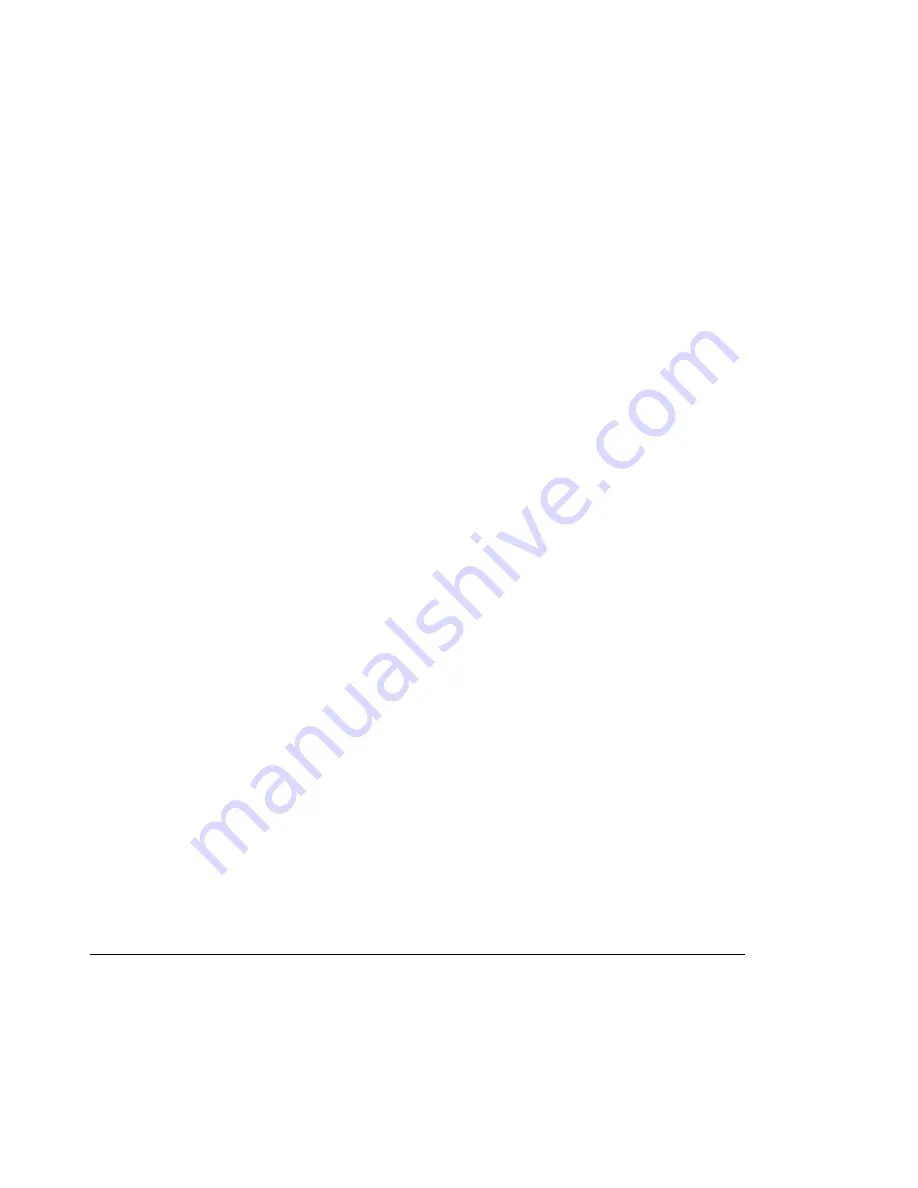
9
Connections to Control Board
Supply
Connect a
10A 240v non earth leakage
protected power supply to Din Rail terminals labelled A & N
Connect earth to the earth Din Rail terminal.
The VSD unit inherently operates with a small amount of earth leakage current which may cause nuisance
tripping of an earth leakage circuit breaker.
Motor Wires
Connect the shielded motor cable to Inverter terminals. Connect earth and shield to Earth Stud.
Control
Connect low voltage limit switch wires to limit switch terminals on circuit board. Note the common terminal and
open/close terminals for motor one and motor two. Connect the shield (if used) to earth.
Control Inputs
The P.E, OPN and STP inputs require a normally closed switch contact and therefore should be shorted to the COM
terminal if not used. This is done via bridging links already on the circuit board (bottom left corner) The CLS, OSC
and PED inputs require a normally open switch contact and therefore should be left unconnected if not used. All the
switch inputs of this control board including the limit switch inputs require a voltage free switch contact only. Do not
connect any switches which provide a voltage to the control board as this will damage the control board. If the inputs
are 12/24v or has long wiring associated with it use an IM-1 module to isolate it from the control board’s input. The
IM-1 is available from the manufacturer.
Powering Accessories
Accessories which require a 24v AC supply can be powered from the transformer output used to power the control
board via the isolated 24v AC supply which is connected to the DIN rail terminals as labelled. However the
transformer’s current capacity must be checked to allow for the extra power required by the accessories. Never use the
supply connected to the 24v AC supply control board terminals to power any accessory as this can interfere with the
control boards operation. (Blue Wires)
Locks & Lights
Use the lock output terminals on the din rail to switch the 12 volts to an electric lock (if fitted). The load switched by
the lock output terminals must not exceed 30v AC / DC @ 5Amps. If a electro magnetic lock is used, change one
wire on the control board lock output to the normally closed output. Use the light relay module (if fitted) to switch the
applied voltage to a light. The load switched by the light relay module must not exceed 240v AC / 30v DC @ 10
Amps.
Setting Cycle Timers & Auto Close Times
The control board has pre-set cycle times which are used to set the maximum time the controller will drive the motors
in the open and closed directions. The pre-programmed time for the open and close cycle timer’s is 60 seconds. The
control board also has a pre-set pedestrian access time of 5 seconds which is intended to open the motor connected to
M1 output only part way. If these default times do not suit your needs simply use the procedure below to adjust them.
Note the same procedure can be used to adjust the auto-close times.
1.
Place the slide switch into the “set” position
2.
Adjust the timer’s value by pressing and holding the required push button for the desired time.
3.
Repeat step 2 for the next timer (if desired).
4.
Place the slide switch back into the “RUN” position.
5.
Test operation.
Make sure that the slide switch is placed back into the “RUN” position before testing the new timer value.
As you can see the procedure used to set each timer’s value is the same only the push button used changes. Each push
button is clearly labelled underneath as to which timer’s value it sets. Note when setting the OPEN, CLOSE and
PEDESTRIAN cycle times the controller will drive the motors as if a “real” cycle is being executed. The difference
being that the motors will stop as soon as the button is released or the limit switches are reached. The OPN status LED
on the control board will flash at 1 second intervals to assist setting times. Note when setting the OPEN and CLOSE
cycle times when limit switches are used, release the push button a few seconds after the limit switch cuts motor
power. This allows for the motors to slow down over the life of the operators without the need to adjust again.
Содержание 450L
Страница 7: ...7 Operator Dimensions ...
Страница 12: ......