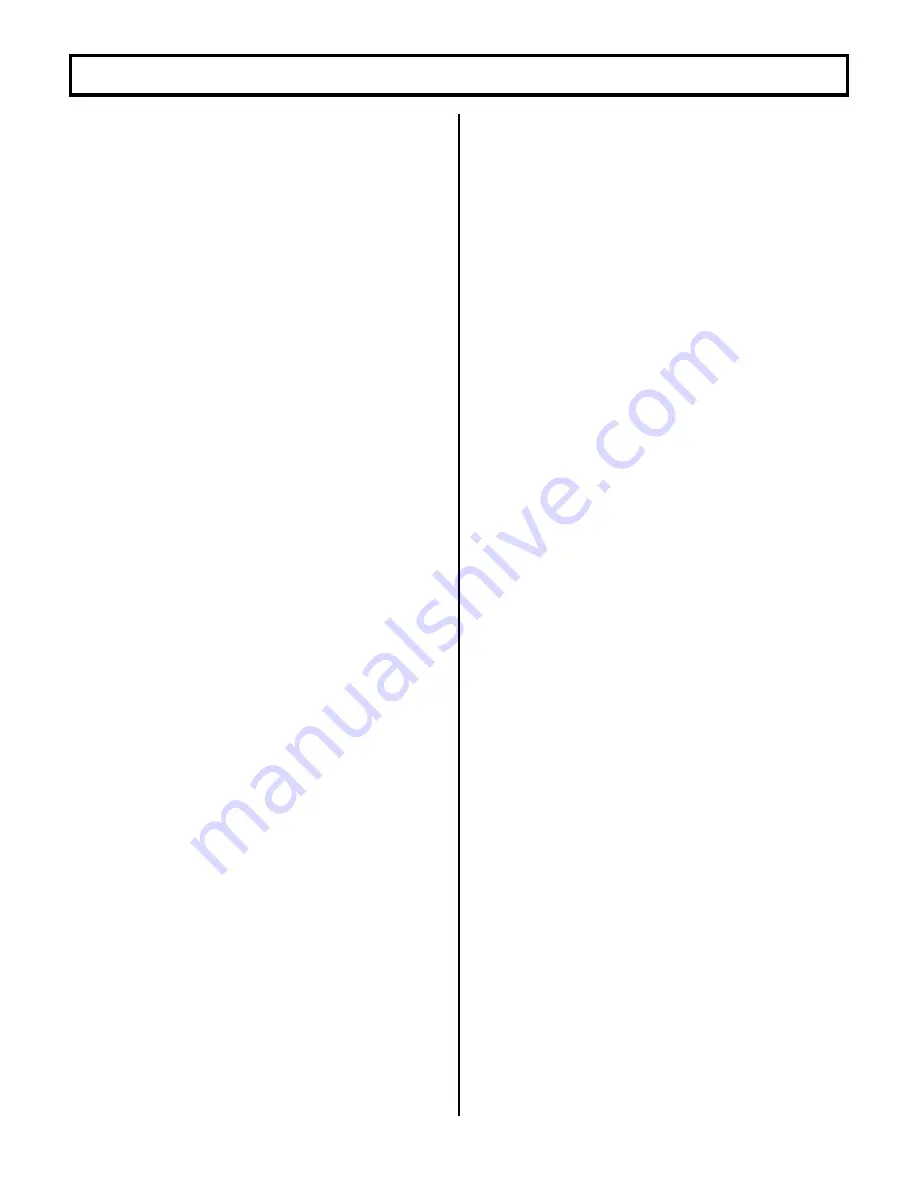
BASIC OPERATION AND FEATURES
IT400 TRANSISTOR CONTROL
Page
7
April 2012
current is less than the value set by Function 24 and
the accelerator input voltage is less than 1 volt. It is
important to note that this function is used to optimize
motor and control performance, and this setting will
be determined by FSIP and OEM engineers at the
time of vehicle development. This setting must not
be changed by field personnel, without the
permission of the OEM.
Section 2.1.4.b Speed Limits
This feature provides a means to control speed by
limiting motor volts utilizing three "adjustable speed
limits. This motor volt limit regulates top speed of the
transistor controller, but actual truck speed will vary
at any set point depending on the loading of the
vehicle. Each speed limit can be adjustable with the
Handset using Functions 11, 12, and 13.
Section 2.1.5 Ramp Operation
Section 2.1.5a Ramp Start
This feature provides maximum control torque to
restart a vehicle on an incline. The memory for this
function is the directional switch. When stopping on
an incline, the directional switch must be left in its
original or neutral position to allow the control to
initiate full power when restarted. The accelerator
potentiometer input will modulate ramp start current.
Section 2.1.5b Anti-Rollback
This feature provides retarding torque to limit rollback
speed in the non-travel direction when the ACC pedal
is released when stopping on a grade, or when the
brake pedal is released when starting on a grade.
This feature forces the vehicle to roll very slowly
down the grade when accelerator or brake is
released. Because the vehicle can gain significant
speed during roll-back, the torque needed to re-start
on the ramp is lower than an unrestricted roll-back
speed.
Section 2.1.6 On-Board Coil Drivers & Internal
Coil Suppression
Coil drivers for the LINE contactor and BRAKE
are on-board the control card. These accessories
must have coils rated for the vehicle battery volts.
Section 2.2 System Protective Override
Section 2.2.1 Static Return to Off (SRO)
This inherent feature of the control is designed to
require the driver to return the directional lever to the
neutral position anytime he leaves the vehicle and
returns. Additionally, if the seat switch or key switch
is opened, the control shuts off and cannot be
restarted until the directional lever is returned to
neutral. A time delay of approximately 2 seconds is
built into the seat switch input to allow momentary
opening of the seat switch, if a bump is encountered.
Section 2.2.2 Accelerator Volts Hold Off
This feature checks the voltage level at the
accelerator input whenever the key switch or seat
switch is activated. If, at start up, the voltage is less
than 3.0 volts, the control will not operate. This
feature assures that the control is calling for low
speed operation at start up.
Section 2.2.3 Pulse Monitor Trip (PMT)
The PMT design contains three features which shut
down, or lock out, control operation if a fault
conditions occurs that would cause a disruption of
normal vehicle operation:
Look
ahead
Look
again
Automatic look again and reset
The PMT circuit will not allow the control to start
under the following conditions:
The control monitors both armature and field
FET's at start-up and during running.
The control will not allow the line contactor to
close at start-up, or will drop it out during running,
if either the armature or field FET's are defective,
so as to cause uncontrolled truck movement.
Section 2.2.4 Thermal Protector (TP)
This temperature sensitive device is internal to the
power transistor (Q1) module. If the transistor's
temperature begins to exceed the design limits, the
thermal protector will lower the maximum current
limit, and maintain the transistors within their
temperature limits. Even at a reduced current limit,
the vehicle will normally be able to reach sufficient
speed. As the control cools, the thermal protector
will automatically reset, returning the control to full
power.
Section 2.2.5 Low Voltage
Batteries under load, particularly if undersized or
more than 80 percent discharged, will produce low
voltages at the control terminals. The IT control is
designed for use down to 50 percent of a nominal
battery voltage of 36-84 volts, and 75 percent of a
nominal battery voltage of 24 volts. Lower battery
voltage may cause the control to operate improperly,