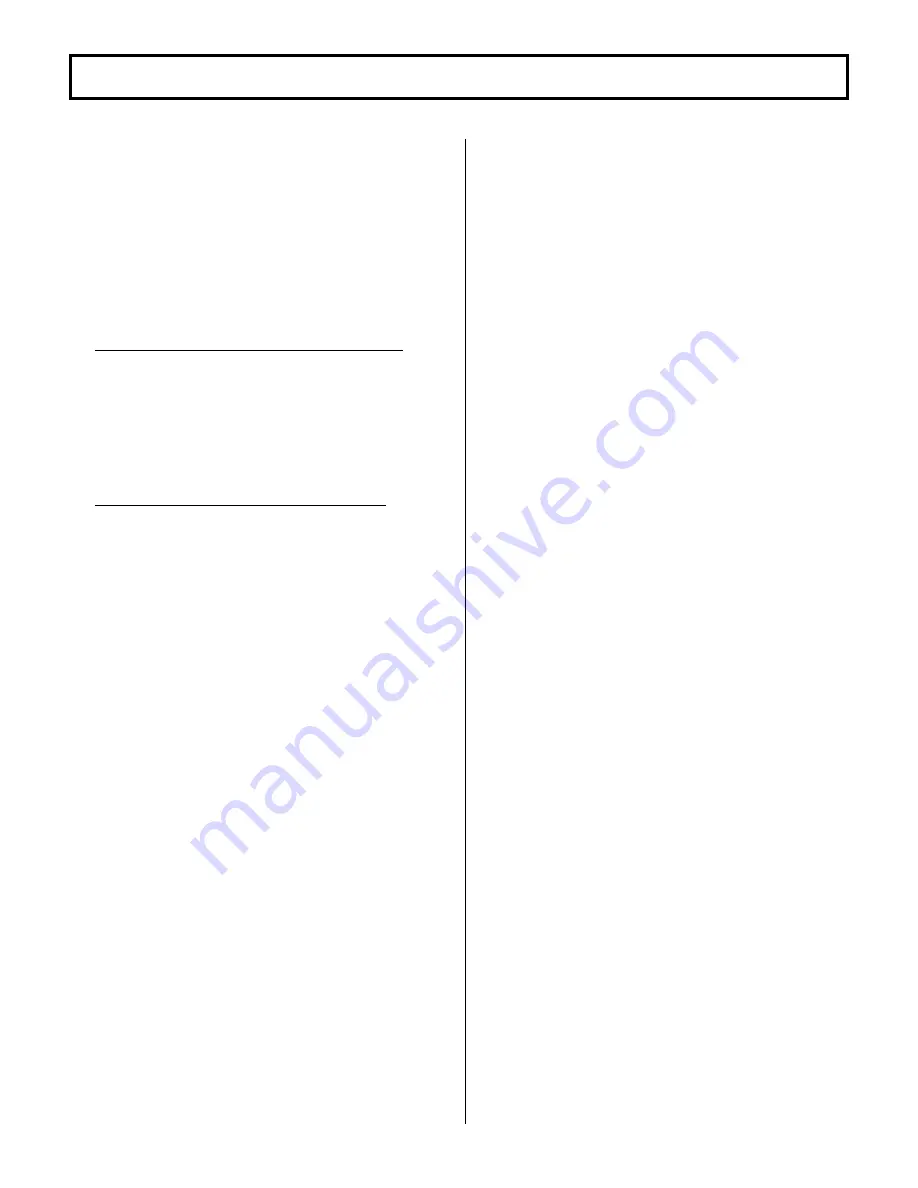
INSTALLATION AND OPERATION
SX TRANSISTOR CONTROL
Page
12
Section 4.0 TROUBLESHOOTING AND DIAGNOSTIC STATUS CODES
Section 4.1 General Maintenance Instructions
The transistor control, like all electrical apparatus, does
have some thermal losses. The semiconductor junctions
have finite
temperature
limits, above which these devices
may be damaged. For these reasons, normal
maintenance should guard against any action which will
expose the components to excessive heat and/or those
conditions which will reduce the heat dissipating ability of
the control, such as restricting air flow.
The following Do’s and Don’t’s should be observed:
Any controls that will be applied in ambient temperatures
over 100° F (40° C) should be brought to the attention of
the vehicle manufacturer.
All external components having inductive coils must be
filtered. Refer to vehicle manufacturer for specifications.
The wiring should not be directly steam cleaned.
In dusty
areas, blow low-pressure air over the control to remove
dust. In oily or greasy areas, a mild solution of detergent
or denatured alcohol can be used to wash the control,
and then low-pressure air should be used to completely
dry the control.
For the control to be most effective, it must be mounted
against the frame of the vehicle. The metal vehicle
frame, acting as an additional heat sink, will give
improved vehicle performance by keeping the control
package cooler.
Apply a thin layer of heat-transfer
grease (such as Dow Corning 340) between the control
heat sink and the vehicle frame.
Control wire plugs and other exposed transistor control
parts should be kept free of dirt and paint that might
change the effective resistance between points.
CAUTION: The vehicle should not be plugged when
the vehicle is jacked up and the drive wheels are in a
free wheeling position. The higher motor speeds can
create excessive voltages that can be harmful to the
control.
Do not hipot (or megger) the control. Refer to control
manufacturer before hipotting.
Use a lead-acid battery with the voltage and ampere
hour rating specified for the vehicle. Follow normal
battery maintenance procedures, recharging before 80
percent discharged with periodic equalizing charges.
Visual inspection of GE contactors contained in the
traction and pump systems is recommended to occur
during every 1000 hours of vehicle operation. Inspection
is recommended to verify that the contactors are not
binding and that the tips are intact and free of
contaminants.
GE does not recommend that any type of welding be
performed on the vehicle after the installation of the
control(s) in the vehicle. GE will not honor control
failures during the warranty period when such failures
are attributed to welding while the control is installed in
the vehicle.
Section 4.2 Cable Routing and Separation
Electrical noise from cabling of various voltage levels can
interfere with a microprocessor-based control system.
To reduce this interference, GE recommends specific
cable separation and routing practices, consistent with
industry standards.
Section 4.2.1 Application Responsibility
T
he customer and customer’s representative are
responsible for the mechanical and environmental
locations of cables. They are also responsible for
applying the level rules and cabling practices defined in
this section.
To help ensure a lower cost, noise-free installation, GE
recommends early planning of cable routing that
complies with these level separation rules.
On new installations, sufficient space should be allowed
to efficiently arrange mechanical and electrical
equipment.
On vehicle retrofits, level rules should be considered
during the planning stages to help ensure correct
application and a more trouble-free installation.
Section 4.2.2. Signal/Power Level Definitions
The signal/power carrying cables are categorized into
four defining levels: low, high, medium power, and high
power. Within those levels, signals can be further divided
into classes.
Sections 4.2.2.a through 4.2.2.d define these levels and
classes, with specific examples of each. Section 4.2.3
contains recommendations for separating the levels.
4.2.2.a Low-Level Signals (Level L)
Low-level signals are designated as
level L
. These
consist of:
Analog signals 0 through ±15 V
Digital signals whose logic levels are less than 15 V
DC
4
– 20 mA current loops
DC busses less than 15 V and 250 mA
The following are specific examples of level L signals
used in drive equipment cabling:
Control common tie
Updated Sept 2019