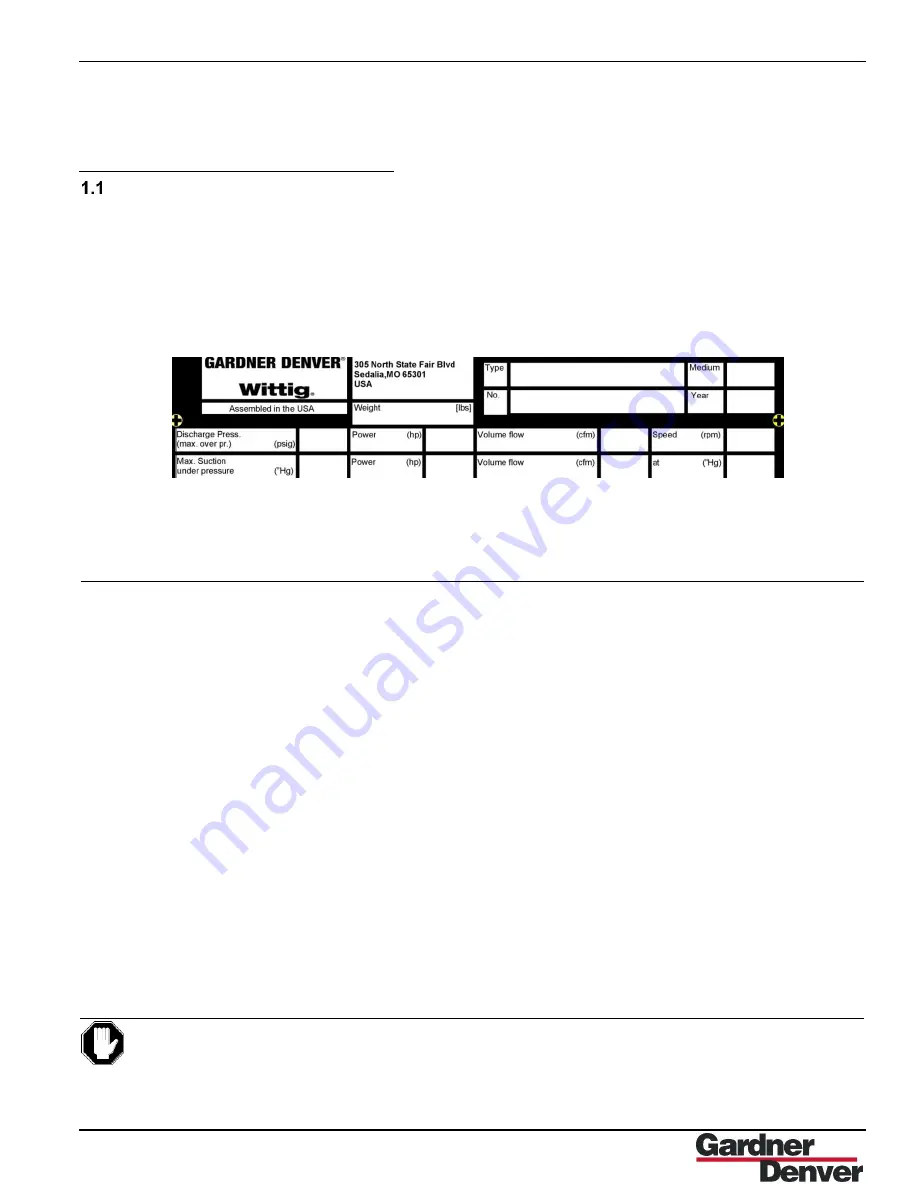
BA-
45.01.0 • US •01/15
1-1
1. Technical data
The compressor/Vacuum pumps in the series RFW
are water-cooled, fresh-oil lubricated rotary vane
compressors.
On the rating plate of each machine you will find, in
addition to the machine number, the most important
data.
Figure 1-1:
Rating Plate of RFW 150…260
Data for the type series
Rotary Compressor & Vacuum Pump
Type
RFW 150 DV
RFW 200 DV
RFW 260 DV
Nominal Vacuum
mbar
abs
400
400
400
Operating Vacuum for continuous operation
1)
mbar
abs
200
200
200
Max. permitted vacuum (short-term, up to 15 min. per hour)
mbar
abs
100
100
100
Max. operating pressure (gauge)
in compressor operation
2)
in compressor operation with V-belt drive
2)
bar
g
2.0
2.0
2.0
1.5
2.0
0.5
Max. Power requirement at max. operating pressure (gauge)
kw
50
70
92
Suction pressure 400 mbar
abs
Volume flow
Final overpressure
Power requirement at drive shaft
m
3
/h
bar
g
kW
820
0.0
23.0
1180
0.0
34.0
1540
0.0
41.0
Suction pressure 1000 mbar
Volume flow
Final overpressure
Power requirement at drive shaft
m
3
/h
bar
g
kW
850
0.5
30.0
1210
0.5
45.0
1570
0.5
58.0
Nominal speed
min
-1
1500
1500
1500
Mass moment of inertia
kgm
2
0.52
0.73
0.95
Sound pressure level at a distance of 7m. at 400 mbar / 0.5 bar
over pressure
db (A)
71/74
75/79
76/82
Weight with back pressure valve
kg
220
280
360
1)
Protect with a ventilating valve!
2)
Protect with a safety valve!
Data and illustrations accurate as of 01.04.1993. Subject to alterations