite polarity, and
c) live ports and the metal enclosure.
Performance - H igh Available Fault Current
(Hi-Break® Power Break® I I ) Circuit Breakers - The U L
Standard 489 specifies additional, optional requirements for
evaluation of breakers on faults higher than the "standard"
values shown in item 5.
Test sequence is as follows:
1. Calibration:
200% of rated current.
2. I nterrupting capacity:
Short-circuit test ore conducted
to evaluate I ll maximum IC rating, (2) IC at maximum
voltage, and (3) IC at maximum kVA. If one o r more tests
ore covered by another, for example, if maxim u m kVA
occurs at maximum voltage test, they may be omitted.
An
"0"
operation and a "CO" operation is requ i red for
each evaluation. Acceptable high available fau lt current
ratings ore, in RMS symmetrical kilo amperes: 7.5, 10, 14,
18, 22, 25, 30, 35, 42, 50, 65, 85, 100, 125, 150, 200.
3.
Trip-Out:
Conducted at 250% of rated current . Breakers
must trip within some time limits as for 200% calibration.
4. Dielectric voltage withsta nd:
Conducted at twice rated
(test) voltage.
The preceding is on abbreviated description. Refer to the
section Standards and References for specific standards.
GE Testing
G E has developed a qualification test plan for the Power+™,
M icroVersoTrip Plus™ and M icroVersaTrip PM™ trip units that
is in addition to the tests required by Standard UL 489. The
objective is to demonstrate performance and reliability under
severe operating conditions. Essential components of the
internal qualification test are:
GE Trip Unit Testing
1. Temperature Cycling.
This test verifies that units are
not damaged when exposed to many extreme thermal
cycles. The test consists of romping units from -20°C to
70°C a minimum of 10 times each. Units are soaked at
each extreme temperature for 1 hour minimum for each
cycle.
2. Storage Temperatu re.
This test ensures that units will
operate properly following exposure to extreme storage
temperature for 72 hours. Units a re stored in on un
powered state at -55°C and +85° for 72 hours and then
subjected to functional testing to verify proper operation.
3.
Voltage Surge.
This test ensures that the circuit breaker
is not susceptible to direct and coupled surge voltages
on any primary line or any control input or output line.
The test is performed per the ANSI C37.90.1 Surge With-
stand Capability specification on a l l input and output
l ines connected to the breaker. Both fast transient and
oscillatory surges a re applied.
4. RF and E M I.
These tests ensure that the breaker is not
susceptible to radiated electromagnetic fields. The test is
performed per the ANSI C3 7.90.2 Radiated Field I mmuni
ty specification. The breaker is subjected to a modulated
field of 30-SOV/m from 20 MHz tolGHz with the field
polarization applied vertica l ly and horizontally.
5. Wa lkie-Talkie Immunity.
The breaker is subjected to
standard types of industrial walkie-talkies to ensure that
it is immune to nuisance trips or improper operation
when nearby walkie-talkies a re used.
6.
Wiggins I m munity.
Test a re performed to ensure the
breaker will not nuisance trip when exposed to a high in
ductive load (Wiggy) voltage tester across the energ ized
phase lines.
7.
Humidity.
A number of u n its a re exposed to high-humid
ity environments of 95% relative humidity for a period of
one week to simulate severe environmental conditions.
8. Heat/Humidity Endura nce.
LCD display modules ore
exposed to +80°C, 85% relative humidity for a minimum
of 1000 hours to ensure that the LCD seal and polor
izers can withstand severe environments for prolonged
periods of time.
9.
POWER LEADER™ Systems Tests.
Tests are performed
to prove that the trip units can be integrated into existing
POWER LEADER networks. A Iorge number of trip u nits
are configured into a Iorge network of various POWER
LEADER devices to ensure that they can communicate
when subjected to Iorge network conditions. M any types
of systems tests are performed including: communica
tion over long distances, multiple simultaneous event
testing, communication protocol testing, integration
testing with other d evices, and bus fault and bus loading
testing.
10. Dust.
U nits are subjected to severe atmospheric dust
environments per M IL-STD-810E, Method 5 10.3, Proc. I.
1 1.
Salt Spray.
U nits are subjected to severe salt spray and
salt fog environments per ASTM Bl17.
12. Electro-Static Discharge.
Units are subjected to Electro
Static Discharge test of up to 8.0kV per I EC 801-2.
GE Breaker Testing
U L Vibration Testing:
GE Power Break II circuit breakers have been i nvestigated in
accordance with UL 489 Supplement SB and vibration tested
in accordance with Supplement S B, Section SB2. This quali
fies them as U L listed Naval circuit breakers intended for use
aboard non-combatant and auxiliary naval ships over
19.8 meters (65 feet) in length. Circuit breakers complying
with these requirements shall be marked "Naval".
39
www . ElectricalPartManuals
. com
www
. ElectricalPartManuals
. com
Содержание Power Break II
Страница 114: ...Notes 114 w w w E l e c t r i c a l P a r t M a n u a l s c o m w w w E l e c t r i c a l P a r t M a n u a l s c o m ...
Страница 115: ...115 w w w E l e c t r i c a l P a r t M a n u a l s c o m w w w E l e c t r i c a l P a r t M a n u a l s c o m ...
Страница 117: ...w w w E l e c t r i c a l P a r t M a n u a l s c o m w w w E l e c t r i c a l P a r t M a n u a l s c o m ...
Страница 118: ...w w w E l e c t r i c a l P a r t M a n u a l s c o m w w w E l e c t r i c a l P a r t M a n u a l s c o m ...