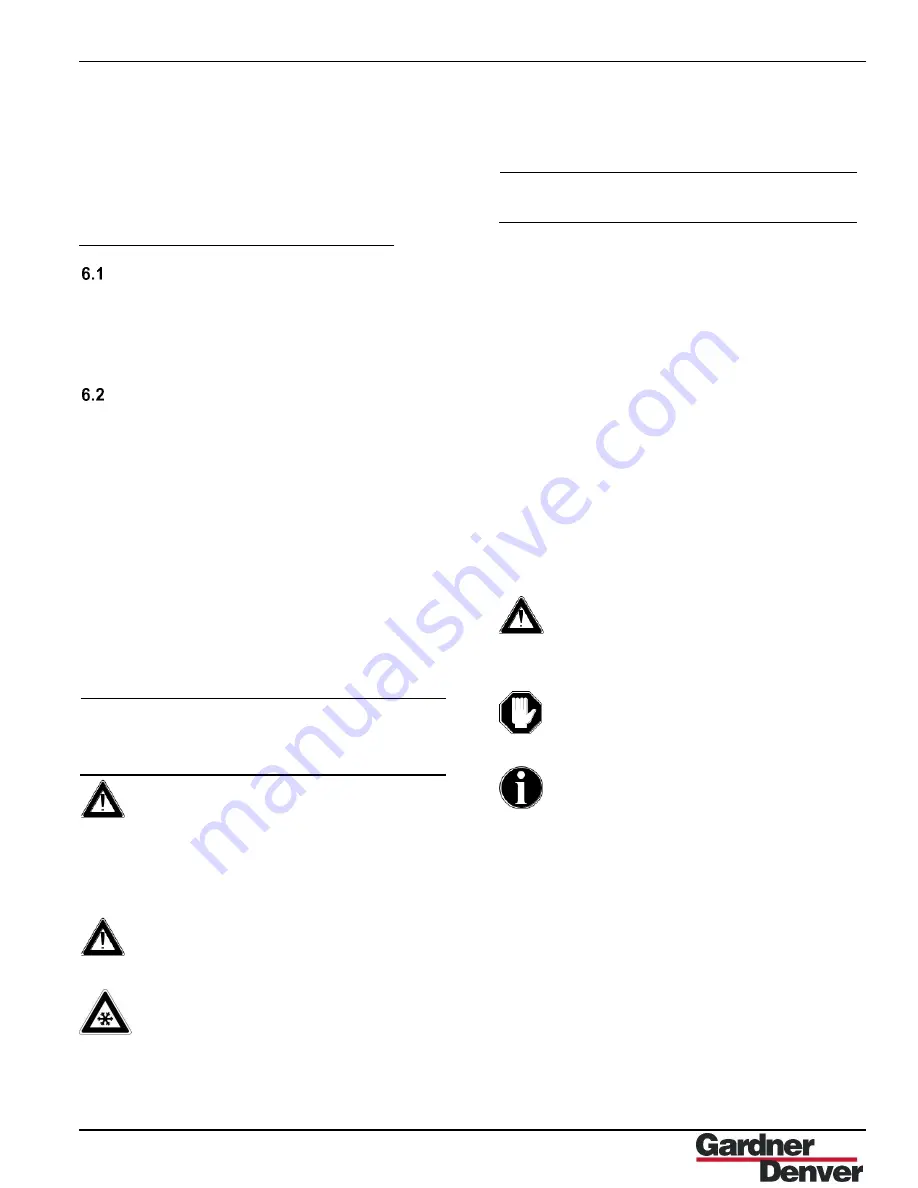
BA-
45.01.0 • US •01/15
6-1
6. Operation
Precautions for long standstill periods
Rinsing after machine has over sucked
Switching on
Normal switching on of the rotary compressor or
compressor & vacuum pump (referred to in the
following text as the “machine”) is carried out as
described in
chapter 5,
.
Regular checks
In pressure operation
Check operating excess pressure on the manometer
(for the permissible pressure, see the machine’s rating
plate).
In vacuum operation
Check the operating vacuum on the vacuum meter (for
the permissible vacuum, see the machine’s rating
plate).
Compression final temperature:
Read the final compression temperature. It is generally
approximately as follows
Operating vacuum 400 mbar
140°C
Operating over pressure 0,5 bar
120°C
Suction temperature
20°C
Depending on the operating status, the final
compression
temperature
may
be
significantly higher than the values given
(
up to approx. 200°C
)!
Drain condensate
Drain the condensate from the condensate and safety tanks.
The tank must not be under pressure when
the condensate is drained.
In the winter, the condensate may freeze.
Rotating speed
Check the operating rotation speed.
Permitted speed range
Drive by cardan shaft
1200...1500 min
-1
Other drive systems
1000...1500 min
-1
Cooling water temperature
Upon return to the cooler the maximum cooling water
temperature is 60°C.
Oil level
Check the oil level on the window of the reservoir.
If the oil level reaches the red mark, add more
lubrication oil.
For the lubrication oil specification see
5.8, lubricating
oils
.
6.2.1
Safety valve
A non-lockable safety valve must be installed in the
pressure pipe after every compressor. It must be set
so that a pressure greater than 10% above the
maximum permitted operating pressure is prevented.
The setting of the valve must be
safeguarded
against
unauthorized
or
erroneous alteration!
The safety valve must not be blocked, or
otherwise manipulated in any way.
Expelling of the entire volume flow from the
safety valve when the pressure pipe is
closed must be avoided, as harmful
pressure vibra- tions may be caused.
The safety valve must not be used as a
pressure regulation instrument.
Check the functionality of the valve during initial
operation, and thereafter once a week, by activating
the manual ventilation with the machine operating
system.