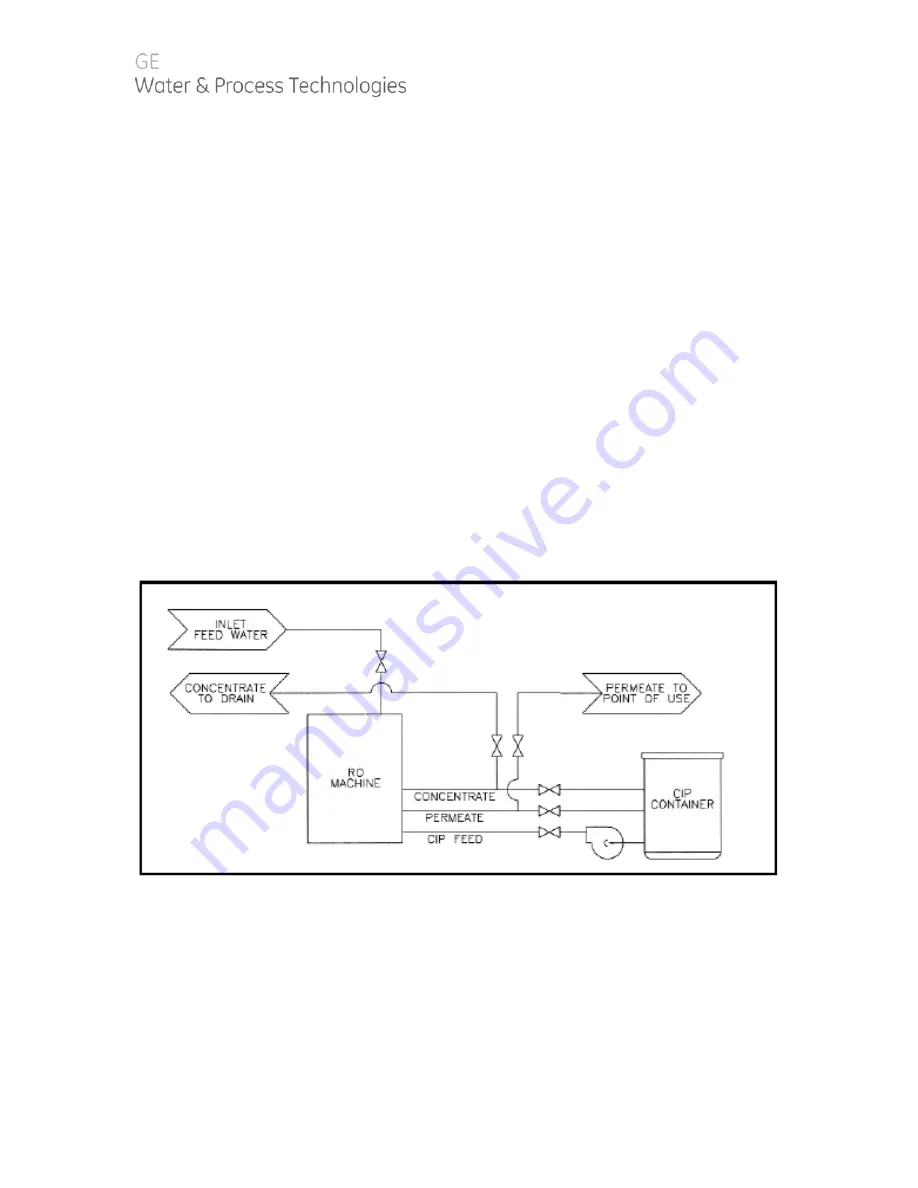
18
4.3.2.
Procedure to Clean with a CIP Pump
1.
With the machine running, open the CIP permeate valve, close the permeate
service valve and fill the CIP tank with permeate water. When the container is
filled to desired level, turn machine OFF.
2.
Add and mix up the cleaners in the CIP container. Please use only PA
membrane element compatible cleaners.
3.
Close the inlet feed water supply valve to the machine and open the CIP inlet
feed water to the CIP container.
4.
Close the permeate valve to point of use and also the concentrate valve drain.
5.
Open the CIP valves, allowing permeate and concentrate to return to the CIP
container. When set properly, the RO machine, the CIP pump, and the CIP
container should be assembled in a loop configuration to recirculate the water
through the machine and back to the container during cleaning. The size of
the CIP container should be a minimum of three times the permeate rate.
CAUTION:
GE recommends the use of a CIP or booster pump to provide the proper
feed water pressure and quantity to the RO machine during cleaning.
Figure 7.
Clean-In-Place Pump and Tank Hook-Up
With the machine set-up in the CIP configuration and the cleaning solution mixed in
the container, you are now ready to start the CIP process. Follow the Steps below.
1.
Check to ensure that the feed, permeate, and concentrate valves and line are
open and unrestricted in the tank loop.