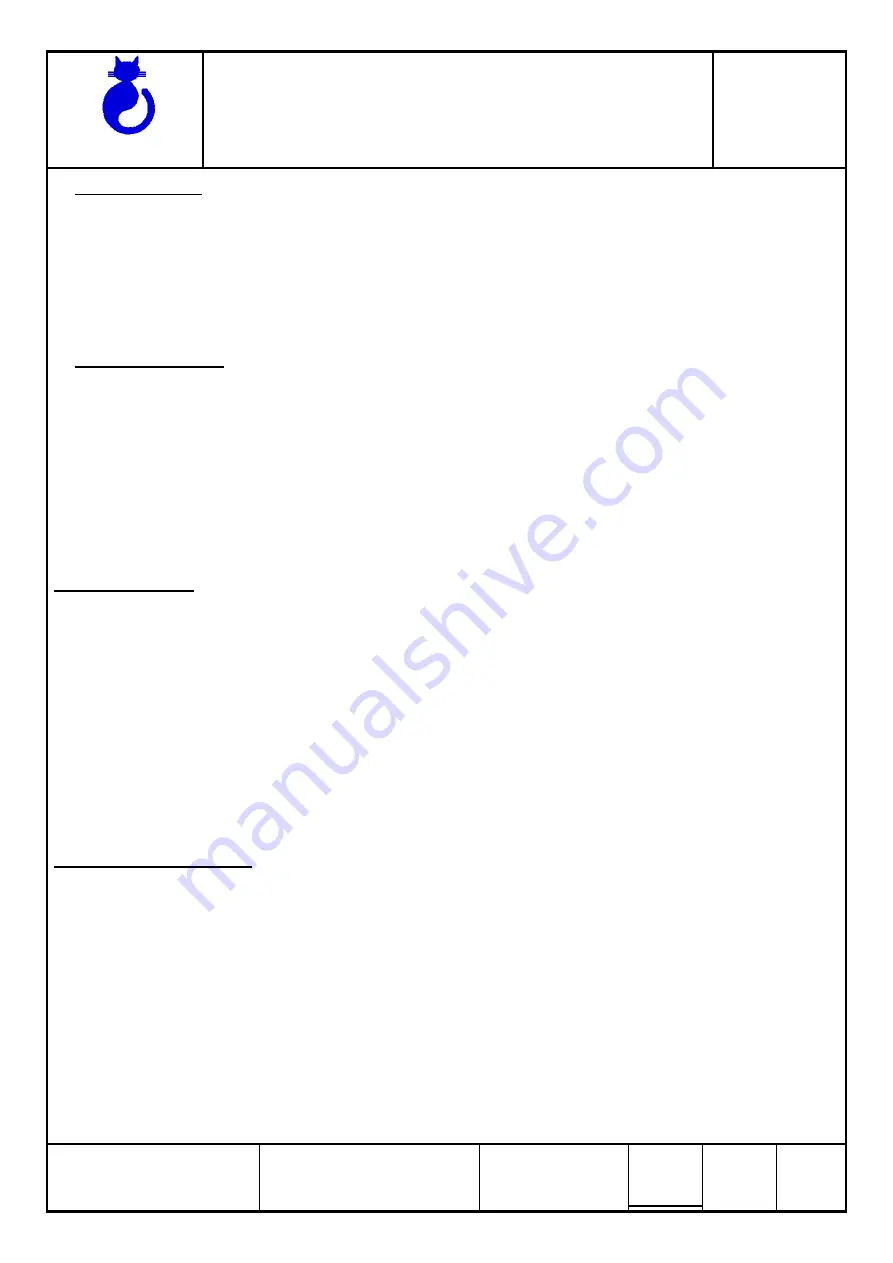
Gascat Ind Com Ltda
Installation, Operation & Maintenance Manual
Blanketing Pressure Regulator – Celtic N
MI-20
Prepared by
Checked by / Approved by
CSQ (Quality Control)
Date
Revision
Page
Vanizio
Vanizio Lizo / Celso Schettini
Rubens
31/08/09
0
3 of 11
2.3 – OPERATION
Depending on the regulator type, its valve can be positioned fully open. Consequently, when a regulator is put into
operation, the shutoff valves should be open slowly so that the regulator valve can assume its regulating position. If
the valves are quickly opened, the upstream pressure can pass downstream through the regulator and over-
pressurize downstream the main line.
All regulators, etc., should operate with the regulating spring specified by the manufacturer. This provision is
particularly important when operating relief or shutoff valves, since incorrect springs can hinder a relief valve to open
and a shutoff valve to close at the proper time.
Provisions should be taken to avoid water input through breathing and ventilation openings.
2.4 – MAINTENANCE
Regulators and valves contain gases at pressures that sometimes are higher than the atmospheric pressure.
Before trying to investigate any problem or to perform service maintenance of the equipment, they should be safely de-
pressurized. Furthermore, as most gases can be flammable, poisonous, corrosive, or somehow, dangerous, it may be
necessary to purge the installation with an inert gas, as nitrogen. Special precautions are necessary for operation with
oxygen or hydrochloric gas and the user should be reassured that appropriate procedures are implemented.
Eventually, it is not enough to isolate the high-pressure device, since high pressures can be retained downstream
of isolation valves. Do not try to remove covers, plugs, etc., before these parts are properly freed-up. Even so, it is
advisable to consider if high-pressure gas can be present at the time of removal of covers and plugs.
Most regulators use spiral springs as the loading device. It is important to reduce the load of these springs relieving
their loaders as much as possible. In some cases, some residual load may last, even though the spring is relaxed to
the limits of its housing.
3 – INTRODUCTION
The Celtic N Regulator construction is extremely compact and entirely built in stainless steel AISI 316 material. It
has a single internal pilot and can be supplied with a 5-µm filter installed at the pilot input. Some components are
polished nearly to sanitary finish, for higher durability. Due to its compact size and small weight, the regulator does not
require special brackets for installation and is widely applicable in the Chemical and Oil Industry.
Celtic N regulators are used in applications that require injection of an inert gas into storage tanks, thereby
creating a neutral atmosphere over the upper level of the liquid at rest inside the tank, or the gas is pumped out of the
tank; the positive-pressure gas blanket prevents contamination of the stored product by the external environment, or
the formation of an explosive atmosphere within the vapor space over the product stored inside the tank.
The regulator can control and maintain pressure, in the range of 5 mmWC (0.5mbar) to 150 mmWC (15mbar),
with a measurement uncertainty up to +1.5 mmWC of the set pressure.
Due to its top-entry feature, there is no need to remove it from the line for maintenance or replacement of parts.
This characteristic greatly facilitates maintenance.
For information on CELTIC N sizing, technical characteristics and specifications, please refer to the product
specific catalog.
4 – OPERATION PRINCIPLE
The Celtic N regulator, with internal pilot directly actuated by the sensor diaphragm, monitors and controls the
vapor pressure of the vapor space over the liquid surface of a liquid within a tank. If small pressure variations occur in
this vapor layer, for example, when the tank cools and vapor of the stored product condenses, the regulator internal
pilot, or the regulator, will return the pressure to the regulated setpoint.
When the liquid is pumped out of the tank, the vapor space pressure on the liquid surface decreases quickly, which
is perceived by the regulator sensor diaphragm that activates the internal pilot at the same time.
This pilot, fed by the inlet pressure through a calibrated orifice, actuates to restore this pressure, but since the flow
required to restore this pressure is larger than the capacity of the pilot shutter, or of the calibrated orifice, the pressure
applied to the piston falls rapidly, allowing full passage of the blanketing gas to the tank. When the tank preset
pressure, set by the adjusting screw, is reached, this pressure, of a few millimeters of water column, raises the
regulator-sensing diaphragm causing the pilot to close, thus rapidly raising the pressure on the piston, which shuts the
Regulator. The piston spring and the pilot shutter spring provide a positive shutting load leading to absolute tightness.
Small pressure variations are perceived as a function of the large area of the sensor diaphragm, what guarantees
a much faster response either to the regulator opening or closing.