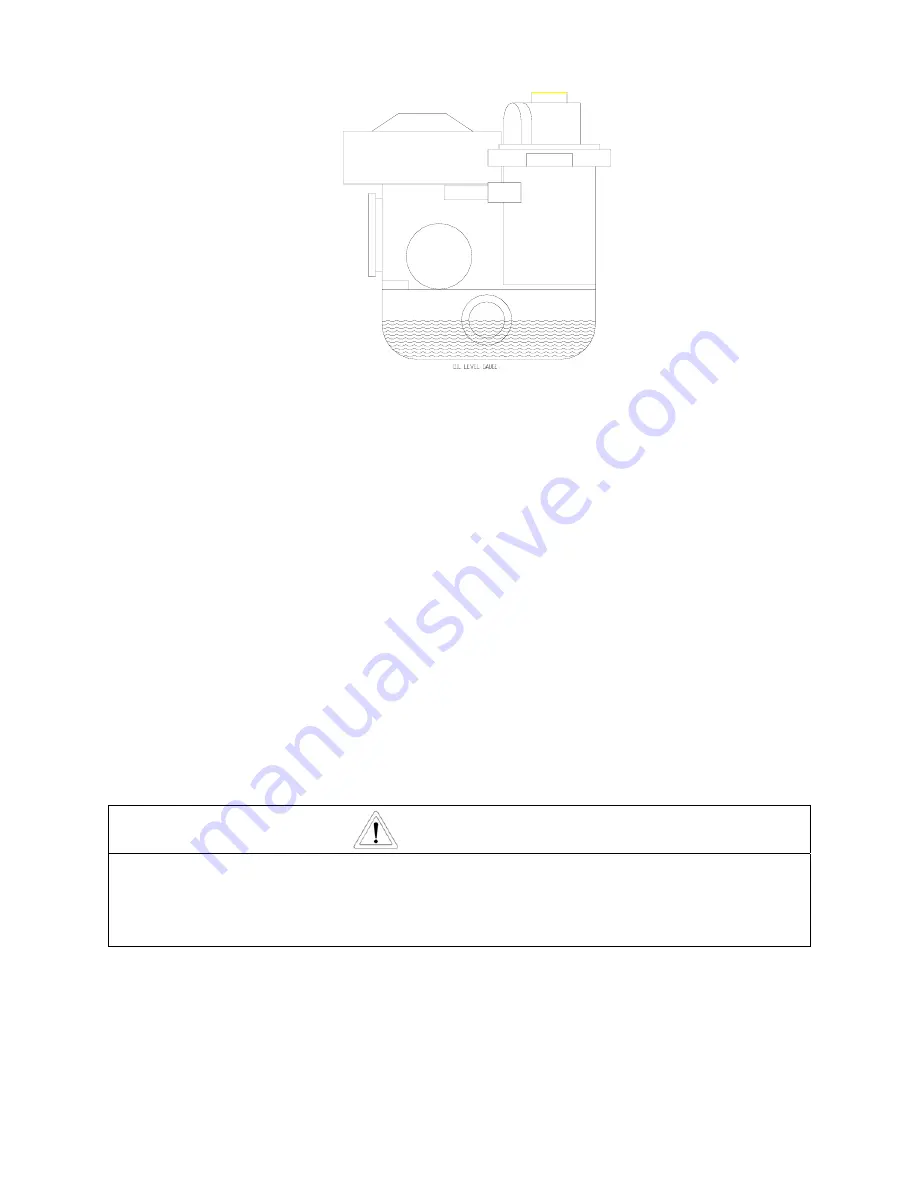
13-8-619 Page 29
306EBA797-A
(Ref. Drawing)
Figure 5-3 – OIL LEVEL GAUGE
OIL LEVEL GAUGE
(Figure 5-3) - The oil level gauge indicates the amount of oil in the oil reservoir.
Read oil level only when unit is shut down and the air/oil mixture has separated. Add oil only when the oil
level is at the bottom of the site glass. Drain oil only when the oil level is above the top of the site glass.
MOISTURE IN THE OIL SYSTEM
- In normal humidity and with normal operating temperatures and
pressures, the thermal mixing valve controls the oil temperature and prevents moisture contamination of
the oil. Unusual cooling of the oil reservoir, short loaded cycle in high humidity or malfunctions of the
thermal valve may result in moisture in the oil system which is detrimental to compressor lubrication and
could cause oil carryover. If moisture is observed in the oil reservoir, drain the moisture and correct the
condition causing the accumulation.
See “Compressor Oil System Check,” page 33 and “Thermal Control (Thermostatic Mixing) Valve,” page
31.
COMPRESSOR OIL
FILTER
(Figure 1-2, page 2) - This replaceable element filter is a vital part in
maintaining a trouble-free compressor, since it removes dirt and abrasives from the circulated oil.
CAUTION
Improper oil filter maintenance will cause damage to equipment. Replace filter
element every 1000 hours of operation. More frequent replacement could be
required depending on operating conditions. A filter element left in service too
long may damage equipment.
Use only the replacement element shown on the filter tag or refer to the parts list for the part number.
Use the following procedure to replace the filter element. Do not disturb the piping.
Содержание INTEGRA EFB99A
Страница 9: ...13 8 619 Page 2 300EFB797 A Ref Drawing Figure 1 2 COMPRESSOR ILLUSTRATION...
Страница 12: ...13 8 619 Page 5 DECALS 206EAQ077 212EAQ077 218EAQ077 211EAQ077 207EAQ077...
Страница 13: ...13 8 619 Page 6 DECALS 216EAQ077 217EAQ077 222EAQ077 221EAQ077 208EAQ077...
Страница 30: ...13 8 619 Page 23 300EFB542 C Ref Drawing Figure 4 3 WIRING DIAGRAM...