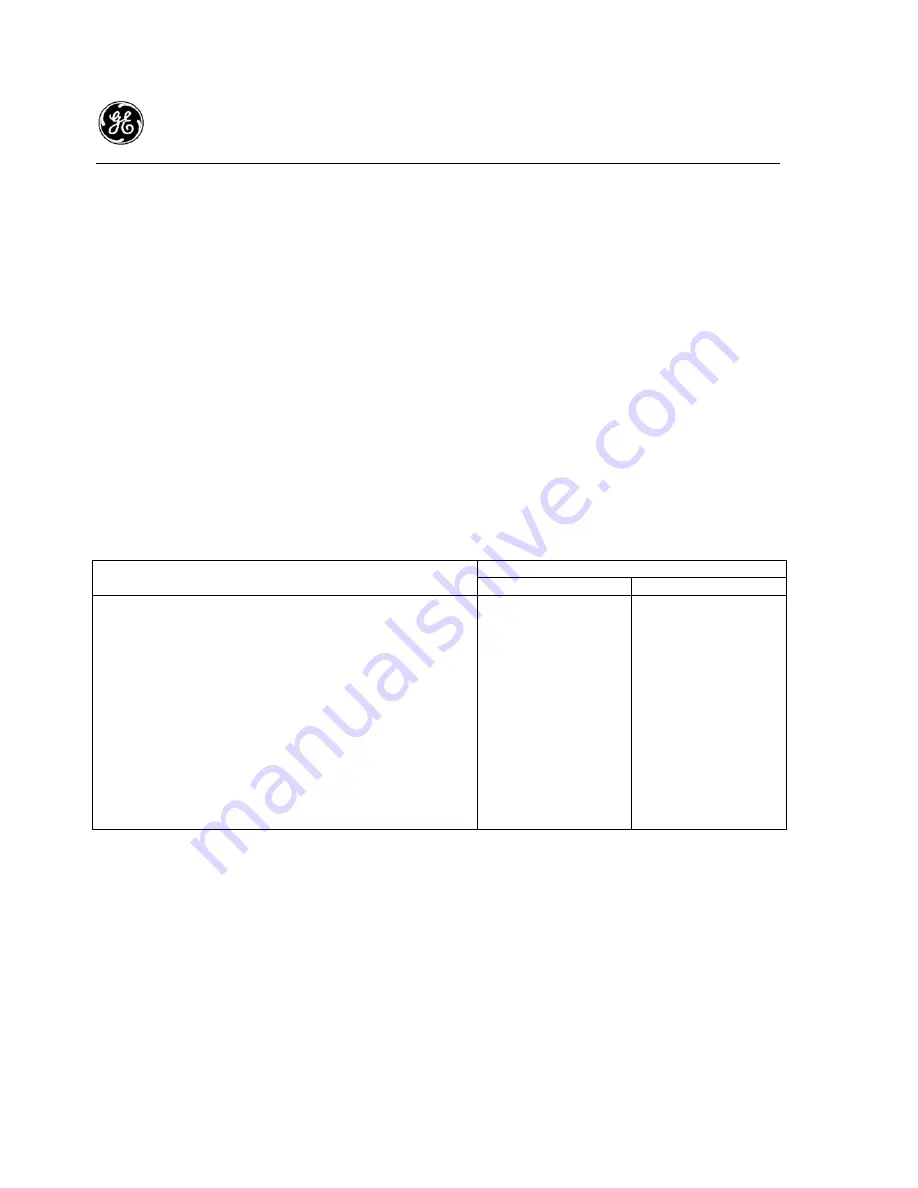
GE Energy Motors GEEP-427-I Copyright 2009, The General Electric Company, USA
22
GEEP-427-I Pegasus, Horizontal Induction Motor
TEWAC, Sleeve Bearing
of time, cause corrosive deposits to develop which
further contribute to deterioration.
Keep metal particles such as copper, iron or steel
away from the machine. This is especially important for
iron and steel since such particles will adhere
magnetically and are extremely difficult to remove. They
may be agitated by magnetic fields present during
operation causing abrasion and eventual failure of
insulation. If for any reason sawing, drilling, machining,
etc., of ferrous materials must be done in the general
vicinity of the unit, such work should be done as
remotely as possible. The unit should not be in operation
at that time. All filings, chips, etc., should be completely
removed prior to starting the unit. The same precautions
should be observed for copper chips or other conducting
materials.
In removing dirt and contamination from the
machine, a vacuum is much preferred to positive air
pressure. Air pressure does not remove, but only
relocates, the objectionable material. It frequently drives
and embeds foreign material into the sides of insulation
as well as into natural crevices inside the machine. A
suction hose from an industrial-type vacuum cleaner
should be used for cleaning. The hose wand or nozzle,
which comes into direct contact wit the machine parts,
should be small enough in cross-section as to produce a
reasonably high air velocity at the entrance to the wand.
This is necessary to accelerate and move the foreign
material into the vacuum hose.
Frequency of Inspection
Frequency of inspection will vary with the item
being inspected and with the severity of local
environmental conditions.
Certain items, such as winding temperature,
bearing temperature and vibration amplitude should be
monitored on a conditions basis. If local provision has
been made for readout or printout of these parameters,
and if contacts and relays are provided to shut down the
unit in case of above-normal temperatures, then all that is
required for inspection is to assure that the protective
equipment is operational and set to detect abnormal
operation. Conversely, if no provision has been made to
Item
Frequency of Inspection
Clean
Conditions
Severe
Conditions
Stator winding (including bracing and support structures, coil
end connections, insulation resistance check)
Yearly Quarterly
Rotor end ring (or end turns)
Yearly
Yearly
Rotor removal (rotor and stator bore)
Every Five Years
Every Five Years
Stator core (with rotor removed)
Every Five Years
Every Five Years
Bearing inspection
Every Three Years
Yearly
Bearing lubrication
Twice Yearly
Bi-Monthly
Separate lube system (if supplied)
Quarterly
Monthly
protect the winding and bearings from over temperatures
by means of protective relays, then the maintenance
program must discharge the local operator with being
aware of the winding and bearing temperatures on a
continuous basis. This also applies to vibration
monitoring and protective equipment.
Routine inspection and maintenance of the stator
winding, rotor winding, core, brushless exciter, brushless
and collector rings (for machines supplied with this
equipment), bearings and top covers should be done on a
scheduled basis. However, the frequency will depend
upon the severity of local environmental conditions.
Installations located in clean environments will require
only occasional routine inspections. Other installations
located in severe environments, such as paper mills,
cement mills, steel mills, power stations, etc., will require
routine inspections more frequently. The accompanying
tabulation is suggested as a basis for a maintenance
program for these two cases. There will be may
installations falling between then, as well as installations
Содержание Pegasus MHV GEEP-427-I
Страница 46: ...GE Energy Motors 46 ...