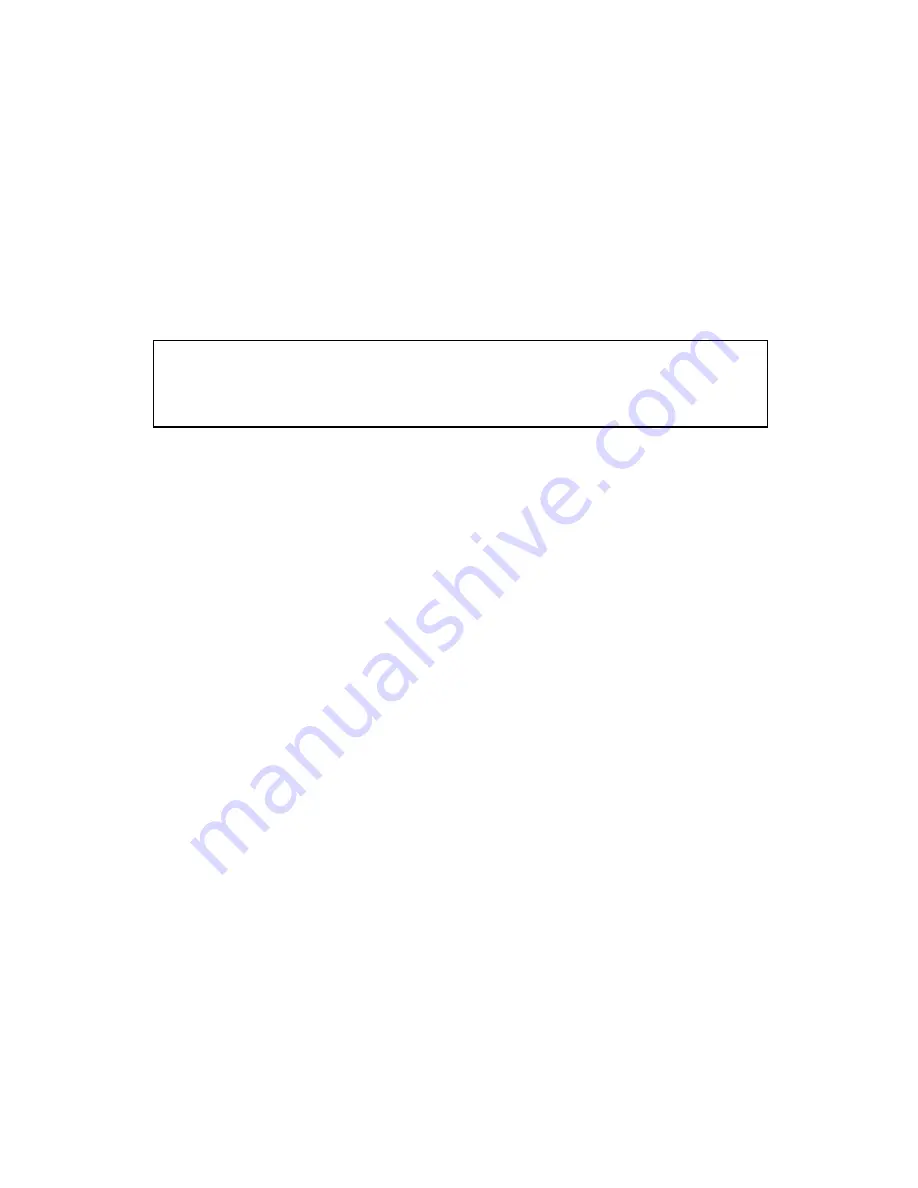
13-11-608 Page 35
Blowdown Valve
(g) - This solenoid valve provides purging air to the compressor during unloaded
operation. It also depressurizes the air/water reservoir during unloaded or halted operation. It is
governed by the AUTO SENTRY W controller.
Aux. Blowdown Valve
(h) – This solenoid valve depressurizes rapidly the air/water reservoir during the
initial phase of the unloading cycle. It is energized by the auxiliary pressure switch.
Aux. Pressure Switch
(j) – This device senses the air reservoir pressure and controls the closing level
of the auxiliary blowdown valve during the latter phase of the unloading cycle. Its setting (see Figure 4-3,
page 35) is adjusted to maintain the compressor inlet pressure within 0 to 11” Hgv during unloaded
operation. It is housed in the starter control box, but it is independent from the AUTO SENTRY W
controller.
Model Power – bhp
40
40
50
50
60
60
75
75
Line Pressure – psig
100
125
100
125
100
125
100
125
Receiver Pressure – psig
23
20
27
20
31
25
36
32
Figure 4-3 – AUXILIARY PRESSURE SWITCH/RECEIVER UNLOADED PRESSURE TABULATION
Check Valve (Aux Blowdown)
(i, next to b) – This check valve prevents back flow of air from the
airend immediately after halting operation.
Minimum Pressure Valve
(k) - This spring-loaded, pressure-balance device remains closed with
compressor discharge pressures under 65 to 70 psig, thus ensuring back pressure to promote injection
water flow for cooling and sealing. The valve also prevents back flow of system air when the compressor
is not running.
Inlet Valve
(b) – This device modulates the flow of air entering the compressor and checks the back
flow of air immediately after halting compressor operation. Its piston assembly is energized with air from
the subtractive valve (during modulation) or with air from the main blowdown valve (during unloaded
operation).
Subtractive Valve
(q) – This device produces a variable pneumatic signal (0 to 20 psig) in proportion to
a system pressure rise (0 to 10 psig) above its set pressure. It is used to control the flow modulating
action of the inlet valve. The device is adjusted as follows:
•
Loosen the locknut securing the adjusting stem of the subtractive valve and screw the latter
in several turns – this will prevent the valve from opening during adjustment. This is also the
way to deactivate the device by adjusting its pressure setting beyond the expected package
operating range.
•
Operate the compressor until the desired discharge pressure is achieved – in case the supply
of air exceeds the demand, bleed some of the discharge air to achieve the target system
pressure.
•
Back-out the adjustment stem until the subtractive valve starts to bypass air – the adjacent
pressure gauge should register movement of less than 1 psig. Now the device is ready to
feed a proportional air signal to the inlet poppet valve as the system pressure builds beyond
the present level.
•
Tighten the lockout to secure the position of the adjustment stem.
The subtractive valve can be disassembled and the diaphragm and ports cleaned.
Содержание PUREAIR EWD99E
Страница 7: ...13 11 608 Page 2 Figure 1 2 PACKAGE ILLUSTRATION AIR COOLED 302EWD797 A Ref Drawing...
Страница 8: ...13 11 608 Page 3 Figure 1 3 PACKAGE ILLUSTRATION WATER COOLED 303EWD797 A Ref Drawing...
Страница 9: ...13 11 608 Page 4 Figure 1 4 WATER COOLED SCHEMATIC 300EWD797 D Ref Drawing...
Страница 10: ...13 11 608 Page 5 Figure 1 5 AIR COOLED SCHEMATIC 301EWD797 D Ref Drawing...
Страница 30: ...13 11 608 Page 25 Figure 4 2 FLOW CHART FOR SETUP PROGRAMMING 300EWC1255 Ref Drawing...
Страница 44: ...13 11 608 Page 39 301EWD546 B Ref Drawing Page 2 of 2...
Страница 45: ...13 11 608 Page 40 Figure 4 5 WIRING DIAGRAM WYE DELTA WITH EXPANSION BOARD 302EWD546 B Ref Drawing Page 1 of 2...
Страница 46: ...13 11 608 Page 41 302EWD546 B Ref Drawing Page 2 of 2...
Страница 47: ...13 11 608 Page 42 Figure 4 6 WIRING DIAGRAM FULL VOLTAGE LESS STARTER 303EWD546 B Ref Drawing Page 1 of 2...
Страница 48: ...13 11 608 Page 43 303EWD546 B Ref Drawing Page 2 of 2...