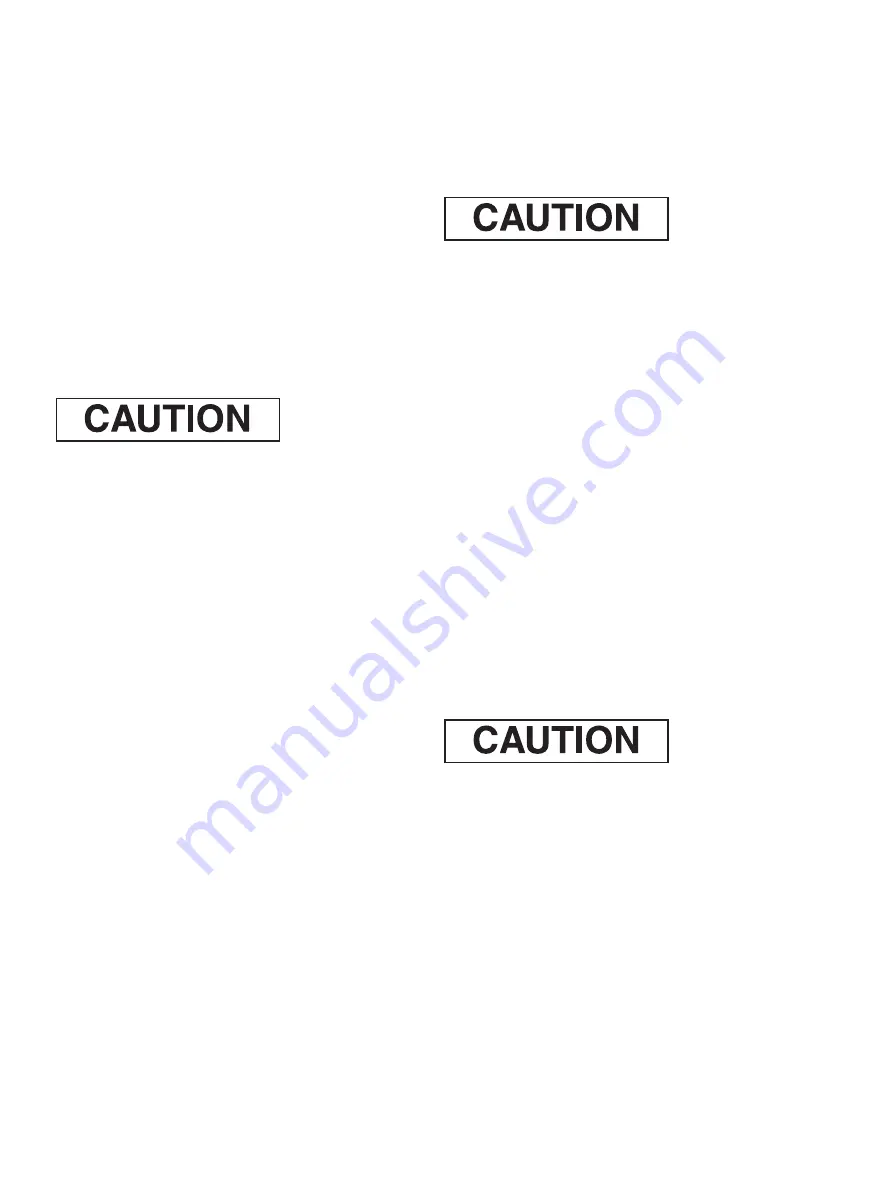
14 | GE Oil & Gas
© 2015 General Electric Company. All rights reserved.
cage groove, slightly open the rings by hand and slide
them one after the other along the plug, taking care not
to damage the parts.
Note: The cuts on each ring are to be placed at about
180° from each other.
6.2.5 41375 high temperature valve
(232°C to 316°C)
(Figure 19)
These valves are equipped with a seal ring composed of a
jacket and a metallic spring and two backup rings (11G).
Assemble the different parts as shown in Figure 19,
starting by the backup rings.
Put these parts as shown in Figure 19, the angle of 90°
of the backup ring in front of the extrusion gap between
cage and plug.
6.3 41405 Valve Plug and
Cage Assembly
(Figure 17)
6.3.1 Assembly of valve plug and auxiliary pilot plug
Assemble, as appropriate, the flat spring or the coil
springs then the valve plug/plug stem assembly.
Using the same tools as those used for disassembly
(see chapter “Disassembly”), compress the springs so
that the retaining ring can be inserted in the groove of
the main plug.
6.3.2 Assembly of cage
Place the cage over the valve plug assembly via the top
of the plug stem. When doing so, take particular care to
position the ring correctly.
6.4 Assembly of the Parts Inside
the Valve Body
(Figures 17, 18 and 19)
Proceed as follows:
• After checking that the surfaces are perfectly clean,
place the seat gasket (14) in the valve body, making
sure that it is centered as well as possible.
• Mount the seat ring or the diffuser seat (13).
• Mount:
– The cage (16) for 41305, 41605 and 41905 valves,
– The cage/plug/stem assembly for 41405 valves,
– The STACK assembly (making sure that the face with
the smallest number of holes is in contact with the
seat ring), and cage (16) for 41375 valves.
For the double-cage assembly, carry out the following
operations:
• Put the inner cage (16) upside down,
• Encase the outer cage (75) on the inner cage, maintain
them together with the two pins (76).
• In the case of valves other than 41405 valves, insert
the valve plug/stem/ring assembly into the cage taking
particular care as it goes past the ring or spring-
energized seal ring.
• In the case of valves with a N.D. less than 150 (6”), place
the body/cage gasket in the valve body, making sure
that it is centered as well as possible.
• For valve sizes 150 to 400 mm (6 to 16”), insert either
the cage gasket (24) or the flat spring washer (17).
• For valve sizes 450, 600 and 750 mm (18, 20 and 24”),
insert either the first cage gasket, the cage washer and
the second cage gasket or the flat spring depending
on the type of valve, then place the body gasket (10) in
the valve body making sure that it is centered as well
as possible.
To the direction of assembly of spring washer:
• ND 150 (6”) to 450 (18”) valves, the concave face is
upwards,
• ND 500 (20”), and 600 (24”), the concave face is
downwards and the tapped holes are visible.
6.5 Assembly of Bonnet
Check that the packing ring (6), the spacer (5) and the
guide bushing (22) have been removed from the bonnet.
Position the bonnet (7) above the valve, so that the
packing flange studs (2) are perpendicular to the flow
direction of the valve.
Thread the bonnet (7) onto the valve stem (1) and push it
down carefully until it goes into the valve body studs (21)
and takes up its correct position.